-
- News
- Books
Featured Books
- smt007 Magazine
Latest Issues
Current IssueSupply Chain Strategies
A successful brand is built on strong customer relationships—anchored by a well-orchestrated supply chain at its core. This month, we look at how managing your supply chain directly influences customer perception.
What's Your Sweet Spot?
Are you in a niche that’s growing or shrinking? Is it time to reassess and refocus? We spotlight companies thriving by redefining or reinforcing their niche. What are their insights?
Moving Forward With Confidence
In this issue, we focus on sales and quoting, workforce training, new IPC leadership in the U.S. and Canada, the effects of tariffs, CFX standards, and much more—all designed to provide perspective as you move through the cloud bank of today's shifting economic market.
- Articles
- Columns
- Links
- Media kit
||| MENU - smt007 Magazine
Estimated reading time: 5 minutes
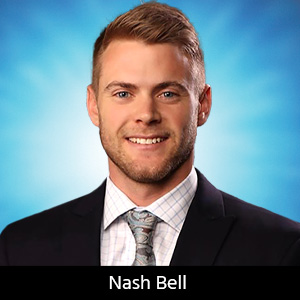
Masking of Conformal Coating During Assembly and Rework
Masking of printed circuit boards post rework/repair as well as for initial PCB assembly is often required if the PCB is to be conformal coated. If a board that has conformal coating on it needs to be reworked or repaired, the conformal coating needs to first be removed before the operation of rework or repair can take place. Once the board has been inspected, tested and cleaned, the conformal coating needs to be re-applied to the area of rework or repair. A conformal coating keep-out area drawing is essential in determining which components require masking. The following discussion centers around the various options for conformal coating masking via a liquid application process.
For purposes of this discussion, rework is defined as the removal and replacement of a component to meet initial specifications and performance characteristics of the board. Repair is defined as restoration of physical damage done to a PCB that brings the board back to functionally but may not meet the original performance intentions. Parylene masking and de-masking is not part of this discussion.
There are numerous options available for conformal coating masking. The most common methods for masking off or protecting select areas of the PCB or components themselves are the following:
- Precut tape dots
- Laser-cut custom tape shape
- Tape that is hand cut and trimmed to size
- Liquid latex
- Silicone boots
- 3D printed custom shapes
Precut Tape Dots
Precut tape dots are effective for conformal coating masking of flat areas to the PCB areas like test points and mounting holes. These are precut stickers, usually round, of standard sizes and die cut; they are available in polyester, polyimide, Kapton and other materials. They are supplied on a roll and are pulled off the release liner one at a time. They are cost-effective for small to medium production runs.
Laser Cut Tape Shapes
Laser cut tape shapes are precision cut from flat sheets of tape material and can be fabricated using Kapton, flexible tape like 3M Type 401 or others. This method is ideal for complex shapes for prototype or small-volume builds as they reduce masking time and can be delivered quickly. The shapes are generated from the board’s Gerber files and can be used not only to protect flat areas but can be designed to tape over 3D components like connectors and headers requiring masking. The technician simply peels the material off the release liner and places it on the board or over the component. The shapes can be grouped together to visually indicate that each tape has been removed from the backing material, helping ensure that all areas requiring masking are masked.
Hand Cut and Trimmed Tape
In this masking method, the tape shapes are cut to size either coming right off the roll or the component is wrapped by the rework technician and trimmed afterwards. Performing the cutting operation on the board is dangerous as parts or boards can be damaged. Performing the cutting after peeling back the roll can be dangerous as the operator can potentially cut their hands. For prototypes or for very odd-shaped areas, it is a very flexible masking method. However, it is a very time-consuming process for both masking and de-masking. The charge generation process during de-masking operations must ensure that the components and assembly are protected from any adverse ESD events (sometimes requiring an air ionizer in the masking/de-masking area).
Liquid Latex, aka “Peelable Mask”
Liquid latex is a thixotropic material designed to be, among other things, a protection against unwanted conformal coating spray. It can be dispensed from a syringe or plastic-tipped squeeze bottle. It is typically cured on the board at room temperature over a three-hour range. After curing and application of the conformal coating, the masking material is simply peeled from the board and disposed of with the regular waste stream. This is ideal for areas that may be tough to get at with the tape. In addition, this type of masking material is ideal if you do not want the conformal coating “wicking up” the contact leads. At times, both the taping methods and the peelable mask method will be employed on the same board with the peelable mask at the board interface. Be careful in using natural latex as these formulations are heavily ammoniated and therefore can impact the PCB laminate surface. If the peelable mask cures very hard, it may rip off components, component leads or PCB laminate during the de-masking process. Conversely, the peelable mask breaks up easily during removal, so you may leave behind residual material, which may cause long-term reliability problems.
Silicone Boots
Silicone boots, customized for different connector and other electronic components, is another conformal coating masking method. They are often used for higher assembly volume jobs to greatly reduce the time and effort required for masking. The boots, due to their self-sealing nature, do not leak as frequently as tape dots and masks, thereby eliminating the need for coating re-work. For higher board volumes, these boots are very cost-effective and can reduce the masking time by 60-70%. One drawback to this masking method is that they will not work in conformal coating dip applications. Some boots can be re-used 125-200 times, depending on their care, and thereby driving the cost-per- use down.
3D Printing of Custom Boots
Another possibility for masking certain areas of a PCB includes the 3D printing of covers or boots to cover components. These 3D printing covers can be made from a variety of materials and offer the same potential benefits as the silicone boots. The material of the boots will determine the seal around the devices as well as temperature that the boots can withstand in the curing process. While the 3D printers are very cost-effective today, their low precision, the length of time to print, the lack of ability of the lower end machines to print heat-resistant pliable materials, and the need to have 3D CAD capability within the SMT assembly operation make this option limited.
Tape Materials
All the tape derivative options may need to be tested. For example, they may or may not be able to prevent uncured coating material from leaching underneath the tape parting line. For example, some tape adhesives leave residues behind that may inhibit the long-term reliability of the electronics assembly by reducing SIR values or allowing accelerated dendritic growth to take place. Adhesives used in these tapes must have properties such that they do not peel off the cured coating material, leave unwanted residue on the PCB, or damage components. If the OEM specifies the allowable materials it may limit your options on material choices and type of masking. For example, even the slitting knife-coating material may cause unwanted silicone debris or de-wetting problems. Ensure that when these tape-based masking methods are used, all tape materials are compatible with the coating materials and the coating process being employed.
Summary
Whatever spraying method is employed in applying the conformal coating, having a handle on what type of masking method to use is critical to making sure the PCB assembly, rework or repair process is done properly and cost-effectively.
More Columns from Knocking Down the Bone Pile
Knocking Down the Bone Pile: Addressing End-of-life Component Solderability Issues, Part 4Knocking Down the Bone Pile: Tin Whisker Mitigation in Aerospace Applications, Part 3
Knocking Down the Bone Pile: Gold Mitigation for Class 2 Electronics
Knocking Down the Bone Pile: Basics of Component Lead Tinning
Knocking Down the Bone Pile: Package on Package Rework—Skill Required
Knocking Down the Bone Pile: 2023’s Top Challenges in BGA Rework
Knocking Down the Bone Pile: Eliminating Solder Balls in Hand Soldering
Knocking Down the Bone Pile: Opening a Trace on the Surface of a PCB