Pros and Cons of Outsourcing Your Product Design to an Independent Contractor
February 8, 2018 | Neil Sharp, JJS ManufacturingEstimated reading time: 4 minutes
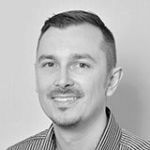
For OEMs looking to improve a product's viability through its life-cycle, the decision to outsource product design to an independent contractor can offer many advantages.
Taking on an independent design contractor or sole trader offers an opportunity to inject a fresh perspective, to gain the value of specialist knowledge and to save on staffing costs, training, infrastructure and equipment.
Opting to outsource your product design process can also free your business to focus on the other things that you're great at, whether that's developing new product concepts, exploring price points or securing new sales.
Ultimately though, deciding whether to engage an independent contractor in your product design will require weighing up the pros and cons as they apply to your specific project.
The Pros of an Independent Contractor
- Efficiency—Choosing to maintain your own in-house team of designers relies on a steady stream of projects to keep your staff occupied - and a payroll to support that process. So if you're an OEM seeking a short-term product design solution, then employing an independent contractor for a fixed time-frame could be the answer. In appointing an independent contractor, you engage the specialist help that you need, when you need it, but without the associated overheads and administrative commitment of retaining a permanent employee.
- Specialist Knowledge—If you're a manufacturer of unique or niche products then the decision to outsource product design may offer the opportunity to hand-pick an independent contractor with the specific bespoke skills that are the best fit for your project. Bringing in that specialist knowledge can also to lead to increased efficiency as your contractor comes equipped with the relevant experience, and lessons learned, from previous design projects.
- Training—As an OEM it isn't always practical to have all the required skills, infrastructure, equipment and personnel for product design permanently in-house. And with the increasingly fast pace of technology, it may prove more time efficient, and cost effective, to hand over the technical challenges of your design to a contractor who can keep up with the rapid changes in software and hardware.
- Accountability—Working with an individual rather than a larger design team can ensure that the areas of individual responsibility are distinctly defined, and that there are clear lines of communication through each stage of the project. An independent contractor may also offer a higher degree of certainty as they are working to an agreed brief, with a set budget and a defined time-frame for completion.
- Strategy—If your in-house design team is already working to capacity then the decision to outsource to an independent contractor may enable you to meet a specific short-term goal or operational need. Or perhaps you're thinking further ahead and are looking to outsource product design as part of a longer-term strategy.
The Cons of an Independent Contractor
- Management—Choosing to take on an outside contractor may bring with it some new management challenges. You might want to consider whether your contractor will require micro-management and how much supervision, if any, they'll need through the project. If they're going to be based on-site then you'll want to ensure you have the facilities and infrastructure to support them. And if they'll be working remotely then you'll want to bear in mind how you intend to maintain communication and retain control of the project throughout the design process.
- Timing—Experienced designers with specific technical skills could well be in high demand, so once you've identified the independent contractor whom you hope to secure, the next step will be to make sure you can engage their services for the time-frame you need. It's also worth bearing in mind the time that the recruitment process, from identifying the appropriate candidate to securing an agreement, may take some time, so you'll want to factor this into your planning.
- Risk—Bringing in an external contractor, and particularly if they are an unknown, can carry with it an element of risk, so you'll want to do your due diligence to ensure their skills and experience fit your project brief. You'll also need to agree a clear 'statement of work' which details their responsibilities and which includes provisions for when things don't go to plan. Introducing a freelancer or independent designer may also have an impact, whether positively or negatively, on your existing staff, so it's worth considering how your company culture may be affected by the introduction of someone new into your current team.
Choosing to outsource your product design to an external contractor could well offer some clear advantages in terms of efficiency, cost-savings and specialist knowledge. On the flip side though there is the risk of not being able to secure the expertise you need when you need it and the challenge of retaining control through the design process.
Every design project is unique, so there is no right or wrong answer when it comes to outsourcing. But if there is one clear goal to keep front of mind, it is to make sure you keep your EMS provider in the loop throughout the process. Design and manufacture go hand in hand and your EMS provider will be an invaluable source of information and guidance as you weigh up your options.
This article originally appeared on the JJS Manufacturing blog, which can be found here.
Testimonial
"We’re proud to call I-Connect007 a trusted partner. Their innovative approach and industry insight made our podcast collaboration a success by connecting us with the right audience and delivering real results."
Julia McCaffrey - NCAB GroupSuggested Items
Electronic Components Market Update
10/04/2018 | Daniella Baldock, JJS ManufacturingUnfortunately, there is still no end in sight to the electronic component shortage, and some lead-times are being quoted with 2019 and even 2020 delivery dates! So if you are working with an EMS provider, it remains vital that you communicate and share forecast information with them. You may also want to start looking at the option of fitting, or designing in, smaller components to your PCB assemblies.
What SMT Component Shortages Mean for Design and Manufacturing Engineers
09/13/2018 | Russell Poppe, JJS ManufacturingMuch has been written about the increasing shortages of electronic components such as MLCCs, chip resistors and other semiconductor devices. And the manufacturing industry is now seeing price increases and greatly extended lead times. It seems the situation is likely to get rapidly worse rather than better. What can we do? Read on.
5 Supply Chain Questions to Ask Your Assembly Partner
08/16/2018 | Neil Sharp, JJS ManufacturingA key question for any OEM who may be considering outsourcing production is whether to maintain its existing supply chain or to hand those crucial purchasing decisions over to its assembly partner. This article highlights five questions to ask a potential assembly partner before handing over the responsibility for your supply chain management.
How Investment in Staff Well-Being Impacts Manufacturing Productivity
08/09/2018 | Sue Poole, JJS ManufacturingAs manufacturers seek to address the challenges of increasing efficiency, there's a greater emphasis on the value of high-performance working practices such as Lean manufacturing. But the emphasis on continual quality improvement processes can also have an indirect effect on employee health and well-being. Here's why manufacturers should invest in the well-being of its employees.
Overcoming Growth Challenges
07/19/2018 | Neil Sharp, JJS ManufacturingGrowth is usually seen by manufacturers as a good thing—a sign of success and a result of hard work. But if this growth isn’t planned for, or the manufacturer can’t react in time, growth can cause the same devastating results as if the business was in decline. This article looks at seven common areas that can cause manufacturers a headache when their business is growing, along with solutions to help ease the pain.