-
- News
- Books
Featured Books
- smt007 Magazine
Latest Issues
Current IssueSupply Chain Strategies
A successful brand is built on strong customer relationships—anchored by a well-orchestrated supply chain at its core. This month, we look at how managing your supply chain directly influences customer perception.
What's Your Sweet Spot?
Are you in a niche that’s growing or shrinking? Is it time to reassess and refocus? We spotlight companies thriving by redefining or reinforcing their niche. What are their insights?
Moving Forward With Confidence
In this issue, we focus on sales and quoting, workforce training, new IPC leadership in the U.S. and Canada, the effects of tariffs, CFX standards, and much more—all designed to provide perspective as you move through the cloud bank of today's shifting economic market.
- Articles
- Columns
- Links
- Media kit
||| MENU - smt007 Magazine
Mek SPI Features Simultaneous 2D and 3D Inspection Capabilities
September 4, 2017 | Mek (Marantz Electronics)Estimated reading time: 2 minutes
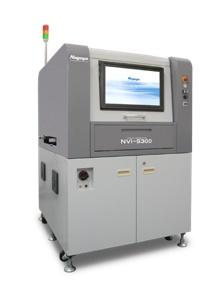
Mek (Marantz Electronics) has launched its latest automated solder paste inspection (SPI) system—the Model S2—which features patented third generation sensor technology that enables unique, simultaneous 2D and 3D inspection. It will be on display for the first time at Productronica in Munich, Hall A2 Booth 402.
The new ISO-Spector S2 utilizes the latest in 12 Mega Pixel camera technology. A fibre optic link allows for a 32 gigabit image data transfer speed.
The S2 delivers the highest quality 2D colour imaging using Episcopic and low angle diffuse RGB lighting systems that remove all specular reflections from solder fluxes and solder mask. Shadow free violet/blue dual lasers provide precise and repeatable 3D images. Available with standard resolution of 18/9µm lens resolution for inspection down to 01005 pad geometries or optionally with 12/6µm for pad geometries down to 008004. On the fly resolution switching allows the efficient inspection of mixed technology PCB’s.
Synthetic color imaging allows the simplification of color extraction of solder mask, silk screen and solder and isolates the solder to be measured, even below zero reference.
The S2 moves SPI forwards from a means of process control to one of production control. Using the Mek S2 and the real-time feedback provided by the SPC-One SPC package the user can narrow tolerances in the print process by adopting automatically to the actual process capability, bringing the real world of printing into its tolerances. Tighter tolerances over the whole PCB, enable the user to monitor process drift which was previously difficult or impossible to capture. This process is especially useful for users of jet style paste printers. The S2 can quickly adjust to changes made in the jetting program without completely reprogramming the inspection parameters. Variations in the jet printing process are immediately visible and fed back.
SPI equipment is essential to monitor and control the most critical, error prone process step in manufacturing defect-free electronic assemblies; solder paste printing. The interception of print defects reduces rework costs, delivers instant yield improvement and accelerates ROI.
About Mek (Marantz Electronics Ltd)
A former division of Marantz well known for its high quality Audio/Video products, Mek Japan (Marantz Electronics Kabushiki Kaisha), developed its first AOI system in 1994. Developed to inspect PCB assemblies for correct component placement and soldering, the company’s original AOI system was designed for use in Marantz factories. Proving to be a highly successful, cost-effective alternative to traditional human inspection, Mek developed its first generation commercial system in 1996. With a steadily growing installed base, MEK Japan and its European/American headquarters, Mek, have sold over 6000 units worldwide to date. Now well established as a leading force in AOI technologies, the company also manufactures a 5D post-print SPI system which combines 3D and 2D image processing methodologies to deliver unprecedented defect detection. At the beginning of March 2014 the company opened US offices in Las Vegas.
Testimonial
"The I-Connect007 team is outstanding—kind, responsive, and a true marketing partner. Their design team created fresh, eye-catching ads, and their editorial support polished our content to let our brand shine. Thank you all! "
Sweeney Ng - CEE PCBSuggested Items
Indium Corporation Promotes Two Leaders in EMEA (Europe, Middle East, and Africa) Markets
08/05/2025 | Indium CorporationWith its commitment to innovation and growth through employee development, Indium Corporation today announced the promotions of Andy Seager to Associate Director, Continental Sales (EMEA), and Karthik Vijay to Senior Technical Manager (EMEA). These advancements reflect their contributions to the company’s continued innovative efforts with customers across Europe, the Middle East, and Africa (EMEA).
MacDermid Alpha Electronics Solutions Unveils Unified Global Website to Deepen Customer, Talent, and Stakeholder Engagement
07/31/2025 | MacDermid Alpha Electronics SolutionsMacDermid Alpha Electronics Solutions, the electronics business of Elements Solutions Inc, today launched macdermidalpha.com - a unified global website built to deepen digital engagement. The launch marks a significant milestone in the business’ ongoing commitment to delivering more meaningful, interactive, and impactful experiences for its customers, talent, and stakeholders worldwide.
KOKI to Showcase Analytical Services and New HF1200 Solder Paste at SMTA Guadalajara 2025
07/31/2025 | KOKIKOKI, a global leader in advanced soldering materials and process optimization services, will exhibit at the SMTA Guadalajara Expo & Tech Forum, taking place September 17 & 18, 2025 at Expo Guadalajara, Salón Jalisco Halls D & E in Guadalajara, Mexico.
Weller Tools Supports Future Talent with Exclusive Donation to SMTA Michigan Student Soldering Competition
07/23/2025 | Weller ToolsWeller Tools, the industry leader in hand soldering solutions, is proud to announce its support of the upcoming SMTA Michigan Expo & Tech Forum by donating a limited-edition 80th Anniversary Black Soldering Set to the event’s student soldering competition.
Koh Young Appoints Tom Hattori as President of Koh Young Japan
07/21/2025 | Koh YoungKoh Young Technology, the global leader in True 3D measurement-based inspection solutions, announced the appointment of Tom Hattori as President of Koh Young Japan (JKY).