Improving SMT Yield and Reducing Defects: A Rauland Case Study
February 14, 2018 | Edward Hughes, AculonEstimated reading time: 6 minutes
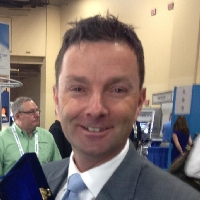
Ever-increasing demand for more complex boards that have higher densities of components means more challenges for SMT assembly operations and yields. Smaller component sizes and more densely packed PCBs lead to more powerful designs in much smaller product packages. These advancements have spurred a new set of challenges in building smaller and more complex assemblies.
Even though SMT products have been manufactured in high volume for decades, SMT line issues continue to be prevalent and new demands continue to pose new challenges. While the SMT print process is not complicated, controlling the outcome is complex. Having an underperforming SMT process results in lots of rework, lower throughput and added product costs as well as product reliability issues.
Rauland, a division of AMETEK Inc., is an 80-year integrated communications technology company that builds nurses call stations and school bell systems. The company responds to market needs globally with two distinct communication system product lines: Responder, designed for the healthcare industry; and Telecenter systems, which serve the educational market.
SMTA-certified Process Engineer Jimmy Crow works at Rauland’s highly sophisticated, FDA-compliant manufacturing facility that has state-of-the-art SMT equipment. At Rauland they build four- to eight-layer PCBs, place BGA, PCBGA, QFNs, typical double-sided boards, with its smallest part to date an 042 Aperio. Disciplined and quality conscious, Crow was not happy with the performance of his SMT line. There were too many defect and too much line downtime. Rework levels were also too high. His goal was to reduce SMT related defects and increase throughput while maintaining quality.
Studies have shown that 65% of defects from SMT lines comes from the screen-printing process, and Crow felt this was certainly the case in his factory. With a 22-second mean cycle time, the stencil printer was the gating process on the assembly line because it was stopped every two and a half minutes for cleaning. As a result, the SMT line would be empty of boards. The line badly needed balancing as no one wants the stencil printer to be the slowest item on assembly line.
Figure 1: Jimmy Crow delivered terrific results for Rauland: SMT-related defects were reduced by over 50%; throughput was increased by over 20%, and the company saved $1 million per year for three SMT lines.
To achieve this, Crow started by concentrating on the screen printing process, which has the largest impact over yield, throughput, quality, and downtime costs. He concentrated primarily on process improvements. Crow began a systematic root cause analysis of the defects.
1. Under Screen Cleaning
Crow’s initial focus was on the substances that clean the screen mechanically—the “paper” and the under-screen solvents used. After investigating different types of paper, Crow found there were better options out there than the current product. He selected a more porous wipe material that he thought would allow for better wiping. The Micro-Care Stencil easily handled the sharp edges on the SMT stencil, which often shredded old-style stencil wipes, causing defects and rework. The structure of the open paper also captures solder balls better than some of the closed structure fill papers.
2. Solvents
Crow then turned his attention to under-screen solvents. IPA (isopropyl alcohol) was problematic because newer solder pastes are comprised of synthetic resins, and the alcohol made the solder viscosity and machinery difficult to maintain. The cleaning properties were not good enough with IPA, as it did not clean and caused some paste bricks to cling to the aperture walls. He even turned off the IPA and sprayed nothing, and experienced the same results. So, he knew he needed to find a better solvent.
For the solvent, he wanted something that was efficient without being harmful to the screen printer. He ultimately chose Zestron Vigon UC160, an aqueous-based cleaning medium specifically designed for SMT stencil. The water-based formulation evaporates more slowly than IPA, but could clean with less wipes.
3. Nanocoating
In taking a systemic view of his SMT line issue, Crow had found a better paper and a better solvent, but he was still experiencing defects and downtime. They were still wiping every four to five boards based on the complexity of the stencil. Something was missing to make the process improvement complete.
Figure 2: With the cost calculator, management could easily see the result of the process improvement program.
That was when Crow met an SMT manufacturing expert, Chrys Shea, at an industry conference and found she had been conducting the same SMT line improvement programs and had delivered remarkable results. Her scientific approach to solving the SMT line issues mirrored Crow’s, but she had already found the missing ingredient that he was looking for, a nanocoating.
Shea's research had led her to advocate Aculon’s NanoClear, a stencil treatment technology, for several years as she had been able to demonstrate significant improvements in performance across many SMT lines.
Page 1 of 2
Testimonial
"We’re proud to call I-Connect007 a trusted partner. Their innovative approach and industry insight made our podcast collaboration a success by connecting us with the right audience and delivering real results."
Julia McCaffrey - NCAB GroupSuggested Items
BEST Inc. Introduces StikNPeel Rework Stencil for Fast, Simple and Reliable Solder Paste Printing
06/02/2025 | BEST Inc.BEST Inc., a leader in electronic component rework services, training, and products is pleased to introduce StikNPeel™ rework stencils. This innovative product is designed for printing solder paste for placement of gull wing devices such as quad flat packs (QFPs) or bottom terminated components.
KYZEN to Focus on Aqueous Cleaning and Stencil Cleaning at SMTA Juarez
05/20/2025 | KYZEN'KYZEN, the global leader in innovative environmentally responsible cleaning chemistries, will exhibit at the SMTA Juarez Expo and Tech Forum, scheduled to take place Thursday, June 5 at the Injectronics Convention Center in Ciudad Jarez, Chihuahua.
KYZEN to Spotlight Stencil Cleaning Solutions at SMTA Oregon
05/02/2025 | KYZEN'KYZEN, the global leader in innovative environmentally friendly cleaning chemistries, will exhibit at the SMTA Oregon Expo & Tech Forum, scheduled to take place on Tuesday, May 20 at the Wingspan Event and Conference Center in Hillsboro, OR. KYZEN’s cleaning expert Jeff Deering will be on-site at the expo providing information about stencil cleaning chemistries, including KYZEN E5631J.
KYZEN to Feature Stencil Cleaning and Aqueous Cleaners at SMTA Capital Expo and Tech Form
04/28/2025 | KYZEN'KYZEN, the global leader in innovative environmentally responsible cleaning chemistries, will exhibit at the SMTA Capital Expo and Tech Forum, scheduled to take place Thursday, May 8 at George Mason University – Mason Square in Arlington, VA.
KYZEN Focuses on Aqueous Cleaning and Stencil Cleaning at SMTA Wisconsin
04/24/2025 | KYZEN'KYZEN, the global leader in innovative environmentally responsible cleaning chemistries, will exhibit at the SMTA Wisconsin Expo and Tech Forum, scheduled to take place Tuesday, May 6 at the Crowne Plaza Milwaukee Airport. KYZEN will be on-site to provide attendees with information about aqueous cleaning chemistry AQUANOX A4618 and stencil cleaner KYZEN E5631J.