-
- News
- Books
Featured Books
- smt007 Magazine
Latest Issues
Current IssueWhat's Your Sweet Spot?
Are you in a niche that’s growing or shrinking? Is it time to reassess and refocus? We spotlight companies thriving by redefining or reinforcing their niche. What are their insights?
Moving Forward With Confidence
In this issue, we focus on sales and quoting, workforce training, new IPC leadership in the U.S. and Canada, the effects of tariffs, CFX standards, and much more—all designed to provide perspective as you move through the cloud bank of today's shifting economic market.
Intelligent Test and Inspection
Are you ready to explore the cutting-edge advancements shaping the electronics manufacturing industry? The May 2025 issue of SMT007 Magazine is packed with insights, innovations, and expert perspectives that you won’t want to miss.
- Articles
- Columns
- Links
- Media kit
||| MENU - smt007 Magazine
Via-in-Pad Plated over Design Considerations to Mitigate Solder Separation Failure
November 29, 2017 | S.Y. Teng, P. Peretta and P. Ton, Cisco Systems Inc.; and V. Kome-ong and W. Kamanee, Celestica ThailandEstimated reading time: 6 minutes
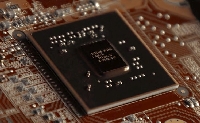
As signal speeds and performance requirements continue to rise, the use of advanced PCB technologies is becoming increasingly important. As a result, the via-in-pad plated over (VIPPO) structure has been adopted in many BGA footprint designs within the PCB. These VIPPO structures are preferred over the more traditional dog-bone pad structure in order to shrink signal path lengths, reducing two parasitic effects, capacitance and inductance, for improved highspeed performance.
Figure 1 illustrates how the VIPPO structure can influence those parasitic effects. The signal traces, which connect the BGA pads with the vias, act as inductors. Additionally, as high-speed designs typically have ground planes immediately below the outer layer, there is also a capacitive effect that is generated. With the VIPPO structure, the outer trace layer is eliminated, thereby cancelling both parasitic effects.
Figure 1: Dog-bone vs. VIPPO pad structure.
Figure 2 exhibits the VIPPO structure as compared with the VIPPO + backdrill (BD) structure. The use of backdrill with the VIPPO structure can eliminate the reflections within the unused portion of the via, which acts as a stub. The portion of the via indicated by the purple arrow is not in series with the signal path, but instead acts as a stub. Therefore, a portion of the signal is reflected back, creating an interference, which will degrade the high-speed signal performance. Hence, the purpose of the back-drill is to remove this “unused” portion of the via in order to eliminate the reflections for a cleaner signal.
Figure 2: VIPPO vs. VIPPO + backdrill structure.
With increased complexity of PCB designs for high-end networking products, the boards thicknesses are typically >120 mils and signal speeds are reaching 25 GHz and beyond. For these types of designs, backdrilling of the VIPPO structures becomes imperative.
It is also a common practice to mix VIPPO and non-VIPPO pad structures within a single BGA footprint, as indicated in Figure 3. The green lines indicate a high-speed signal trace (e.g., for differential pairs) on the outer layer. It is preferable from a signal integrity perspective, to route these signal lines on the outer layers of the PCB to take advantage of microstrip routing which has faster propagation speeds than stripline routing. Hence, these BGA pads do not require the use of VIPPO. These non-VIPPO pads are highlighted in red. Without any VIPPO structure, a zero stub length can be achieved, which is an extremely attractive option for the signal integrity engineer. Moreover, additional routing space is gained underneath the non-VIPPO pad. Unfortunately, these types of mixed footprint designs have a propensity for manufacturing defects during SMT assembly of BGA packages and can potentially expose the PCBA to field reliability risks if these defects escape manufacturing tests.
Figure 3: Mixed VIPPO/Non-VIPPO BGA Footprint.
Failure Mode and History
As a consequence of these advanced PCB technologies and complex board designs, a unique BGA solder joint failure mode has emerged during specific assembly conditions. This failure mode occurs when the bulk solder separates from the IMC during or just prior to reflow. This failure mode is of particular concern because the discontinuity is so small relative to the size of the solder joint itself that it cannot be detected via X-ray inspection methodologies. Furthermore, in many cases it is only a partial separation of the BGA solder joint and hence, it may not even be detected via ICT or functional test techniques. Without a robust methodology to screen for these defects, this presents an extremely high risk for potential escapes to the field.
Typically, this failure mode has been found on BGA packages with a 1 mm pitch or less BGA array and having a PCB footprint that includes a mixed VIPPO/non-VIPPO pad design. The solder separation occurs when the component is subjected to a secondary reflow, either during top-side SMT for bottom-side components or during rework of an adjacent, or mirrored, BGA component. Since the open occurs between the bulk solder and the IMC, it does not have the typical brittle solder joint fracture signature, which has a flat fracture interface through the IMC as shown in Figure 4. Instead, this failure mode exhibits more of a hot solder tear or separation type of failure mode, as the solder separates from the IMC leaving it intact.
Figure 4: Example of brittle fracture.
Figures 5 and 6 illustrate examples of both partial and complete solder separations. For these failures, the solder separation only occurs on the solder joints that use a VIPPO BGA pad and is typically adjacent to a solder joint(s) with a non-VIPPO BGA pad. In some cases, this type of failure mode has also been identified on a component having a full VIPPO BGA pad pattern on the PCB when there is also a pattern of VIPPO with deep backdrill (BD) within the footprint. Hence, the deep-backdrill VIPPO structures seem to mimic the behavior of the non-VIPPO pads so that it becomes comparable to a mixed VIPPO/non-VIPPO BGA pad footprint and again, induces solder separation in the solder joints on a VIPPO pad when subjected to a secondary reflow.
Page 1 of 2
Suggested Items
Driving Innovation: Direct Imaging vs. Conventional Exposure
07/01/2025 | Simon Khesin -- Column: Driving InnovationMy first camera used Kodak film. I even experimented with developing photos in the bathroom, though I usually dropped the film off at a Kodak center and received the prints two weeks later, only to discover that some images were out of focus or poorly framed. Today, every smartphone contains a high-quality camera capable of producing stunning images instantly.
Hands-On Demos Now Available for Apollo Seiko’s EF and AF Selective Soldering Lines
06/30/2025 | Apollo SeikoApollo Seiko, a leading innovator in soldering technology, is excited to spotlight its expanded lineup of EF and AF Series Selective Soldering Systems, now available for live demonstrations in its newly dedicated demo room.
Indium Corporation Expert to Present on Automotive and Industrial Solder Bonding Solutions at Global Electronics Association Workshop
06/26/2025 | IndiumIndium Corporation Principal Engineer, Advanced Materials, Andy Mackie, Ph.D., MSc, will deliver a technical presentation on innovative solder bonding solutions for automotive and industrial applications at the Global Electronics A
Fresh PCB Concepts: Assembly Challenges with Micro Components and Standard Solder Mask Practices
06/26/2025 | Team NCAB -- Column: Fresh PCB ConceptsMicro components have redefined what is possible in PCB design. With package sizes like 01005 and 0201 becoming more common in high-density layouts, designers are now expected to pack more performance into smaller spaces than ever before. While these advancements support miniaturization and functionality, they introduce new assembly challenges, particularly with traditional solder mask and legend application processes.
Knocking Down the Bone Pile: Tin Whisker Mitigation in Aerospace Applications, Part 3
06/25/2025 | Nash Bell -- Column: Knocking Down the Bone PileTin whiskers are slender, hair-like metallic growths that can develop on the surface of tin-plated electronic components. Typically measuring a few micrometers in diameter and growing several millimeters in length, they form through an electrochemical process influenced by environmental factors such as temperature variations, mechanical or compressive stress, and the aging of solder alloys.