-
- News
- Books
Featured Books
- smt007 Magazine
Latest Issues
Current IssueWhat's Your Sweet Spot?
Are you in a niche that’s growing or shrinking? Is it time to reassess and refocus? We spotlight companies thriving by redefining or reinforcing their niche. What are their insights?
Moving Forward With Confidence
In this issue, we focus on sales and quoting, workforce training, new IPC leadership in the U.S. and Canada, the effects of tariffs, CFX standards, and much more—all designed to provide perspective as you move through the cloud bank of today's shifting economic market.
Intelligent Test and Inspection
Are you ready to explore the cutting-edge advancements shaping the electronics manufacturing industry? The May 2025 issue of SMT007 Magazine is packed with insights, innovations, and expert perspectives that you won’t want to miss.
- Articles
- Columns
- Links
- Media kit
||| MENU - smt007 Magazine
5 Techniques Used to Detect Counterfeit Electronic Components
March 16, 2018 | Danielle Olivier, JJS ManufacturingEstimated reading time: 3 minutes
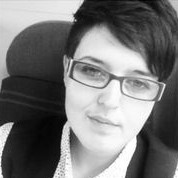
We are well aware of the threat of counterfeit components to electronic supply chains. Counterfeiting is a longstanding problem with the ability to grow in magnitude and scope if we are not vigilant. Which in turn, presents the electronic manufacturing industry with concern over genuine economic and innovative growth.
Although government pressure and private resources like those offered by ERAI Inc. have helped minimize the risk of counterfeit components from entering the supply chain, there is still and will most likely continue to be, a prominent threat.
So, what can you do to minimize this risk? Well, one of the most important things you can do to protect your supply chain is understand the ways in which you can detect counterfeit parts. In this article, we explore five different ways to detect counterfeit electronic components, so you can stay one step ahead in protecting your supply chain.
1. Sizing Discrepancies
By measuring the component height, length and width and then comparing these to the manufacturer’s specifications can give an indication that the part is genuine. If the measurements don’t match the manufacturer’s specifications, or there are variances across the batch you have received, then further investigation would be required.
2. Marking Authenticity
Blacktopping is a common technique used by counterfeiters which involves a thin layer of blacktopping material to cover the original part numbers and details. This is then re-printed with false markings in order to purposefully present the part as something that it isn’t. Arguably blacktopping is one of the most common techniques used by counterfeiters. This is obviously a cause for concern as the part you receive may be completely different to the part you ordered.
So how do you test for marking authenticity? A common test is to use an Acetone wash which is applied to the surface of a component helping to remove false printing or reveal the remnants of previous markings.
3. X-Ray Inspection
X-Ray inspection is a technique to examine the inner workings of the component. X- Ray can be used to show evidence of counterfeiting by highlighting the die, wire bonds and and any possible signs of delamination. Why is this important? Well, by examining the internals and comparing them to manufacturer specifications or controlled images of authentic parts, you will be able to determine whether the part is genuine.
4. Electrical Testing
Conducting electrical testing on suspect components can give you a better idea of whether the part is genuine or not by comparing the results to the tolerances recorded by the manufacturer. If the results are significantly different to the industry specifications, then further investigation would be required.
5. Decapsulation
If the other checks mentioned above are not conclusive, or you still have concerns over the authenticity of a part, it may be necessary to carry out decapsulation or 'de-lidding' of a sample component.
There are various techniques to carry out this process, often involving an acid solution, which therefore makes the process destructive. However, once this process is complete you can see the inner workings of a part using a high-powered microscope to visually inspect and verify factors such as manufacturer markings, defects to the die, correct typography, and accurate and authentic part numbers.
Identifying counterfeit components can be difficult as there may be more than one reason behind components failing individual tests. Component manufacturers have been known in the past to make production errors and then remark components themselves. So, not everything that looks suspect, is necessarily a counterfeit device.
However, by using multiple detection tests to examine incoming components you stand a far better chance of minimizing the risk of suspect devices entering your supply chain. You also provide your customer, the end user with greater confidence that when they take the product out of the box, or install it alongside their machinery, it will work first time, error free.
This article originally appeared on the JJS Manufacturing blog, which can be found here.
Suggested Items
Count On Tools Recognizes Donna Orr’s Ongoing Leadership and Impact Across 27+ Years
06/26/2025 | Count On ToolsCount On Tools, Inc. (COT), a leading provider of precision components and SMT spare parts, is proud to recognize Donna Orr, Executive Manager, for her continued dedication and leadership as she marks more than 27 years with the company.
A Record Year for the 75th Annual IEEE Electronic Components and Technology Conference (ECTC)
06/26/2025 | ECTCThe 75th annual 2025 IEEE Electronic Components and Technology Conference (ECTC), held at the Gaylord Texan Resort & Convention Center here May 27-30, had record attendance, a record number of paper submissions/presentations, record international and student participation, and a record number of exhibitors in a sold-out exhibition hall:
The Death of the Microsection
06/26/2025 | Bob Neves, Reliability Assessment Solutions, Inc.I got my start out of college grinding and polishing PCB microsections. My thumbs are a bit arthritic today because of the experience (microsection grinders know what I mean). Back then, via structures were rather large, and getting to the center in six steps of grinding and polishing was easy compared to what my team has been doing recently at the lab.
Specially Developed for Laser Plastic Welding from LPKF
06/25/2025 | LPKFLPKF introduces TherMoPro, a thermographic analysis system specifically developed for laser plastic welding that transforms thermal data into concrete actionable insights. Through automated capture, evaluation, and interpretation of surface temperature patterns immediately after welding, the system provides unprecedented process transparency that correlates with product joining quality and long-term product stability.
Fresh PCB Concepts: Assembly Challenges with Micro Components and Standard Solder Mask Practices
06/26/2025 | Team NCAB -- Column: Fresh PCB ConceptsMicro components have redefined what is possible in PCB design. With package sizes like 01005 and 0201 becoming more common in high-density layouts, designers are now expected to pack more performance into smaller spaces than ever before. While these advancements support miniaturization and functionality, they introduce new assembly challenges, particularly with traditional solder mask and legend application processes.