-
- News
- Books
Featured Books
- smt007 Magazine
Latest Issues
Current IssueSupply Chain Strategies
A successful brand is built on strong customer relationships—anchored by a well-orchestrated supply chain at its core. This month, we look at how managing your supply chain directly influences customer perception.
What's Your Sweet Spot?
Are you in a niche that’s growing or shrinking? Is it time to reassess and refocus? We spotlight companies thriving by redefining or reinforcing their niche. What are their insights?
Moving Forward With Confidence
In this issue, we focus on sales and quoting, workforce training, new IPC leadership in the U.S. and Canada, the effects of tariffs, CFX standards, and much more—all designed to provide perspective as you move through the cloud bank of today's shifting economic market.
- Articles
- Columns
- Links
- Media kit
||| MENU - smt007 Magazine
BTU's Custom Belt Furnace Capabilities on Display at Heat Treat
September 26, 2017 | BTU International, Inc.Estimated reading time: 1 minute
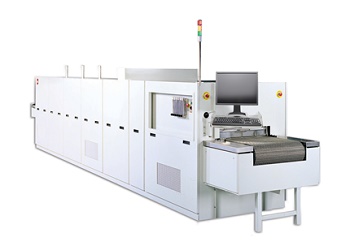
BTU International Inc. will exhibit at Heat Treat, ASM's Heat Treating Society Conference & Exhibition, which is scheduled to take place October 24–26, 2017 in Columbus, Ohio. BTU will highlight its controlled atmosphere furnaces in Booth 2524.
BTU's controlled atmosphere belt furnaces are available with temperature ranges up to 1150°C and with various process atmospheres including hydrogen and nitrogen. BTU designs and manufactures inline controlled atmosphere furnaces for a number of applications including: glass-to-metal sealing, direct bond copper, brazing, sintering and heat-treating.
BTU is the industry leader in atmosphere control for continuous furnaces. Whether dealing with high purity muffle applications or general purpose muffle-less applications, BTU has a unique set of capabilities, know-how and experience supporting precision temperature and atmosphere applications. Excellent atmosphere purity is achieved through the use of BTU’s patented gas barrier technology. In addition, BTU’s unique eductor technology can be used to enhance cooling or control process atmosphere. The end result is superior efficiency, superior performance and superior thermal uniformity.
BTU's controlled atmosphere furnaces feature BTU's proprietary WINCON control system. WINCON features a simplified user interface and incredibly powerful analytical capabilities.
About BTU International
BTU International, a wholly-owned subsidiary of Amtech Group (Nasdaq: ASYS), is a global supplier and technology leader of advanced thermal processing equipment in the electronics manufacturing market. BTU’s high-performance reflow ovens are used in the production of SMT printed circuit board assemblies and in semiconductor packaging processes. BTU also specializes in precision controlled, high-temperature belt furnaces for a wide range of custom applications, such as brazing, direct bond copper (DBC), diffusion, sintering and advanced solar cell processing. BTU has operations in North Billerica, Massachusetts, and Shanghai, China, with direct sales and service in the U.S.A., Asia and Europe. Information about BTU International is available here.
Testimonial
"In a year when every marketing dollar mattered, I chose to keep I-Connect007 in our 2025 plan. Their commitment to high-quality, insightful content aligns with Koh Young’s values and helps readers navigate a changing industry. "
Brent Fischthal - Koh YoungSuggested Items
How Good Design Enables Sustainable PCBs
08/21/2025 | Gerry Partida, Summit InterconnectSustainability has become a key focus for PCB companies seeking to reduce waste, conserve energy, and optimize resources. While many discussions on sustainability center around materials or energy-efficient processes, PCB design is an often overlooked factor that lies at the heart of manufacturing. Good design practices, especially those based on established IPC standards, play a central role in enabling sustainable PCB production. By ensuring designs are manufacturable and reliable, engineers can significantly reduce the environmental impact of their products.
50% Copper Tariffs, 100% Chip Uncertainty, and a Truce
08/19/2025 | Andy Shaughnessy, I-Connect007If you’re like me, tariffs were not on your radar screen until a few months ago, but now political rhetoric has turned to presidential action. Tariffs are front-page news with major developments coming directly from the Oval Office. These are not typical times. President Donald Trump campaigned on tariff reform, and he’s now busy revamping America’s tariff policy.
Global PCB Connections: Understanding the General Fabrication Process—A Designer’s Hidden Advantage
08/14/2025 | Markus Voeltz -- Column: Global PCB ConnectionsDesigners don’t need to become fabricators, but understanding the basics of PCB fabrication can save you time, money, and frustration. The more you understand what’s happening on the shop floor, the better you’ll be able to prevent downstream issues. As you move into more advanced designs like HDI, flex circuits, stacked vias, and embedded components, this foundational knowledge becomes even more critical. Remember: the fabricator is your partner.
MKS’ Atotech to Participate in IPCA Electronics Expo 2025
08/11/2025 | AtotechMKS Inc., a global provider of enabling technologies that transform our world, announced that its strategic brands ESI® (laser systems) and Atotech® (process chemicals, equipment, software, and services) will showcase their latest range of leading manufacturing solutions for printed circuit board (PCB) and package substrate manufacturing at the upcoming 17th IPCA Show to be held at Pragati Maidan, New Delhi from August 21-23, 2025.
MKS Showcases Next-generation PCB Manufacturing Solutions at the Thailand Electronics Circuit Asia 2025
08/06/2025 | MKS Instruments, Inc.MKS Inc, a global provider of enabling technologies that transform our world, today announced its participation in Thailand Electronics Circuit Asia 2025 (THECA 2025), taking place August 20–22 at BITEC in Bangkok.