-
- News
- Books
Featured Books
- pcb007 Magazine
Latest Issues
Current IssueThe Hole Truth: Via Integrity in an HDI World
From the drilled hole to registration across multiple sequential lamination cycles, to the quality of your copper plating, via reliability in an HDI world is becoming an ever-greater challenge. This month we look at “The Hole Truth,” from creating the “perfect” via to how you can assure via quality and reliability, the first time, every time.
In Pursuit of Perfection: Defect Reduction
For bare PCB board fabrication, defect reduction is a critical aspect of a company's bottom line profitability. In this issue, we examine how imaging, etching, and plating processes can provide information and insight into reducing defects and increasing yields.
Voices of the Industry
We take the pulse of the PCB industry by sharing insights from leading fabricators and suppliers in this month's issue. We've gathered their thoughts on the new U.S. administration, spending, the war in Ukraine, and their most pressing needs. It’s an eye-opening and enlightening look behind the curtain.
- Articles
- Columns
- Links
- Media kit
||| MENU - pcb007 Magazine
Estimated reading time: 6 minutes
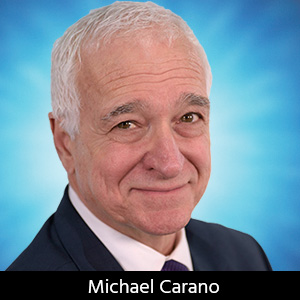
Contact Columnist Form
Trouble in Your Tank: Surface Preparation and Cleaning, Part 1
Copper foil is manufactured in a reel-to-reel continuous electrodeposition process (Figure 3). After the copper foil is formed the foil unwinds and passes through several treatments in a treater line. Copper dendrites are first grown on the rough side. These dendrites are brittle and need to be encapsulated with more ductile copper in a second step. This sequence is repeated, creating dendrites on top of dendrites. A zinc coating, or alternatively a brass coating, is then deposited, followed by the encapsulation with silane coupling agent, which forms strong bonds with the resin.On the smooth (drum) side, a very thin zinc (nickel) barrier is deposited, followed by a chromate/zinc coating. The nickel barrier prevents the formation of copper/chrome intermetallics that are difficult to remove with acid cleaners. In the past, thickness and chemical composition of chromium layers were not well-controlled and could lead to poor resist adhesion and low yields. Great progress has been made in controlling the conversion coating. The de sirable stain-proofing properties are balanced against the ability to remove a fair portion of the chromium layer with a simple process step such as treatment with 10% sulfuric acid.
One should note that chromate levels may vary for any number of reasons. There is no perfect chromate thickness or amount on the surface of the copper foil. Regardless, removing the chromate from the foil surface is the first step to enhancing photoresist adhesion. The chromate conversion coating serves as an anti-tarnish to preserve it and slow down the copper oxidation process. The chromium phase is actually a contiguous, hydrated Cr(OH)3 phase, with chromium predominantly at the oxidation state Cr+3, with interspersed zinc. The degree of hydration is critical to the removal of this layer in acid. Typical chromium coverage would be about 5 mg/m2.
Occasionally, suppliers also apply organic anti-tarnishes such as benzotriazole. It is debatable why and to what extent these conversion coatings should be removed prior to lamination. In the case of chromate conversion coatings, there is ample evidence that most dry films do not adhere too well to such a surface.
Also, in most innerlayer production processes, prelamination cleaning serves a dual purpose: the removal of chromate serves film adhesion but is also necessary to assure good oxide formation for multilayer bonding.
In addition, failure to effectively remove chromates and other soils will lead to what we call differential etching. Essentially this means that during the surface roughening step (after chromate and soil removal) employing a microetch formulation, the roughening will be less than optimum due to incomplete chromate and other soil removal. This in turn negatively impacts adhesion of resists. Understandably, in those areas where organic soils and chromates remain, the microetch will have compromised ability to provide a uniformly structured surface.
In-House Evaluation and Data Gathering
Due to the importance of surface preparation in printed circuit board manufacturing, the PCB fabricator should embark on an evaluation of current chemical and mechanical processes available. Some of the evaluations will require working closely with the dry film and chemical suppliers.
When evaluating the effectiveness of surface preparation for primary imaging, there are several data points listed below that will influence the success or failure of dry film adhesion:
- Surface profilometry with different microetches
- Effect of chromate removing chemistry on surface cleanliness and topography
- SEM analysis of treated copper surface (utilizing different microetch chemistries)
- Film/mask peel tests after chemical treatment
- Sidewall SEM analysis after development (comparing differing chemical prep methods)
Examples of generic chemistry performance on copper surfaces are shown in Figure 4.
Figure 4: Examples of microetched surfaces. Hydrogen peroxide/sulfuric acid microetch (left); oxone (middle); sodium persulfate (right).
Figure 5: Sidewall of developed photoresist (20-micron line = 0.8 mil)
As shown in Figure 4, the various generic microetches impart stark differences in topography. One must take these differences into account when evaluating chemical clean processes and adhesion. In a future column, we will explore soldermask adhesion issues. This is critical due to the aggressive nature of several final finishes including ENIG and immersion tin.
Desired Outcomes
The overarching task for the fabricator is to optimize the cleaning and surface preparation processes of the copper surfaces. The engineer will also need to finalize data including supporting documentation as to differences in the grain structures of different microetch formulations and their effect on the copper foils.
Recognizing these differences, the engineer will provide recommendations as to which combination of cleaners and microetches provides optimal surface profiles to meet current industry criteria, including but not limited to:
1. Adhesion performance for sub 5-mil lines and spaces for primary resist (Figure 5)
2. Ability to hold soldermask dams
3. Improve soldermask adhesion under various conditions including the ability to withstand lifting when exposed to ENIG and immersion tin plating processes
4. Documented yield improvements from customers willing to share data
In the end, lines and spaces are only getting finer. Sub 4-mil lines and spaces are becoming mainstream. Simply relying on laser direct imaging will not mitigate issues related to less than optimal adhesion of film to the surface.
Ensuring that the copper foil surface has been properly cleaned of soils and chromates is the first step in ensuring good photoresist adhesion.
This is then followed by surface roughening with chemistry to provide sufficient topography for the film to adhere.
Michael Carano is VP of technology and business development for RBP Chemical Technology. To reach Carano, or read past columns, click here.
Page 2 of 2More Columns from Trouble in Your Tank
Trouble in Your Tank: Can You Drill the Perfect Hole?Trouble in Your Tank: Yield Improvement and Reliability
Trouble in Your Tank: Causes of Plating Voids, Pre-electroless Copper
Trouble in Your Tank: Organic Addition Agents in Electrolytic Copper Plating
Trouble in Your Tank: Interconnect Defect—The Three Degrees of Separation
Trouble in Your Tank: Things You Can Do for Better Wet Process Control
Trouble in Your Tank: Processes to Support IC Substrates and Advanced Packaging, Part 5
Trouble in Your Tank: Materials for PWB Fabrication—Drillability and Metallization