-
-
News
News Highlights
- Books
Featured Books
- smt007 Magazine
Latest Issues
Current IssueWhat's Your Sweet Spot?
Are you in a niche that’s growing or shrinking? Is it time to reassess and refocus? We spotlight companies thriving by redefining or reinforcing their niche. What are their insights?
Moving Forward With Confidence
In this issue, we focus on sales and quoting, workforce training, new IPC leadership in the U.S. and Canada, the effects of tariffs, CFX standards, and much more—all designed to provide perspective as you move through the cloud bank of today's shifting economic market.
Intelligent Test and Inspection
Are you ready to explore the cutting-edge advancements shaping the electronics manufacturing industry? The May 2025 issue of SMT007 Magazine is packed with insights, innovations, and expert perspectives that you won’t want to miss.
- Articles
- Columns
- Links
- Media kit
||| MENU - smt007 Magazine
Industry 4.0 Concerns
April 27, 2018 | Russell Poppe, JJS ManufacturingEstimated reading time: 4 minutes
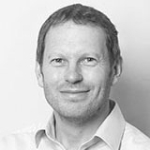
The fastest way for manufacturers to achieve growth in a new world of industrial connectivity is to leverage new technologies.
A transition to automated data and process management is irrefutable, and while this heralds smart supply chains that bring enhanced agility, productivity and profitability, many are adopting a "wait and see" approach.
Industry 4.0 is one of the five areas the UK government plans to focus on developing in a bid to boost the post-Brexit British economy. This came after the announcement that £4.7 billion would be available for research and development into robots, artificial intelligence, 5G mobile technology and smart energy.
Only 11% of UK manufacturers think the UK is geared up to take advantage of the fourth industrial evolution, which begs the question: why are we still so hesitant about its implementation?
In this article, we look at the four key concerns for manufacturers and aim to eradicate any fears surrounding your transition.
Employees
As the PwC Annual Survey suggests, "The biggest challenge for industrial leaders isn't technology – it's the people."
The future is not complete automation; this is simply not realistic. There will still be a great need for human intervention and supervision.
Training programs may need a rethink and recruitment processes will need tweaking. This causes concern for those in higher management and HR.
In fact, a need for re-training could become a lucrative business itself with the potential introduction of learning factories.
It's natural for employees to feel intimidated by new technologies and AI (artificial intelligence) that could inevitably replace them. This increases the pressure on CEOs and HR departments. But we can be safe in the knowledge that the role of the workforce is evolving, rather than vanishing.
Skilled individuals and teams will become multi-disciplined and develop skillsets in more challenging areas. Rather than performing mundane tasks, their skillsets will be developed to oversee and coordinate production.
There are many skills machines can’t emulate, such as critical thinking, management of complex situations and emotional intelligence. By preparing new training schemes that empower employees to embrace and develop Industry 4.0 technologies, they become more open to change, able to adapt to new roles and working environments and accustomed to continuous interdisciplinary learning.
Health and Safety
With a highly adaptable workspace comes new health and safety risks. Health and safety is at the heart of any employer's risk assessments and new machinery implementation.
Risk assessments of equipment will now have to be more rigorous than ever, taking into account all aspects, from individual components right through to operator ‘touch points’.
Safety sensors are also available, where the system can immediately sense if a human operator has moved into an unsafe area or is in a hazardous position. Innovative programming can allow the machinery to slow down to safe speed, or power down completely to allow the individual to move away from the hazard.
Much of the new equipment and machinery introduced during the transition will be built with safety features. For example, compatible drives which can be used to create a machine protocol with a unique number, highlighting immediately a potential safety issue if a different protocol is used. Look out for these where feasible to minimize risks and the need for intensive testing.
Cyber Security
Today, according to Gartner, there are five billion connected devices worldwide. This is monumental progression for industrial connectivity.
But with increased connectivity comes the increased risk of cyber threats. And with innovations such as remote control of machinery and robotics, it creates opportunities for remote hackers.
The risks of data and manipulation affecting your entire supply chain are heightened.
This can be managed by asking your EMS provider if they have an auditable security policy and can demonstrate how your IP will be kept safe and secure.
If and where possible, select equipment and software with built in safety features.
Technology Implementation
The thought of AI has many business owners hot under the collar. Cost, maintenance, and the unknown potential of machine-to-machine communication… it can all seem a bit out of reach—a bit sci-fi, even.
With almost half the chief executives questioned as a part of PwC’s annual survey, expressing concerns that investors, employees and the wider public would distrust the concept, it’s not surprising that many remain cautious.
As new technologies emerge, they tend to have a ripple effect on other areas within the industry. The wrong approach could set a company up financial, operational and reputational damage.
Smart robots and digital twinning for example, are making it a possibility for engineers to control, amend and test operational equipment remotely. But how can you guarantee your systems will communicate with each other effectively?
With a robust quality management system in place, you can identify and avoid damaging scenarios and abnormalities before they take place. The end goal is acceleration through introducing exponential technologies—welcoming processes that let machines do the work for us, but where humans ultimately maintain the control. Employers and employees need to be quick to learn if we are to successfully implement and control such intelligence systems.
Rather than adopting the ‘wait and see’ approach—which could see you fall behind competitors in the long run—keep an eye on competitors and monitor new technologies to see how they can be used to improve delivery customer satisfaction and efficiencies within your own production lines.
Of course, manufacturers are inherently cautious. But we advise you take the ‘think big, start small’ approach. Transition is still a work-in-progress for many. Start testing new methods and technologies to and stay up to date with the market. This will equip you with the information to tackle any concerns head on, reassuring your employees, stakeholders and customers along the way.
This article originally appeared on the JJS Manufacturing blog, which can be found here.
Suggested Items
Real Time with... IPC APEX EXPO 2025: Aster—Enhancing Design for Effective Testing Strategies
04/18/2025 | Real Time with...IPC APEX EXPOWill Webb, technical director at Aster, stresses the importance of testability in design, emphasizing early engagement to identify testing issues. This discussion covers the integration of testing with Industry 4.0, the need for good test coverage, and adherence to industry standards. Innovations like boundary scan testing and new tools for cluster testing are introduced, highlighting advancements in optimizing testing workflows and collaboration with other tools.
Real Time with… IPC APEX EXPO 2025: Schmoll America Showcasing Four Advanced Machines
03/05/2025 | Real Time with...IPC APEX EXPOIn an expansive booth, Schmoll America is showcasing three advanced Schmoll machines and one from Impex, its partner company. Kurt emphasizes Schmoll's commitment to growth and excellence as Schmoll America approaches its first anniversary. Stop by booth 4123 to see the action.
Smart Factory Insights: The Costs of Legacy Thinking
12/01/2021 | Michael Ford -- Column: Smart Factory InsightsAs humans, we learn facts, gain impressions, create solutions, put practices into place, and move onto our next challenge. Over time, our intent is to create a legacy of value, but in many cases, we are creating legacies in a different sense. Our knowledge, experience, and creations age or become superseded, but there is resistance to replace or update. An increasing gap develops between perception and reality. Younger, more agile peers take advantage, get ahead, and we look away, thinking that they don’t know what they are doing. Though a natural human phenomenon, decision-makers in manufacturing today need to bear this mind more than ever.
Managing Cyber-Threats Within Electronics Manufacturing
11/16/2018 | Neil Sharp, JJS ManufacturingThe rise of the 4th Industrial Revolution (4IR) has brought with it digital interconnectivity that offers unprecedented opportunities for original equipment manufacturers (OEMs). But with that openness there also comes risk—the threat of the loss of data, the theft of capital or intellectual property, and the disruption of access to systems or operational technology—all of which can impede businesses and impact on trade.
IoT: Driving Change in Manufacturing
10/15/2018 | Stephen Las Marias, I-Connect007In the manufacturing world, the Internet of Things (IoT) can be seen as an element of Industry 4.0. The idea behind it is that factories would evolve to become smarter, to become a lot more flexible—to be able to make the products that customers want, basically at any time that they need.