-
- News
- Books
Featured Books
- smt007 Magazine
Latest Issues
Current IssueWhat's Your Sweet Spot?
Are you in a niche that’s growing or shrinking? Is it time to reassess and refocus? We spotlight companies thriving by redefining or reinforcing their niche. What are their insights?
Moving Forward With Confidence
In this issue, we focus on sales and quoting, workforce training, new IPC leadership in the U.S. and Canada, the effects of tariffs, CFX standards, and much more—all designed to provide perspective as you move through the cloud bank of today's shifting economic market.
Intelligent Test and Inspection
Are you ready to explore the cutting-edge advancements shaping the electronics manufacturing industry? The May 2025 issue of SMT007 Magazine is packed with insights, innovations, and expert perspectives that you won’t want to miss.
- Articles
- Columns
- Links
- Media kit
||| MENU - smt007 Magazine
Estimated reading time: 4 minutes
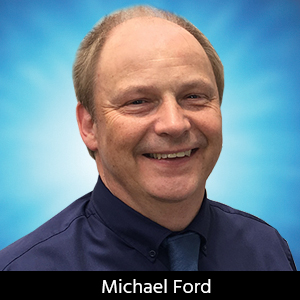
Smart Factory Insights: The Costs of Legacy Thinking
As humans, we learn facts, gain impressions, create solutions, put practices into place, and move onto our next challenge. Over time, our intent is to create a legacy of value, but in many cases, we are creating legacies in a different sense. Our knowledge, experience, and creations age or become superseded, but there is resistance to replace or update. An increasing gap develops between perception and reality. Younger, more agile peers take advantage, get ahead, and we look away, thinking that they don’t know what they are doing. Though a natural human phenomenon, decision-makers in manufacturing today need to bear this mind more than ever.
As a civilization, we have achieved so much—men on the moon, supercomputing power in the palm of our hands, and we’ve even made the planet just a little bit warmer. In manufacturing, we benefit from faster, more flexible automation; smaller, lighter materials; greater throughputs; near-perfect quality; and decreased costs, with a supply-chain to die for.
Our intent was to create excellence. Being in control in manufacturing is paramount, having removed as many unknown sources as possible of variation and change. Practices put in place address challenges that once plagued operations, and that maximized benefits and profit. It has meant we took our eyes off the ball.
The world is going through another fundamental change. In fact, this time, a few different interacting changes, are occurring at the same time. Whether it is global or local politics, a pandemic, or bad weather, the message is finally getting across that there really are fundamental challenges ahead, not the least within manufacturing, which of course, brings new opportunities.
In the manufacturing world, the advancement of software within inspection, test, and assembly machines, as well as operational and business solutions such as MES, MOM, and ERP, has been radical over recent years. It is more difficult to see the progress of software changes as compared to machine hardware technology, which you can see and for which there are clear specifications. Most of the software value is not visible, with thousands of elements that contribute, which are not, however, practical to detail and explain. Even the human interface, the shopwindow of software, has shrunk in significance. Advancement of software brings more automation of decision-making, and even “creativity,” but less human interaction and involvement. One manufacturer was unhappy when they upgraded their product design data import from Gerber to the use of IPC-2581. Instead of a screen full of options and configurations needed to cope with the randomness of Gerber and the myriad associated supporting files, there was just one button, labelled “Import 2581.” The feeling of being in control on behalf of the user is replaced by the cleverness within the software and the data format itself. Which do we think is the quicker and most reliable?
More and more, we see advanced technologies being embedded within software. Incredible improvements in factory management, active quality, supply-chain, and even image sensors and inspection algorithms, often go unnoticed and are taken for granted, certainly lacking appreciation of value. Vendors often attempt to recreate that feeling of interaction, making eye-catching game-ready graphical displays in the hope that people will notice that the software is there and doing something.
Against this backdrop, it is difficult to assess progression and therefore the need for modern software, to make confident, justified decisions that create changes in current manufacturing practices. The purchase and use of software very often is based on information and perceptions dating from many years ago. Even in a period of months, values from software become significantly enhanced. Another factor, however, is that not all vendors are keeping pace, and setting the state of the art for the industry. Vendors are also subject to the same difficulties in making paradigm-changing choices in the development of their products. We see many large software platforms, popular in the industry, date back decades since their initial creation, which will never be able to evolve quickly enough. Progressive vendors have reinvented solutions that take advantage of the latest technologies, such as standardized IIoT messaging, and use it to create previously unachievable functionality and automation. It is essential to regularly reset perceptions and take a fresh look into which software solutions have really evolved and which companies are driving the industry, helping manufacturing adapt and recover, knowing that perceptions of limitations from years ago have long since been addressed. Today’s software technology, architecture, and reliability is a long way ahead of what you might expect.
As most manufacturers now scramble around for materials, machines, and spare parts, as well as skilled and experienced labor, remember that the most modern software from machine vendors, MES providers, and others are likely to be far more advanced than you realize, which reflects on the ability to cope much more easily with the business-related changes and limitations that are being forced upon us all. The argument that any change, including that of new software, brings its own variations and challenges, as well as thinking that it may be too late now as the global challenges are already with us, are not valid. The amount of control and visibility that the latest software provides is at least an order of magnitude greater than the work and effort to introduce the software.
As for global challenges coming to an end, many think that is unrealistic, both in terms of dealing with ongoing consequences of what has happened already—for example, with the pandemic—as well as worsening factors such as climate change and potentially political issues, which are forcing rapid change in government policy, risk management, and customer demand choices. The worst and the best are yet to come. The most modern software is your friend and ally as we face the future together.
This column originally appeared in the November 2021 issue of SMT007 Magazine.
More Columns from Smart Factory Insights
Smart Factory Insights: Making Rework a Smart Business OpportunitySmart Factory Insights: The Sustainability Gold Rush
Smart Factory Insights: Today’s Manufacturing Jobs Require a New Skill Set
Smart Factory Insights: Compose Yourself, Mr. Ford
Smart Factory Insights: The Smart Business Case for Local PCB Manufacturing
Smart Factory Insights: Manufacturing Digital Twin—Spanners in the Works
Smart Factory Insights: Machines, People, and AI
Smart Factory Insights: Is Sustainability in Manufacturing a Benefit or Burden?