-
- News
- Books
Featured Books
- smt007 Magazine
Latest Issues
Current IssueSupply Chain Strategies
A successful brand is built on strong customer relationships—anchored by a well-orchestrated supply chain at its core. This month, we look at how managing your supply chain directly influences customer perception.
What's Your Sweet Spot?
Are you in a niche that’s growing or shrinking? Is it time to reassess and refocus? We spotlight companies thriving by redefining or reinforcing their niche. What are their insights?
Moving Forward With Confidence
In this issue, we focus on sales and quoting, workforce training, new IPC leadership in the U.S. and Canada, the effects of tariffs, CFX standards, and much more—all designed to provide perspective as you move through the cloud bank of today's shifting economic market.
- Articles
- Columns
- Links
- Media kit
||| MENU - smt007 Magazine
Electrolube Launches Complete Cleaning Solution for Silicone Wafer Assemblers
June 16, 2017 | ElectrolubeEstimated reading time: 3 minutes
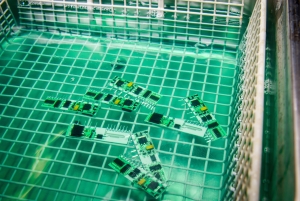
Electrolube has developed an innovative cleaning solution called Safewash Super (SWAS) for PCB wafer assemblers, following close collaboration with a number of manufacturers to considerably improve their cleaning capabilities as well as speed up throughput, reduce costs and decrease environmental impact.
While cleaning processes can vary from plant to plant, the silicone wafer manufacturers in collaboration with Electrolube all had many issues in common. These included experiencing a bottleneck in production due to a slow cleaning process, using a solvent based cleaning product—which produced disappointing cleaning outcomes as well as increased rejects and re-work—and concerns with environmental impact with regard to storage, transport, disposal and employee safety. The existing solvent-based products in use also displayed a relatively low contamination 'load bearing' capability, which resulted in a more frequent need to replace material for a fresh batch.
In a recent case study involving a major multinational wafer manufacture, Electrolube's SWAS, Safewash Super, proved how one product change can result in an entirely new cleaning process experience for wafer assemblers. This particular customer used a US made solvent-based cleaning agent in a multi chamber machine, consisting of five cleaning tanks plus a loading and unloading station. Electrolube addressed their concerns by introducing SWAS into their process. As a direct result of implementing SWAS, the customer was able to reclaim considerable floor space at their facility by reducing their existing five tank configuration to a three tank configuration (clean/QDR & QDR De-Ionised).
SWAS significantly improved the assembler’s cleaning performance with no residue on the wafer and enabled throughput to increase by as much as 50%, a vast increase assisted by the decreased time in the cleaning tank and the reduced tank configuration.
SWAS can absorb a maximum of 5%-15% of its weight of flux (RA, RMA, no-clean and water-soluble) whilst still cleaning to high military standards. Due to the product’s capacity to ‘hold’ high levels of contaminant particles, the customer effectively reduced the number of cleaning agent changes per week. Costs were reduced even further thanks to the water-based formulation of SWAS, making it cheaper to transport and dispose of after use. Designed to clean to well within the world's military cleanliness standards—ANSI-J-001B/IPC TM-650—SWAS is non-flammable, 100% ozone friendly and biodegradable. The cleaning agent is low-odour and is far safer for employees to work with and to store.
It has become very evident that SWAS is a very cost effective and technically capable cleaning product in this application, indeed for a majority of wafer manufacturers and PCB/production equipment cleaning applications. SWAS is ideally suited to removing all types of flux residues quickly and efficiently, with minimal environmental effect using low cost, readily available cleaning equipment. It is particularly well suited for the removal of very stubborn flux resides and no-clean fluxes, which can be extremely difficult to remove. Currently used by major manufacturers in a wide variety of cleaning systems, Safewash Super provides advanced cleaning performance to military cleanliness standards at minimal financial and environmental cost.
About Electrolube
Electrolube, a division of H.K. Wentworth Limited, is a leading manufacturer of specialist chemicals for electronics, automotive and industrial manufacturing. Core product groups include conformal coatings, contact lubricants, thermal management materials, cleaning solutions, encapsulation resins and maintenance and service aids.
The extensive range of electro-chemicals at Electrolube enables the company to offer a 'complete solution' to leading manufacturers of electronic, industrial and domestic devices, at all levels of the production process. Through collaboration and research, the company is continually developing new and environmentally friendly products for customers around the world and their commitment to developing ‘greener’ products has been endorsed by the ISO 14001 standard for the highly efficient Environmental Management System in place at the company.
Winners of the Queen’s award for Enterprise 2016, Electrolube is represented in over 55 countries with an established network of subsidiaries and distributors. By offering genuine security of scale and a reliable supply chain, the company is able to deliver a truly tailored service. For further information, please click here.
Testimonial
"The I-Connect007 team is outstanding—kind, responsive, and a true marketing partner. Their design team created fresh, eye-catching ads, and their editorial support polished our content to let our brand shine. Thank you all! "
Sweeney Ng - CEE PCBSuggested Items
Flexible Circuit Technologies to Host Free Flex Heater Webinar
08/18/2025 | Flexible Circuit TechnologiesGlobal Supplier of flexible circuits, flex design services, and assembly/box-build services, Flexible Circuit Technology will host their latest webinar, "Thermal Precision Meets Flexibility: The Technology Behind Heater Circuits" on Tuesday, August 26th, 2025 at 11 AM EDT.
A.R.T. Ltd. Nominated in Four Categories at 2025 Instrumentation and Electronics Industry Awards
08/11/2025 | A.R.T. Ltd.Advanced Rework Technology Ltd. (A.R.T. Ltd.), a leading provider of electronics training and consultancy, has been shortlisted in four categories at the 2025 Instrumentation and Electronics Industry Awards, including Industry Personality, Academic Support, Rising Star, and Best Customer Service.
EMC Taiwan Receives IPC-4101 Qualified Products Listing Certification
08/08/2025 | Global Electronics AssociationIPC’s Validation Services Program has awarded an IPC-4101 Qualified Products Listing (QPL) to Elite Materials Co. (EMC), an electronics base material manufacturing company headquartered in Taoyuan City, Taiwan.
Global Excellence in PCB Design: The Global Electronics Association Expands to Italy
08/07/2025 | Global Electronics AssociationIn today's rapidly evolving electronics industry, printed circuit boards (PCBs) serve as the critical backbone influencing the success, reliability, and time-to-market of countless products. Recognizing this essential role, the Global Electronics Association (formerly IPC), a worldwide leader in electronics standards, certification, and education, is now expanding its internationally acclaimed PCB design training to Italy.
Dana on Data: Best Practices in Interpreting Drawing Notes—‘Use Latest Revision’
08/07/2025 | Dana Korf -- Column: Dana on DataThe global nature of electronics manufacturing requires clear, consistent, and precise communication, particularly in technical documentation. An area where miscommunication often arises is in interpreting drawing notes—small lines of text with the potential to dramatically impact product quality, manufacturing efficiency, and customer satisfaction.