-
- News
- Books
Featured Books
- smt007 Magazine
Latest Issues
Current IssueSupply Chain Strategies
A successful brand is built on strong customer relationships—anchored by a well-orchestrated supply chain at its core. This month, we look at how managing your supply chain directly influences customer perception.
What's Your Sweet Spot?
Are you in a niche that’s growing or shrinking? Is it time to reassess and refocus? We spotlight companies thriving by redefining or reinforcing their niche. What are their insights?
Moving Forward With Confidence
In this issue, we focus on sales and quoting, workforce training, new IPC leadership in the U.S. and Canada, the effects of tariffs, CFX standards, and much more—all designed to provide perspective as you move through the cloud bank of today's shifting economic market.
- Articles
- Columns
- Links
- Media kit
||| MENU - smt007 Magazine
Rehm Rigorously Inspects Electronics Components
September 4, 2017 | Rehm Thermal SystemsEstimated reading time: 3 minutes
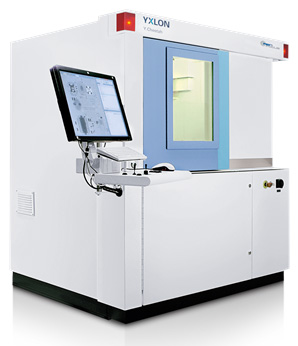
X-ray analysis of circuit boards has now become one of the most important methods in the manufacturing process for quality assurance of soldering, to visually check for pores and voids. The next step is analysis using 3D methods such as laminography and computer tomography. Customers are now able to closely examine their boards in the Technology Center at Rehm Thermal Systems by using the new Y. Cheetah μHD CT X-ray inspection system from YXLON.
Voids have a huge effect on the quality of the solder joint, therefore automotive manufacturers are increasingly setting acceptance limits on components. Not everyone is fortunate enough to have the necessary technical equipment. That is why Rehm Technology Center offers customers the opportunity to thoroughly inspect boards and jointly perfect their processes. A wide range of SMD and inspection equipment can be used under professional supervision for fault management. Solder joints can be examined in detail using the new YXLON Cheetah μHD X-ray inspection system, which enables high-resolution, non-destructive, real-time microfocus X-ray inspection of components and sub-assemblies, circuit boards, electronic and mechanical modules, sensors, MEMS and MOEMS as well as electromechanical components and connectors. It combines several innovative developments, such as fine-focus tube technology, a high-power target, a latest generation long-life finely calibrated flat detector and a manipulator with vibration damping, as well as eHDR inspection, micro CT and micro-laminography.
"Among other things, the radiographs help to evaluate the soldering quality and the void rates. Afterwards, we can make a decision with the customer as to whether any further vacuum processes are necessary and make fine adjustments to these processes. The system also performs the entire spectrum of state-of-the-art X-ray inspections, including laminography and computer tomography. This offers a wide range of manual and automatic inspection opportunities, such as distance measurements, layer assembly, BGA solder joint analysis as well as close inspections of the solder that don’t interfere with structures of components, conductor tracks, substrates and much more. The results obtained form the basis for successfully improving the processes. We particularly value the simplicity, flexibility and above all the accuracy of the system," emphasizes Helmut Öttl, Head of Process Development/Application at Rehm.
Using laminography, it is possible to generate precise layer images of larger or double-sided printed circuit boards as well as of multilayer semiconductor components. In particular, however, industrial computer tomography offers three-dimensional insights into test parts and thus facilitates the analysis of internal structures, dimensional measurements or set-point comparisons to CAD data. In addition to this, computer tomography also provides valuable information for the production process and enables detailed insights into the finest structures and smallest components.
"The YXLON Cheetah microfocus X-ray inspection system offers exactly what customers require: precision, flexibility, ease of use and speed. This is the only way today's modern manufacturing companies can satisfy the growing complexity of electrical and electronic test parts," says Thorsten Rother, YXLON's Market Manager.
The successful cooperation between Rehm and YXLON is the ideal basis for further joint projects with regard to vacuum technology, fault analysis and test methods.
Image: (from left) Helmut Öttl, Head of Process Development/Application (Rehm) and Thorsten Rother, Market Manager (YXLON) in front of the Y. Cheetah μHD X-ray inspection system (picture: Rehm Thermal Systems).
About YXLON International
YXLON International develops and manufactures X-ray and CT inspection systems for a wide range of applications and industries. Whether in the aerospace, automotive or electronics industries, some of the largest manufacturers are YXLON customers who rely on the quality of YXLON worldwide. CT systems have also been part of the product portfolio since 2003. YXLON is right there for their customers worldwide with headquarters in Hamburg and sales and service locations in Tokyo, Hudson (Ohio), San Jose (California), Beijing, Shanghai, Hattingen and Heilbronn as well as a representative network in more than 50 countries. Since 2007, YXLON International has been part of the COMET Group.
About Rehm Thermal System
As a specialist in the field of thermal system solutions for the electronics and photovoltaics industries, Rehm is a technology and innovation leader in the modern and economical production of electronic modules. As a globally operating manufacturer of reflow soldering systems with convection, condensation or vacuum, drying and coating systems, functional test systems, equipment for the metallization of solar cells as well as numerous customer-specific special systems, we are represented in all relevant growth markets and, as a partner with more than 25 years of industry experience, we implement innovative manufacturing solutions that set standards.
Testimonial
"Our marketing partnership with I-Connect007 is already delivering. Just a day after our press release went live, we received a direct inquiry about our updated products!"
Rachael Temple - AlltematedSuggested Items
Indium Corporation Promotes Two Leaders in EMEA (Europe, Middle East, and Africa) Markets
08/05/2025 | Indium CorporationWith its commitment to innovation and growth through employee development, Indium Corporation today announced the promotions of Andy Seager to Associate Director, Continental Sales (EMEA), and Karthik Vijay to Senior Technical Manager (EMEA). These advancements reflect their contributions to the company’s continued innovative efforts with customers across Europe, the Middle East, and Africa (EMEA).
MacDermid Alpha Electronics Solutions Unveils Unified Global Website to Deepen Customer, Talent, and Stakeholder Engagement
07/31/2025 | MacDermid Alpha Electronics SolutionsMacDermid Alpha Electronics Solutions, the electronics business of Elements Solutions Inc, today launched macdermidalpha.com - a unified global website built to deepen digital engagement. The launch marks a significant milestone in the business’ ongoing commitment to delivering more meaningful, interactive, and impactful experiences for its customers, talent, and stakeholders worldwide.
KOKI to Showcase Analytical Services and New HF1200 Solder Paste at SMTA Guadalajara 2025
07/31/2025 | KOKIKOKI, a global leader in advanced soldering materials and process optimization services, will exhibit at the SMTA Guadalajara Expo & Tech Forum, taking place September 17 & 18, 2025 at Expo Guadalajara, Salón Jalisco Halls D & E in Guadalajara, Mexico.
Weller Tools Supports Future Talent with Exclusive Donation to SMTA Michigan Student Soldering Competition
07/23/2025 | Weller ToolsWeller Tools, the industry leader in hand soldering solutions, is proud to announce its support of the upcoming SMTA Michigan Expo & Tech Forum by donating a limited-edition 80th Anniversary Black Soldering Set to the event’s student soldering competition.
Koh Young Appoints Tom Hattori as President of Koh Young Japan
07/21/2025 | Koh YoungKoh Young Technology, the global leader in True 3D measurement-based inspection solutions, announced the appointment of Tom Hattori as President of Koh Young Japan (JKY).