-
- News
- Books
Featured Books
- smt007 Magazine
Latest Issues
Current IssueSupply Chain Strategies
A successful brand is built on strong customer relationships—anchored by a well-orchestrated supply chain at its core. This month, we look at how managing your supply chain directly influences customer perception.
What's Your Sweet Spot?
Are you in a niche that’s growing or shrinking? Is it time to reassess and refocus? We spotlight companies thriving by redefining or reinforcing their niche. What are their insights?
Moving Forward With Confidence
In this issue, we focus on sales and quoting, workforce training, new IPC leadership in the U.S. and Canada, the effects of tariffs, CFX standards, and much more—all designed to provide perspective as you move through the cloud bank of today's shifting economic market.
- Articles
- Columns
- Links
- Media kit
||| MENU - smt007 Magazine
Under the Hood: Solder Joint Reliability
May 21, 2018 | Burton Carpenter, NXP Semiconductors Inc.Estimated reading time: 3 minutes
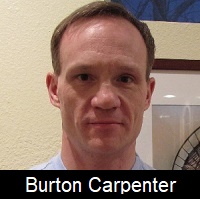
The automotive industry continues to drive increased solder joint reliability (SJR) for under-the-hood applications. One aspect of SJR, temperature cycle on board (TCoB) assesses thermal fatigue resistance of solder interconnection between component and PCB during temperature excursions. In some instances, requirements on number of cycles to first failure have increased 2x over previous product generations.
It has been long established that packages using NSMD BGA pads were more resilient than ones with SMD pads to fatigue-induced solder joint cracks. However, NSMD pads in our previous investigations on 292MAPBGA and 416PBGA packages failed sooner in AATS testing due to an alternate failure mode: substrate Cu trace cracks.
Detailed failure analysis revealed that these cracks occurred exclusively on BGA pads in the die shadow. This led to the idea that a mixed design—NSMD pads outside the die shadow, while maintaining SMD pads under the die—could perform better than a pure SMD design.
Separately, lower CTE substrate dielectric materials were under investigation as a means to reduce package warpage. Below Tg, the mold compound CTE is 9ppm/°C. The standard substrate dielectric CTE is 16ppm/°C, resulting in considerable package warpage at lower temperatures. It was hypothesized that lowering the substrate dielectric material CTE to 11ppm/°C would reduce package warpage which in turn should reduce solder joint strain thereby increasing solder joint lifetime.
Table 1: Package details. DOE variables in yellow.
A six-cell experimental matrix was run to study the impact of these two variables (substrate dielectric material and package pad design type.) These experiments used standard daisy-chain temperature cycle testing methodology. Assemblies were monitored in situ to detect failures as they occurred, and 2-parameter Weibull failure distributions were fit to the data. Various metrics derived from the Weibull fits were regressed against the DOE variables to determine which had significant impact on solder joint lifetime, and to what degree.
Crack growth was assessed using cross-section and dye-and-pry techniques on unmonitored assemblies that were removed from the chambers at fixed read points. Conclusions on the impact of the parameters were determined based on the totality of electrical test and crack growth data.
EXPERIMENTAL:
Design
The package attributes are summarized in Table 1. Those highlighted in yellow were varied in the experiment. The substrate dielectric details are in Table 2.
BGA arrays are shown in Figure 1. The baseline SMD design in Figure 1a contained only SMD pads. Hybrid-A in Figure 1b used the same footprint, but the outer four rings were substituted with NSMD pads, while the pads at the die edge were maintained as SMD.
Table 2: Substrate dielectric mechanical properties.
By contrast, the outer six rings were NSMD for Hybrid-B, encompassing the die edge. In all cases, the SMD pad SRO (solder resist opening) was 0.45mm. To compensate for solder wetting down the pad sidewall, the NSMD pads on the hybrid designs were slightly smaller to produce a similar ball height.
These packages were daisy-chain test vehicles with pairs of solder joints electrically connected. A complete circuit was created by connecting pairs on the PCB side that were skipped on the package. All solder joints were monitored as one “net.” A failure on any solder joint meant the remaining solder joints could no longer be electrically monitored.
Figure 1: BGA footprint showing arrangement of SMD and NSMD pads for the three different designs.
Except where parameters were intentionally varied, the daisy-chain packages were mechanically similar to the final products: same die size, area and thickness. Similarly, the same material sets were used: mold compound, die attach, and assembly factory.
To read the full version of this article, which appeared in the April 2018 issue of SMT007 Magazine, click here.
Testimonial
"We’re proud to call I-Connect007 a trusted partner. Their innovative approach and industry insight made our podcast collaboration a success by connecting us with the right audience and delivering real results."
Julia McCaffrey - NCAB GroupSuggested Items
Indium Promotes Huang to Senior Manager, Marketing Communications
08/28/2025 | Indium CorporationWith its commitment to innovation and growth through employee development, Indium Corporation announces the promotion of Jingya Huang to Senior Manager, Marketing Communications, to continue to lead the company’s branding and promotional efforts.
Rehm Academy Expands Its Training Program
08/28/2025 | Rehm Thermal SystemsThe demands on modern industrial companies and employees continue to rise, and therefore, the topic of further education is becoming increasingly important today.
MacDermid Alpha Awarded for Innovation: Driving Process Optimization and Efficiency with Major Indian EMS Provider
08/28/2025 | MacDermid Alpha Electronics SolutionsMacDermid Alpha Electronics Solutions, a leading global supplier of integrated materials for the electronics industry, is recognized by one of India’s top EMS providers, Syrma SGS, with an award for innovation that advanced process optimization, enhanced operational efficiency, and yield gains.
Integrated Solutions for Board-level Reliability: A Smarter Path Forward
08/27/2025 | Alan Gardner, MacDermid Alpha Electronics SolutionsIn today’s electronics manufacturing landscape, reliability is no longer just a benchmark but a business imperative. As industries such as automotive, aerospace, and high-performance computing (HPC) push the boundaries of innovation, the demand for dependable board-level performance under extreme conditions has never been greater.
ZESTRON Expands Capabilities with Addition of the EPS by i-Tech AG 75 Pallet Cleaning System
08/26/2025 | ZESTRONZESTRON, the global leader in high-precision cleaning solutions and services, is excited to announce the addition of a new capability in its Technical Center in Manassas, VA: