-
- News
- Books
Featured Books
- smt007 Magazine
Latest Issues
Current IssueWhat's Your Sweet Spot?
Are you in a niche that’s growing or shrinking? Is it time to reassess and refocus? We spotlight companies thriving by redefining or reinforcing their niche. What are their insights?
Moving Forward With Confidence
In this issue, we focus on sales and quoting, workforce training, new IPC leadership in the U.S. and Canada, the effects of tariffs, CFX standards, and much more—all designed to provide perspective as you move through the cloud bank of today's shifting economic market.
Intelligent Test and Inspection
Are you ready to explore the cutting-edge advancements shaping the electronics manufacturing industry? The May 2025 issue of SMT007 Magazine is packed with insights, innovations, and expert perspectives that you won’t want to miss.
- Articles
- Columns
- Links
- Media kit
||| MENU - smt007 Magazine
Voiding Control at High-Power Die-Attach Preform Soldering
May 17, 2017 | Dr. Arnab Dasgupta, Elaina Zito, and Dr. Ning-Cheng Lee, Indium CorporationEstimated reading time: 4 minutes
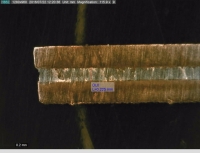
Assembly of components with large pads, such as high-brightness LEDs or high-power dies, often is soldered with preforms. Solder preforms are used to lower voiding and to lower flux fumes that can be generated by solder paste. The use of solder preforms also result in better thermal and electrical conductivity compared to Ag epoxy. This is particularly true when the joints are to be formed within a cavity.
Voiding in the solder joint is a concern for high-reliability and high-performance devices. In this study, voiding behavior of large pad high-power devices was simulated with copper (Cu) coupon to Cu coupon sandwiches. A flux-coated preform was studied in this assembly, with variation in solder alloy type, quantity of solid flux coated on solder preform, Cu coupon pre-oxidation extent, reflow temperature, and pressure exerted onto the sandwich during reflow.
Experiment
1. Solder Alloy Type
Preforms of three solder alloys were tested: 96.5Sn/3Ag/0.5Cu (SAC305), 63Sn/37Pb, and 57Bi/42Sn/1Ag. The preform diameter was 0.906-inch, and 0.006-inch thick.
2. Flux Coating
The preform was pre-coated with a solid flux film using liquid flux at 0.5, 1.0, and 2% flux concentrations in isopropyl alcohol upon application.
3. Cu Coupon Oxidation Pre-treatment
The copper coupon (0.906-inch diameter, 0.020-inch thick) was used to simulate both die and substrate. It was pre-cleaned by soaking in a diluted HBF4 aqueous solution, followed by deionized water rinsing, and air drying. These cleaned Cu coupons were then oxidized by placing them on a 230°C hot plate for 0, 30, and 60 seconds, and five minutes prior to the soldering process.
4. Die-Attach Sandwich Setup
The high-power die-attach setup was simulated with the use of two Cu coupons, which were to be joined with a flux-coated solder preform. A 3-inch x 3-inch ceramic plate was used as a carrier. The simulated die-attach sandwich (Cu coupon on a solder preform, then placed on another Cu coupon) was placed on the carrier. At die-attach with solder preforms, many manufacturing processes use fixtures with some weight on the die to secure the sandwich. In this study, metal weight varying from 0 to 100 grams was placed on the top of the sandwich to simulate the fixture weight. Paper cardboard was placed on top of the die for heat insulation, if a weight was used.
5. Reflow Peak Temperature
The sandwich on the carrier was placed on a 5-zone, in-line contact reflow oven, and then sent through the reflow oven with various peak temperatures as follows:
- SAC305: 240°C, 250°C, and 260°C
- 63Sn/37Pb: 205°C, 215°C, and 225°C
- 57Bi/42Sn/1Ag: 160°C, 170°C, and 180°C
6. Reflow Under Various Pressures
For SAC305, various weights were placed on top of the sandwiches at reflow: 0, 10, 30, and 100 grams. For this set of assembly, freshly cleaned Cu coupons, 0.5% flux concentration, and a peak temperature of 240°C were used. Ten sandwiches were reflowed for each condition. For 63Sn/37Pb and 57Bi/42Sn/1Ag, 0, 10, 20, and 30 grams of weight were used for the pressure study.
7. Assessment
After reflow, the sandwiches were examined under X-ray to determine the voiding area percentage. For SAC305, three sandwiches for each weight condition were cross-sectioned to determine the bondline thickness under various weights
Results
Effect of Weight on SAC305 System Using X-ray Images
Figure 1 shows the X-ray images of SAC305 sandwiches under various weights. Here, the flux concentration was 0.5%, the peak temperature was 240°C, and the coupons were etch-cleaned prior to use. Although 10 samples were prepared for each combination of conditions, three sandwiches were removed due to large opens in the solder joints because the image analysis software was unable to determine the voiding percentage properly. Most of the samples showed full wetting to the perimeter of coupons, and only a few showed a small fraction of non-wetting near the edge of the joints.
Figure 1: X-ray images for SAC305 soldered sandwiches processed with various weights on top of samples.
Most of the voids showed plain vacancy, except for a few samples where some spotty light-colored solder were seen within the voids, such as in the third image of the 10-gram series and the first image of the 30-gram series. The spotty solder islands were attributed to the once-formed liquid joints, but were wiped out partially by expanding voids.
In most images, concentric ring textures can be seen clearly, indicating the Cu coupons may be warped. Also, the joint appeared to be thicker toward the center, and the solidification may have been developed stepwise from the edge toward the center.
1. Bondline Thickness (BLT): The 100-gram weight samples showed a much lighter shade of color than the other three weight samples, suggesting much thinner solder BLT data for SAC305 joints under various weights. The sandwich samples were cross-sectioned, as exemplified in Figure 2, with the BLT measured at both the edges and the center. The average value was calculated to represent the BLT of a given weight condition.
Page 1 of 3
Suggested Items
Driving Innovation: Direct Imaging vs. Conventional Exposure
07/01/2025 | Simon Khesin -- Column: Driving InnovationMy first camera used Kodak film. I even experimented with developing photos in the bathroom, though I usually dropped the film off at a Kodak center and received the prints two weeks later, only to discover that some images were out of focus or poorly framed. Today, every smartphone contains a high-quality camera capable of producing stunning images instantly.
Hands-On Demos Now Available for Apollo Seiko’s EF and AF Selective Soldering Lines
06/30/2025 | Apollo SeikoApollo Seiko, a leading innovator in soldering technology, is excited to spotlight its expanded lineup of EF and AF Series Selective Soldering Systems, now available for live demonstrations in its newly dedicated demo room.
Indium Corporation Expert to Present on Automotive and Industrial Solder Bonding Solutions at Global Electronics Association Workshop
06/26/2025 | IndiumIndium Corporation Principal Engineer, Advanced Materials, Andy Mackie, Ph.D., MSc, will deliver a technical presentation on innovative solder bonding solutions for automotive and industrial applications at the Global Electronics A
Fresh PCB Concepts: Assembly Challenges with Micro Components and Standard Solder Mask Practices
06/26/2025 | Team NCAB -- Column: Fresh PCB ConceptsMicro components have redefined what is possible in PCB design. With package sizes like 01005 and 0201 becoming more common in high-density layouts, designers are now expected to pack more performance into smaller spaces than ever before. While these advancements support miniaturization and functionality, they introduce new assembly challenges, particularly with traditional solder mask and legend application processes.
Knocking Down the Bone Pile: Tin Whisker Mitigation in Aerospace Applications, Part 3
06/25/2025 | Nash Bell -- Column: Knocking Down the Bone PileTin whiskers are slender, hair-like metallic growths that can develop on the surface of tin-plated electronic components. Typically measuring a few micrometers in diameter and growing several millimeters in length, they form through an electrochemical process influenced by environmental factors such as temperature variations, mechanical or compressive stress, and the aging of solder alloys.