-
- News
- Books
Featured Books
- smt007 Magazine
Latest Issues
Current IssueSupply Chain Strategies
A successful brand is built on strong customer relationships—anchored by a well-orchestrated supply chain at its core. This month, we look at how managing your supply chain directly influences customer perception.
What's Your Sweet Spot?
Are you in a niche that’s growing or shrinking? Is it time to reassess and refocus? We spotlight companies thriving by redefining or reinforcing their niche. What are their insights?
Moving Forward With Confidence
In this issue, we focus on sales and quoting, workforce training, new IPC leadership in the U.S. and Canada, the effects of tariffs, CFX standards, and much more—all designed to provide perspective as you move through the cloud bank of today's shifting economic market.
- Articles
- Columns
- Links
- Media kit
||| MENU - smt007 Magazine
What Matters Most is Communication
December 4, 2017 | Stephen Las Marias, I-Connect007Estimated reading time: 3 minutes
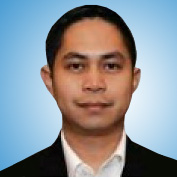
There is a growing trend towards the use of HDI in electronics manufacturing. A simple reason is that people want greater performance from their electronics, now more than ever. From an electronics design standpoint, greater performance means more switches or transistors. More transistors mean more power. Counterintuitively, more power requirements of a device means you need to lower the power of the whole system or subassembly. You also need to lower the power because then, you need to deal with thermal management.
To lower the power requirement, everything must be reduced. As such, the components keep getting smaller and smaller. Pin pitches are now down to 0.25 mm or around 10 mil. On top of that, the overall density of board assemblies continuously increases in line with the growing demand for more features and functions. Adding to that challenge is the shrinking PCB real estate on which to put this increasing number of components.
Our recent survey on HDI found that the three key factors driving HDI work are: overall density, fine pitch of components, and the high pin counts of ICs (Chart 1).
At present, majority of our surveyed respondents say up to 25% of PCBs they work with use HDI technology (Chart 2).
In three years, nearly half of the respondents answered that HDI technology will account for at least 50% of their PCB work. This is across a variety of industries, top three of which are consumer electronics, telecommunications, and automotive electronics. In particular, the emergence of 5G and Internet of Things (IoT) are expected to bolster the use of HDI technology due to frequency and signaling requirements (Chart 3).
Assemblers have different areas of concern regarding HDI than fabricators and designers. When it comes down to having vias in the boards, especially vias in pads, issues will arise if the assembly is the not done properly. "When you put a via in a pad, you typically want to fill that via, with either a non-conductive or conductive epoxy, and use some sort of plating over the barrel of the via so that you get a smooth pad that you are assembling the part to without a whole lot of surface deviation. The flatter the pad, the easier it is to print solder on the board, and to assemble the part," said Garret Maxson of EMS firm ACDi.
This month’s issue of SMT Magazine examines the challenges when dealing with HDI from an assembly perspective. We start with a roundtable between HDI experts Steve Bird of Finisar, Tony Torres of APCT, and technologists from EMS firm MC Assembly, including Vince Burns, Steve Jervey, Mike Smyth, and Paul Petty. The discussion covers the latest technology developments, manufacturing challenges, and HDI strategies, from the design, fabrication, and assembly perspectives. What we found out is that, while there may be new techniques and strategies, technologies, equipment, tools, and materials to employ and utilize, there is always one thing that will ensure the manufacturing/ assembly success of your product: communication.
Communication between the designer and the assembler will help improve the manufacturability and assembly of the final product—even before the board design gets fabricated. As Vince Burns of MC Assembly says, "It's not just designing the perfect circuit, but it has to be manufacturable, and that’s where our input comes in."
There is value to be added in collaborating with the designers in the very first stages of the design. Indeed, the goal is working together as a team and sharing the expertise of one another to make sure that the design is manufacturable, and the final product is of high quality and reliable.
To read the full version of this article, which appeared in the November 2017 issue of SMT Magazine, click here.
Testimonial
"Our marketing partnership with I-Connect007 is already delivering. Just a day after our press release went live, we received a direct inquiry about our updated products!"
Rachael Temple - AlltematedSuggested Items
Indium Corporation Promotes Two Leaders in EMEA (Europe, Middle East, and Africa) Markets
08/05/2025 | Indium CorporationWith its commitment to innovation and growth through employee development, Indium Corporation today announced the promotions of Andy Seager to Associate Director, Continental Sales (EMEA), and Karthik Vijay to Senior Technical Manager (EMEA). These advancements reflect their contributions to the company’s continued innovative efforts with customers across Europe, the Middle East, and Africa (EMEA).
MacDermid Alpha Electronics Solutions Unveils Unified Global Website to Deepen Customer, Talent, and Stakeholder Engagement
07/31/2025 | MacDermid Alpha Electronics SolutionsMacDermid Alpha Electronics Solutions, the electronics business of Elements Solutions Inc, today launched macdermidalpha.com - a unified global website built to deepen digital engagement. The launch marks a significant milestone in the business’ ongoing commitment to delivering more meaningful, interactive, and impactful experiences for its customers, talent, and stakeholders worldwide.
KOKI to Showcase Analytical Services and New HF1200 Solder Paste at SMTA Guadalajara 2025
07/31/2025 | KOKIKOKI, a global leader in advanced soldering materials and process optimization services, will exhibit at the SMTA Guadalajara Expo & Tech Forum, taking place September 17 & 18, 2025 at Expo Guadalajara, Salón Jalisco Halls D & E in Guadalajara, Mexico.
Weller Tools Supports Future Talent with Exclusive Donation to SMTA Michigan Student Soldering Competition
07/23/2025 | Weller ToolsWeller Tools, the industry leader in hand soldering solutions, is proud to announce its support of the upcoming SMTA Michigan Expo & Tech Forum by donating a limited-edition 80th Anniversary Black Soldering Set to the event’s student soldering competition.
Koh Young Appoints Tom Hattori as President of Koh Young Japan
07/21/2025 | Koh YoungKoh Young Technology, the global leader in True 3D measurement-based inspection solutions, announced the appointment of Tom Hattori as President of Koh Young Japan (JKY).