-
- News
- Books
Featured Books
- pcb007 Magazine
Latest Issues
Current IssueIn Pursuit of Perfection: Defect Reduction
For bare PCB board fabrication, defect reduction is a critical aspect of a company's bottom line profitability. In this issue, we examine how imaging, etching, and plating processes can provide information and insight into reducing defects and increasing yields.
Voices of the Industry
We take the pulse of the PCB industry by sharing insights from leading fabricators and suppliers in this month's issue. We've gathered their thoughts on the new U.S. administration, spending, the war in Ukraine, and their most pressing needs. It’s an eye-opening and enlightening look behind the curtain.
The Essential Guide to Surface Finishes
We go back to basics this month with a recount of a little history, and look forward to addressing the many challenges that high density, high frequency, adhesion, SI, and corrosion concerns for harsh environments bring to the fore. We compare and contrast surface finishes by type and application, take a hard look at the many iterations of gold plating, and address palladium as a surface finish.
- Articles
- Columns
Search Console
- Links
- Media kit
||| MENU - pcb007 Magazine
Estimated reading time: 4 minutes
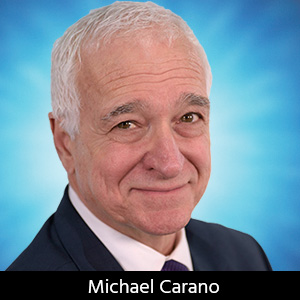
Contact Columnist Form
Trouble in Your Tank: Surface Preparation and Cleaning, Part 2
Some type of cleaning and surface structuring is required in virtually every step of the printed circuit manufacturing process, from preparing the raw laminate for etch or plating resist to final assembly board cleaning before shipment. In this edition of “Trouble in Your Tank,” I will attempt to cover most of the general cleaning problems that can occur in any of these steps and, where possible, any problems unique to a specific manufacturing step. Many cleaning procedures are tightly integrated within certain manufacturing processes, such as plating, and may also be covered in other columns or feature articles.
This section is divided into two categories: mechanical cleaning surface preparation and chemical cleaning. However, this is only a general presentation. More details with chemical and mechanical cleaning will be covered in future columns.
One should make a clear distinction between the method of surface preparation and the nature of the surface alteration affected by such a method. The mechanical method of brush scrubbing changes the topography as well as the chemical composition of the surface (e.g., removal of oxide, chromium, etc.). On the other hand, the mechanical method of jet-pumice scrubbing restructures the topography with little or no abrasion of copper. The chemical composition of the surface stays very much the same, except for the removal of loosely held oxide and some redistribution (e.g., of chromium from conversion coatings into deeper layers of the surface). A chemical surface preparation method such as alkaline cleaning will change the chemical nature of the surface by removing organic contaminants, but will not affect the topography, whereas a persulfate etch will change both.
In general, surface preparation is done to assure good adhesion of metal, dielectric, photoresist, or soldermask to the prepared surface, although avoiding excessive adhesion could also be the object. Take the example of surface preparation before dry photoresist lamination. One can measure the surface profile of the copper surface using the technique of profilometry. This technique measures changes in the structure or profile of a surface. The data collected gives information such as[1]:
Ra—Arithmetic mean surface roughness: Arithmetical mean of the sums of all profile values.
Rt—Total height of the roughness profile: Sum from the height Zp of the highest profile peak and the depth Zv of the lowest profile valley within the measured length (ln).
Rzi—Maximum height of the roughness profile: Sum from the height of the highest profile peak and the depth of the lowest profile valley within a sampling length.
Rz (max)—Maximum surface roughness: Largest of the five Rzi values from the five sampling lengths “i” over the total measured length.
Rz—Surface roughness depth: Mean value of the five Rz values from the five sampling lengths over the total measured length.
One must be careful about encountering differential etching. This occurs when spots of organic residues have not been cleaned from the surface of the copper. One common source of these residues is epoxy or pre-preg dust that can deposit on the copper.
In addition, the overall surface roughness of the material is often contributed by the glass fabric styles and thicknesses. This is especially notable since the industry has moved to thinner core materials and thinner copper foils. Be prudent when working with these thinner materials as mechanical surface preparation may stretch thinner materials. In contrast, while chemical cleaning will not stretch the material, excessive copper removal may impact signal conductivity. Excessive copper removal or an overly roughened surface will impact signal integrity resulting in insertion loss at high frequencies.
Several types of copper foil are used today. The two main categories are electrodeposited (ED) foil and rolled annealed (RA) foil. And within each of these categories are several variations. As an example, there are several foil types within the ED category. These differ based on the extent of the copper pro file. In addition, during the past several years, low profile ED copper foils have been introduced with an enhancement known as reverse treat. Essentially, the shiny side of the copper foil (also known as drum side) has been treated with material to enhance the bond of the photoresist to the copper foil (Figure 1).
It is important to note that if one employs RTF foil, there should be minimal if any microetching or scrubbing of the RTF. Any aggressive etching or cleaning will negatively impact the topography one is paying for with RTF. It is suggested however that an alkaline cleaner fol lowed by an acid cleaner (to remove the chromate conversion coating) be used. One must still have a clean copper surface to facilitate resist adhesion. PCB007
References 1. Mitutoyo website.
Michael Carano is VP of technology and business development for RBP Chemical Technology. To reach Carano, or read past columns, click here.
This article originally appeared in the May 2018 issue of PCB007 Magazine, click here.
More Columns from Trouble in Your Tank
Trouble in Your Tank: Yield Improvement and ReliabilityTrouble in Your Tank: Causes of Plating Voids, Pre-electroless Copper
Trouble in Your Tank: Organic Addition Agents in Electrolytic Copper Plating
Trouble in Your Tank: Interconnect Defect—The Three Degrees of Separation
Trouble in Your Tank: Things You Can Do for Better Wet Process Control
Trouble in Your Tank: Processes to Support IC Substrates and Advanced Packaging, Part 5
Trouble in Your Tank: Materials for PWB Fabrication—Drillability and Metallization
Trouble in Your Tank: Supporting IC Substrates and Advanced Packaging, Part 5