Super Dry’s Novel Approach to the Drying Process
February 7, 2018 | Pete Starkey, I-Connect007Estimated reading time: 12 minutes
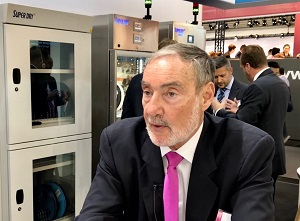
Pete Starkey spent a few minutes at the Super Dry booth on the first day of the productroncica show, and chatted with old friend Rich Heimsch, who taught the old dog a few new tricks about the drying process.
Pete Starkey: Rich, it's great to see you here. Thank you for joining us.
Rich Heimsch: Very nice to see you again. It's good to do some work and catch up with old friends, which is what this show certainly offers to me. And it's significant also because of the difference between the U.S. and European markets in their attitude to moisture management.
Starkey: Rich, would you expand on those cultural differences?
Heimsch: The European market is simply more mature. It's considerably more advanced because they needed to worry about it much sooner.
Starkey: Would this relate back to 2006 and the introduction of RoHS regulations and lead free?
Heimsch: Yes. Overnight, virtually every component in a guy's shop needed to be watched, and a lead-free process adds one or often two MSL levels to every component. So, you could say it took them by surprise. They knew the legislation had a date, but there were a lot of other things to worry about first. “I need paste. I need re-flow.” That was a pressure thing. There was a bit of a surprise and that required some scrambling. And the founder of our company will say that it was that point in time that the business completely shifted gears. It was also a point in time where assemblers started to recognize that they needed to do things a different way. They needed to deal with the logistics of baking everything and then, “What am I going to do with it? Because the clock is restarting. Let's build something where I can store and reset the floor life in the same place.” That was the genesis of our ‘floor-life reset’ cabinets which have moved along significantly in capability over the years. I can recall bringing one to an APEX show, let's say eight years ago, and most of the people who came by said, "Really, what does it do and what would I need that for?"
Starkey: Could you just define your meaning of floor-life reset?
Heimsch: Restoring the safety of a component after it has expired, after it's been out in ambient atmosphere for too long. Exactly what traditional high-temperature baking was set to perform. Europeans then recognized that this baking induces oxidation and intermetallics and now felt it was time to deal with the solderability. They were baking more and more, a larger percentage of components, and creating more solderability related issues than they had before. Just by the numbers.
The low temperatures do not induce that oxidation. They greatly less induce intermetallic growth, and at the very low humidities, which just didn't exist when the 033 standard was written, accelerate the drying to where a 1% 60°C dry is faster than 90°C at atmosphere or even 90°C in a nitrogen oven. So, they kept going on from there. One of the things that we're doing now is offering in the machine the tracking of up to 20 different batches of parts and floor life being recovered with software to track them. Software to automatically calculate how much time it needs. If it's MSL3 and it's 1.4 millimeters in thickness and I'm at 1% at 40°C or 1% at 60°C, it will do the calculation for you. Hit start and it'll keep track of it and let you know when the different ones are finished. You can go in and out with more batches, with other batches, and that's where the recovery time that we talked about has played another role. Interestingly enough, the understanding and the take up of that low temperature baking is the most noticeable change in our U.S. domestic market as far as people who are doing it. I mean, still a lot of people feel they don't need to. Automotive, military, they have always known. We've had this conversation once before. You get an intermittent in your handset, it's an inconvenience. To have an intermittent in your airbag, your ABS, or your implant and it's another level of problem. So, I can't say across the board that the North American market is seven years behind, but in a generalized way, that's the case. These guys had to start somewhat sooner.
Starkey: Rich, can I ask just to explain in basic terms how the low-temperature desiccation, low-temperature moisture removal system works?
Heimsch: We create an atmosphere with virtually no moisture in it whatsoever, like 0.05 grams of water per cubic meter. That alone is a moisture vacuum. That will at ambient temperature dry out a saturated component. As a matter of fact, faster than the 40C @ 5% process in the 033C spec that many people use. But it’s of course desirable to dry faster. So, every 10°C of heat that you add to that, the time cuts in half. The heat accelerates that drying process. However, we remain at a low temperature. We haven't induced the corrosion that the higher temperatures cause in these alloys. And it becomes a balance and a compromise between how much time do I want to spend on this and how much do I want to protect the solderability? The real kind of eureka moment is recognizing you can do it several times and in a super high-mix, low-volume environment, in and out, back and forth, back and forth off the line. That can be a significant benefit.
Starkey: Which you can't do with repeated high-temperature baking.
Heimsch: Correct.
Starkey: Because you just thermally degrade the components, you're encouraging intermetallic growth, and you're changing the solderability characteristics.
Heimsch: Even going back 25 years when the 033 standard was first formed, it talks about limiting the high-temperature baking. It is certainly known. To me, it's a recognizable indicator of a change within our domestic U.S. market. Obviously, more and more people are committing to, “Okay, now's the time I get a moisture management process in place.” Lead free, over time, has become a larger and larger percentage of the solder paste that's consumed in the U.S. So then over time they face the same issues and how much better it is to comprehensively manage components.
Because most components do not have unlimited floor life. You can't just leave them lying around. You must have some sort of process control, and that's generating new interest in how this works and what exactly are we talking about. For a manufacturing manager, it might not change his end of line yield significantly. A lot of these assemblies with damaged components pass in-circuit test, pass the functional test and it's out in the field three, four, five months before the failures occur. A lot of the micro cracking will occur on the underside of devices because that's where the encapsulation is the thinnest. It's the water vapor trying to get out and exceed the elastic limit of the encapsulant, and that's the easiest place to escape. You're not going to visibly see that. So, the recognition that it needs to be managed and the baking process refined continues to evolve.
Starkey: The fact that you can effectively build up a database of the drying program you need versus the nature and dimensions of the components that you're storing.
Heimsch: Yes. And the original baking guidelines differentiate between component thicknesses, and the thicker components have a longer floor life because they take longer to reach a dangerous water weight percentage.
Starkey: On the other hand, once they've reached that point, they take longer to pull back.
Heimsch: That's exactly right. Doing the exact same saturating, drying, weighing procedures that were done 25 years ago at 125°C. Components were saturated according to IPC JEDEC specs then put into a 1%, 40°C atmosphere, a 1% 60°C atmosphere, weighed hourly as they dried, and now you had lines to follow for the adsorption rate of the drying.
Page 1 of 2
Suggested Items
ViTrox Marks 25 Years of Innovation with Cutting-Edge Solutions at NEPCON China 2025 in Shanghai
04/18/2025 | ViTrox TechnologiesViTrox, which aims to be the World’s Most Trusted Technology Company, is proud to announce its participation in NEPCON China 2025, taking place from April 22–24, 2025, at Booth #1E45, Shanghai World Expo Exhibition & Convention Centre (SWEECC).
Indium Experts to Present on Power Electronics at PCIM Europe 2025
04/17/2025 | Indium CorporationAs one of the leading materials providers to the power electronics assembly and e-Mobility industries, Indium Corporation experts will share their technical insight and knowledge on a variety of industry-related topics throughout PCIM Europe, May 6-8, in Nuremberg, Germany.
KOKI Announces Upcoming Webinar on Solder Voiding – Causes and Remedies
04/16/2025 | KOKIKOKI, a global leader in advanced soldering materials and process optimization services, is pleased to announce its upcoming webinar, “Solder Voiding—Causes and Remedies,” which will take place on Tuesday, April 22, 2025, at 12:00 PM CDT. Jerome McIntyre, Regional Sales & Applications Engineer at KOKI Americas, will present this live session.
Real Time with... IPC APEX EXPO 2025: Transition Automation Focusing on Security Coatings and Squeegee Technology
04/16/2025 | Real Time with...IPC APEX EXPOMark Curtin, President of Transition Automation, gives an update on recent innovations at his company. He highlights a record sales month and their new focus on security coatings to fight counterfeiting. Mark explains the engineering behind their durable squeegees, the importance of maintenance, and the value of considering overall costs over just price.
Indium to Feature Materials Solutions Powering Sustainability at PCIM Europe
04/15/2025 | Indium CorporationIndium Corporation specializes in power device packaging, offering a portfolio of advanced material solutions encompassing the entire assembly, including die-attach, top-side die interconnect, substrate-attach, package-attach, and PCB assembly.