-
- News
- Books
Featured Books
- smt007 Magazine
Latest Issues
Current IssueWhat's Your Sweet Spot?
Are you in a niche that’s growing or shrinking? Is it time to reassess and refocus? We spotlight companies thriving by redefining or reinforcing their niche. What are their insights?
Moving Forward With Confidence
In this issue, we focus on sales and quoting, workforce training, new IPC leadership in the U.S. and Canada, the effects of tariffs, CFX standards, and much more—all designed to provide perspective as you move through the cloud bank of today's shifting economic market.
Intelligent Test and Inspection
Are you ready to explore the cutting-edge advancements shaping the electronics manufacturing industry? The May 2025 issue of SMT007 Magazine is packed with insights, innovations, and expert perspectives that you won’t want to miss.
- Articles
- Columns
- Links
- Media kit
||| MENU - smt007 Magazine
Mirtec Succeeding Through Inspection Innovation
December 20, 2017 | Pete Starkey, I-Connect007Estimated reading time: 13 minutes
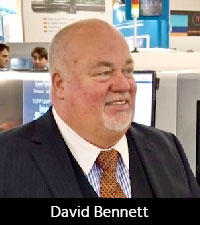
During productronica, I had the good fortune to sit down for an interview with David Bennett, president of Mirtec Europe. We discussed a variety of topics, including Mirtec’s latest inspection technologies, the challenges that miniaturization can bring, and Mirtec’s efforts to stay on the leading edge and never be a “me too” company.
Pete Starkey: I'm here at productronica speaking with David Bennett of Mirtec. David, thank you for sparing us your time. We recognize how busy you are, and certainly there's an awful lot of activity around your booth.
Give us an idea, as a leading supplier of automated optical inspection equipment, what's driving your developments? What's driving the technology? What's the market expecting of you?
David Bennett: The key things in inspection are the fact that nothing's getting easier. Everything's getting harder. Miniaturization, things like system in package, all these sorts of things. It's an industry that's always being driven forward. And the reason why Mirtec is so successful ... I mean, there are bigger companies than Mirtec. But I always say, "Fiat is bigger than Jaguar. I know what I prefer to drive." So the fact of the matter is, we're the technology leader, and that is supported by over 38 industry technology awards, which is unrivaled by anybody in inspection. And it's always for things like the sensors. We are passionate about owning everything to do with our technology.
For example, we were the first and still are the major camera supplier in optical inspection. The vast, vast majority, if not everybody else in the industry, tends to buy off a vendor.
Starkey: I think we recognize that. Everything under the hood.
Bennett: Exactly. The issue you have there is you're only ever as good as your vendor's technology, and your vendor might be looking at totally different industries. So we are focused on semiconductor, LED manufacturing, and SMT. So we develop optics, lenses, to deal with the problems and the future of those industries. So I don't care about the food industry. I don't care what's needed in another industry. I need to look after my customers. And the way Mirtec do that is taking absolute control of all of our sensors. Our 3D sensors, our cameras, even down to the lenses, everything is done by Mirtec.
Starkey: Again, it makes a lot of sense when you've got that sort of level of control and no dependency on any third-party supplier. So, what are the main inspection challenges that you're having to address at the moment?
Bennett: The complexity of boards is becoming a challenge. Everything's being miniaturized, everything's being densely populated. We're working on some projects, unfortunately, they're NDA covered, but we've actually been headhunted by specialist companies in this industry who want us to work with them, because they are having a problem to do certain types of inspection. And their attitude is, "If Mirtec cannot do it, it cannot be done." That's a massive compliment to us.
But they're actually correct. Even down to the issue of repeatability, if you're measuring, metrology's becoming very important now. It's always been there, but now it's even more important in inspection. If you cannot get back to the same position, and you're trying to measure something like an 0201 metric pad, then you have an in-build problem. We have a repeatability of 1 micron, which no one in this industry has, except us.
Again, it's one of those situations where we don't want to be a "me too.” We don't want to have a similar technology to our competitors. We want to continue to push the boundaries, and you can only do that if you own your own destiny, and the destiny of the sensors in Mirtec are 100% controlled by us.
Starkey: Do you find that whatever trend you set becomes the trend everybody tries to emulate, by which time you've already moved on?
Bennett: Oh yeah. We were the very first company to bring out a 10 megapixel camera. Then we had a 15 megapixel, then we had a 25. Then we had a 50. Mirtec are moving forward all the time on that. Now the guys who were competitors, who had 2 megapixel and 4 megapixel, they're all trying to catch up. But they could only have what their vendors supplied them. So they're always lagging, and we're laps ahead on that sort of thing.
People think that the cameras, because they have a bigger field of view, just give you speed. Well, of course, they do. But what we do, we start with a big field of view, and then we use a very small lens. So you get incredible accuracy and high definition of what you're looking at.
Being able to go fast and keep up with a production line, whilst looking with the most detailed lenses into miniaturization, is a defining factor of the strength of Mirtec. Other companies, if they cannot control their lenses, and they cannot control their cameras, have in pretty much a fixed state and the only way that they can go faster is to open up the field of view, which is like pulling away from what you're trying to inspect in the first place. We go exactly the opposite. We start with a huge field of view, and crunch it down to get great detail. That gives us the speed we require for our customers, and the detail.
Starkey: Is there any opportunity to do that sort of thing in combination? To look at a larger field and if there is some feature within that field that requires more critical inspection, to focus in on that?
Bennett: Well, we can cover all of the component sizes, because our field of view is so big. We can see even the big components quite easily. At the same time, we can see the pad, and measure, not just see it. We can measure the pad of an 0201 metric, which is the smallest component currently in production.
Starkey: Yet.
Bennett: Yet. But the fact is, we can see it clearly. So, at the moment, our lens capabilities go from a 4 micron, 6 micron, to a 9.8 micron, 13 micron, and up to 15 micron. The customer's requirement will determine what lens and what camera he puts together. Wherever possible, we say to our customers, "If we're within your beat speed, keep the smallest lens you can." That's just like looking closer than anybody else is looking. And when you come to be able to look closer, your data, if you have the repeatability, the accuracy to look in the same place, and measure accurately, then the data, the information that your customers are working with, is solid. They don't have to worry about shift, or trying to get the best they can do. You've got to be able to do the absolute, and that's what we aim for.
Starkey: You're producing a lot of data.
Bennett: Yes.
Starkey: Where does that data go? What can you do with that data? What do you do with that data?
Bennett: We've actually just signed a deal to work with Cogiscan for Industry 4.0. Now, we've been exporting data for many years into MES systems, and into companies' local databases, and whatever. They can choose from our SPC packages, etc., exactly what they want, when they want it, where they want it. So having data around has been great. But now, because the Industry 4.0 drive to have all of the machines as a complete, total line, everyone's trying to reinvent the wheel, or make relationships where this printer works with this SPI, and that pick-and-place, and whatever. "Here, Mr. Customer, here's a solution."
I've been involved in data transfer for over 20 years in this industry, and I can tell you, customers don't want to buy what vendors want to sell them. They want to buy what they want to buy, and usually it's best in class. So going to them with a complete line solution and saying, "No, look, we've shaken hands, and we can all speak, but I don't like that oven. I don't want that printer. I don't want that AOI."
So what we did is we went to Cogiscan, and they are one of the world's leading connection companies for machine connectability, and said, "Make a black box translator where you can plug a Mirtec into any competitor's machine, any other piece of equipment on the production line." It's seamless. It's been handled by specialists in data transfer. Why should we try to invent the wheel? These guys exist, and they already have the communication protocols to speak to virtually everybody at the same time.
Page 1 of 2
Suggested Items
Smarter Machines Use AOI to Transform PCB Inspections
06/30/2025 | Marcy LaRont, PCB007 MagazineAs automated optical inspection (AOI) evolves from traditional end-of-process inspections to proactive, in-line solutions, the integration of AI and machine learning is revolutionizing defect reduction and enhancing yields, marking a pivotal shift in how quality is managed in manufacturing.
SolderKing’s Successful Approach to Modern Soldering Needs
06/18/2025 | Nolan Johnson, I-Connect007Chris Ward, co-founder of the family-owned SolderKing, discusses his company's rapid growth and recent recognition with the King’s Award for Enterprise. Chris shares how SolderKing has achieved these award-winning levels of service in such a short timeframe. Their secret? Being flexible in a changing market, technical prowess, and strong customer support.
ZETWERK Enhances Manufacturing Capabilities with TRI
06/04/2025 | TRITest Research, Inc. (TRI), the leading test and inspection systems provider for the electronics manufacturing industry, is pleased to announce that ZETWERK Electronics has integrated TRI's Automated Optical Inspection (AOI) and Solder Paste Inspection (SPI) solutions into its state-of-the-art manufacturing facility in Tamil Nadu.
Axxon-Mycronic Enhances Conformal Coating Quality with New Inline AOI and Thickness Measurement Technology
06/03/2025 | Axxon-MycronicAxxon-Mycronic, a leading, global supplier of innovative and production-ready, dispensing and conformal coating systems, announced a breakthrough in automated optical inspection (AOI) technology for conformal coating with the introduction of its Modus inline conformal coating AOI system—CCAOI.
I-Connect007 Editor’s Choice: Five Must-Reads for the Week
05/30/2025 | Andy Shaughnessy, Design007I don’t have a scorecard, but I do have a weekly wrap-up of must-reads that I think deserve another “bite of the apple,” so to speak. IPC’s Rich Cappetto shares his perspective on everything from tariffs to the CHIPS Act. Columnist Josh Casper discusses the use of AI in 3D AOI systems and the immediate benefits that AI can bring about. Columnist Anaya Vardya explains how technologies like AI can improve our customer service, as well as our manufacturing processes.