-
- News
- Books
Featured Books
- design007 Magazine
Latest Issues
Current IssueShowing Some Constraint
A strong design constraint strategy carefully balances a wide range of electrical and manufacturing trade-offs. This month, we explore the key requirements, common challenges, and best practices behind building an effective constraint strategy.
All About That Route
Most designers favor manual routing, but today's interactive autorouters may be changing designers' minds by allowing users more direct control. In this issue, our expert contributors discuss a variety of manual and autorouting strategies.
Creating the Ideal Data Package
Why is it so difficult to create the ideal data package? Many of these simple errors can be alleviated by paying attention to detail—and knowing what issues to look out for. So, this month, our experts weigh in on the best practices for creating the ideal design data package for your design.
- Articles
- Columns
- Links
- Media kit
||| MENU - design007 Magazine
Selecting X-Ray Inspection Equipment
January 24, 2018 | Russell Poppe, JJS ManufacturingEstimated reading time: 6 minutes
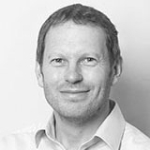
There is a continuing trend towards smaller, more densely-populated printed circuit board (PCB) assemblies in electronics manufacturing. This is not necessarily because the PCB assembly needs to be smaller, but new designs are using significantly more ball grid array (BGA) and other types of devices with hidden solder connections, such as quad flat no-leads (QFN) and land grid arrays (LGAs). Such devices often have performance and cost advantages over larger packages with leads, so the trend is likely to continue.
Automated optical inspection (AOI) is an established, key process control in the SMT industry that greatly increases confidence in the quality of the finished product. But what do you do about devices where you cannot optically see the solder connections? X-ray inspection provides the answer.
Using X-ray as an in-process control can help remove the risk of producing assemblies that are impossible or uneconomical to repair due to misplaced ‘hidden connection’ devices. Reworking a misplaced device can be time consuming and may cause other issues on the assembly, for example with surrounding components on the PCB due to local heating. Rework might also exceed the maximum number of solder reflow cycles allowed for double-sided assemblies. Finding a failure later in the process, for example at JTAG or functional test, incurs additional lost time and cost in diagnosis and re-test.
So, when should you use X-ray? It should certainly be part of the ‘first-off’ inspection process, helping to ensure the oven profile is optimal for the leadless devices. It might then be sensible to check a sample of assemblies as they go through production; a few from the start, middle and end of the batch is typical. Alternatively, an ‘in line’ process might be used, though it is worth noting that X-ray inspection—even if automated—is relatively slow. In practice, placing leadless devices, especially BGAs, is quite straightforward and normally causes few issues, so X-ray should be employed thoughtfully.
Figure 1: X-ray allows inspection without resorting to potentially destructive re-work or micro-sectioning.
X-ray inspection can also help reduce end-of-line manual inspection, for example on fine-pitch devices that cannot be fully covered by AOI (depending on what type of system you have), or where other BGA inspection methods such as an Ersascope might have been used. Another great benefit of X-ray inspection is in resolving quality issues. X-ray allows inspection without resorting to potentially destructive re-work or micro sectioning, which adds cost and, of course, leads to a scrapped assembly. Micro-sectioning also requires a bit of an educated guess as to where the problem might be.
How often have your heard someone say, “It fails test, it doesn’t work, and I can’t see where the problem is, so it must be the BGA”? Enhancing X-ray to provide laminography, or indeed, full 3D capability that enables the inspector to walk through an assembly, helps find faults such as broken tracks or barrels in a PCB, for example, as well as any issues with leadless components.
Away from PCBAs, X-ray can provide nondestructive inspection of other manufactured components such as cable assemblies or machined parts where there is a need to see interior detail. It can also provide a degree of measurement capability.
So, a capable X-ray inspection facility is now considered a must-have for modern electronics assembly lines. But now that you have decided you need one yourself, or that your electronics manufacturing services (EMS) partner should be investing on your behalf, how do you go about choosing the right system?
Key Considerations
There are a lot of vendors and systems out there, so as with all capital equipment evaluations it is best to start looking with a must-have list already in mind. We will assume that price (and payback) will be part of the equation, and of course, the system must be large enough to accommodate the items that you want to inspect.
The following are four more areas to consider:
1. Image quality
If you were looking to buy a camera, then one with a higher pixel count, say, 24MP, is better quality than one with 16MP, right? If you know a bit about photography, you will know this is a great over-simplification (if not just plain nonsense), and if anything, X-ray can seem even more complicated.
There are physics and very clever software involved. Things that can affect image quality include the power, voltage, spot size, detector resolution, proximity of the X-ray source to the item and the field of view. Take voltage, for example. A 160kV system will have greater X-ray penetration capability than say a 130kV system, but the higher voltage can adversely affect the image contrast and hence, quality. How do you decide? The most practical solution is to take some typical sample assemblies and try the X-ray system out. Image quality can be a subjective opinion.
The great news is that you will probably find that systems aimed at PCB assemblies provide image quality that ranges from very good to excellent. This can perhaps be more to do with how the inspection is set up than the technical capability of its components.
Page 1 of 2
Testimonial
"The I-Connect007 team is outstanding—kind, responsive, and a true marketing partner. Their design team created fresh, eye-catching ads, and their editorial support polished our content to let our brand shine. Thank you all! "
Sweeney Ng - CEE PCBSuggested Items
MacDermid Alpha Electronics Solutions Unveils Unified Global Website to Deepen Customer, Talent, and Stakeholder Engagement
07/31/2025 | MacDermid Alpha Electronics SolutionsMacDermid Alpha Electronics Solutions, the electronics business of Elements Solutions Inc, today launched macdermidalpha.com - a unified global website built to deepen digital engagement. The launch marks a significant milestone in the business’ ongoing commitment to delivering more meaningful, interactive, and impactful experiences for its customers, talent, and stakeholders worldwide.
KOKI to Showcase Analytical Services and New HF1200 Solder Paste at SMTA Guadalajara 2025
07/31/2025 | KOKIKOKI, a global leader in advanced soldering materials and process optimization services, will exhibit at the SMTA Guadalajara Expo & Tech Forum, taking place September 17 & 18, 2025 at Expo Guadalajara, Salón Jalisco Halls D & E in Guadalajara, Mexico.
Weller Tools Supports Future Talent with Exclusive Donation to SMTA Michigan Student Soldering Competition
07/23/2025 | Weller ToolsWeller Tools, the industry leader in hand soldering solutions, is proud to announce its support of the upcoming SMTA Michigan Expo & Tech Forum by donating a limited-edition 80th Anniversary Black Soldering Set to the event’s student soldering competition.
Koh Young Appoints Tom Hattori as President of Koh Young Japan
07/21/2025 | Koh YoungKoh Young Technology, the global leader in True 3D measurement-based inspection solutions, announced the appointment of Tom Hattori as President of Koh Young Japan (JKY).
Silicon Mountain Contract Services Enhances SMT Capabilities with New HELLER Reflow Oven
07/17/2025 | Silicon Mountain Contract ServicesSilicon Mountain Contract Services, a leading provider of custom electronics manufacturing solutions, is proud to announce a significant upgrade to its SMT production capability with the addition of a HELLER 2043 MK5 10‑zone reflow oven to its Nampa facility.