-
- News
- Books
Featured Books
- smt007 Magazine
Latest Issues
Current IssueIntelligent Test and Inspection
Are you ready to explore the cutting-edge advancements shaping the electronics manufacturing industry? The May 2025 issue of SMT007 Magazine is packed with insights, innovations, and expert perspectives that you won’t want to miss.
Do You Have X-ray Vision?
Has X-ray’s time finally come in electronics manufacturing? Join us in this issue of SMT007 Magazine, where we answer this question and others to bring more efficiency to your bottom line.
IPC APEX EXPO 2025: A Preview
It’s that time again. If you’re going to Anaheim for IPC APEX EXPO 2025, we’ll see you there. In the meantime, consider this issue of SMT007 Magazine to be your golden ticket to planning the show.
- Articles
- Columns
Search Console
- Links
- Media kit
||| MENU - smt007 Magazine
Strategies for Addressing Flex Circuit Assembly Pain Points
April 13, 2017 | Stephen Las Marias, I-Connect007Estimated reading time: 4 minutes
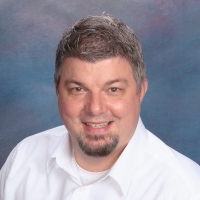
In an interview with SMT Magazine, Steve Fraser, VP of Operations at Firstronic, discusses the challenges they face in flex circuit assembly and their strategies to ensure the reliability of the products.
Stephen Las Marias: What do you think are the major challenges in flex-circuit assembly?
Steve Fraser: We are predominately working with rigid-flex circuit automotive lighting applications. One of the issues we are seeing is that while these boards used to be shipped in a rigid panel, they are increasingly coming in non-rigid panels. This is because LEDs tend to use metal backing rather than FR4. The cost of metal is high enough that to reduce material cost, panels are shipped in flex format. However, the tradeoff is that when this is done, the flex panels must be palletized. This drives added tooling cost since it requires 25–30 pallets to run product on an SMT line without impacting throughput. Post-SMT, panels/boards then require flat trays and carts for movement among production operations, which may or may not be compatible with a manufacturer’s existing PCBA handling equipment.
An additional challenge is that the bonding material used to bond to the rigid portion is moisture sensitive, which means the product needs to be kept in sealed-in bags until ready for use in production. Typically, they must pass through the SMT process within four hours of opening to prevent unacceptable moisture absorption. Consequently, if you have serialization requirements, you have serialize product inline or run small batches. In lieu of this, pre-SMT baking is required which adds time and cost and is a non-value added process. Finally, we have some applications that have bend and form requirements for the rigid portions. We receive them flat, bend them first and then run them through the line formed, which increases the complexity of the required pallet.
Las Marias: What specific steps in a flexible circuit assembly process have the biggest effect on yields?
Fraser: First, it is important to ensure the board hasn’t absorbed moisture prior to running through SMT process. Second, the pallet design must be appropriate for running the board through the SMT process and work with the test fixture. Third, it is important to develop a detailed handling plan that considers every step from when someone takes the board out of the out of the package through placing it in the finished goods package. Finally, finished goods packaging design needs to protect the product in shipment and be easy to load and unload without stressing solder joints.
Las Marias: How do assemblers address these challenges? What parameters should be considered?
Fraser: The reflow soldering process is straightforward. If you are running double-sided reflow, you really need to have your profiles dialed in. But for the most part, if you have good process in place, it isn’t significantly more challenging.
Las Marias: How different is the flex circuit assembly from the standard PCB assembly, and what are the important factors to consider?
Fraser: Support and handling are more complex. In test, you need to design fixtures that will accommodate a carrier to lift the flex panel from the fixture without stressing it. Verifying stress and strain requirements at test is also critical.
Las Marias: What about the challenges with respect to flexible circuit materials?
Fraser: Moisture sensitivity can be an issue with the bonding material.
Las Marias: Do customers call out a specific brand name of material to use when dealing with flexible printed circuits?
Fraser: Yes, most of our customers specify material and board house.
Las Marias: What has the greatest impact on the quality of flexible circuit assemblies?
Fraser: When you are doing final assembly, you need to make sure that the board functions properly before beginning the mechanical assembly process and that the final mechanical assembly process doesn’t damage it. The more a flex circuit is handled, the higher the probability of operator incurred defects or stress fractures that could cause failures in the field, so minimizing the possibility that a mechanical assembly step must be reworked is far more important than with a traditional PCBA.
Las Marias: In which end markets are you seeing increasing use of flexible circuits?
Fraser: In our case, exterior and interior automotive lighting.
Las Marias: What should OEMs consider when choosing an assembly partner for their flex circuit assemblies/projects?
Fraser: Does that partner have demonstrated capabilities in that application? Also, it is important to understand that less defects are likely to occur if the contract manufacturer does final assembly as compared to shipping the flex circuits, because this final mechanical assembly provides a rigid structure to ship the flex board on and eliminates additional handling of packaging and unpackaging the PCBA. Additionally, doing it all in one place minimizes handling and over-processing, because if the product is shipped to a second facility, it must be packaged, retested and often repalletized for the next assembly step.
Las Marias: Are there new technologies out there that will significantly impact or benefit the flex circuit assembly process?
Fraser: While not directly related only to flex, more automotive lighting applications are using LEDs and often these are mounted on flex or rigid flex because of packaging needs. Reflow ovens with vacuum process are beneficial in terms of pulling air pockets out of solder joint to eliminate voids. This level of defect of mitigation is good for both flex circuits and traditional PCBAs.
Las Marias: Thank you very much, Steve.
Fraser: Thank you.
This article was originally published in the March 2017 issue of SMT Magazine.
Suggested Items
Indium’s Karthik Vijay to Present on Dual Alloy Solder Paste Systems at SMTA’s Electronics in Harsh Environments Conference
05/06/2025 | Indium CorporationIndium Corporation Technical Manager, Europe, Africa, and the Middle East Karthik Vijay will deliver a technical presentation on dual alloy solder paste systems at SMTA’s Electronics in Harsh Environments Conference, May 20-22 in Amsterdam, Netherlands.
SolderKing Achieves the Prestigious King’s Award for Enterprise in International Trade
05/06/2025 | SolderKingSolderKing Assembly Materials Ltd, a leading British manufacturer of high-performance soldering materials and consumables, has been honoured with a King’s Award for Enterprise, one of the UK’s most respected business honours.
Knocking Down the Bone Pile: Gold Mitigation for Class 2 Electronics
05/07/2025 | Nash Bell -- Column: Knocking Down the Bone PileIn electronic assemblies, the integrity of connections between components is paramount for ensuring reliability and performance. Gold embrittlement and dissolution are two critical phenomena that can compromise this integrity. Gold embrittlement occurs when gold diffuses into solder joints or alloys, resulting in mechanical brittleness and an increased susceptibility to cracking. Conversely, gold dissolution involves the melting away of gold into solder or metal matrices, potentially altering the electrical and mechanical properties of the joint.
'Chill Out' with TopLine’s President Martin Hart to Discuss Cold Electronics at SPWG 2025
05/02/2025 | TopLineBraided Solder Columns can withstand the rigors of deep space cold and cryogenic environments, and represent a robust new solution to challenges facing next generation large packages in electronics assembly.
BEST Inc. Reports Record Demand for EZReball BGA Reballing Process
05/01/2025 | BEST Inc.BEST Inc., a leader in electronic component services, is pleased to announce they are experiencing record demand for their EZReball™ BGA reballing process which greatly simplifies the reballing of ball grid array (BGA) and chip scale package (CSP) devices.