-
- News
- Books
Featured Books
- pcb007 Magazine
Latest Issues
Current IssueThe Hole Truth: Via Integrity in an HDI World
From the drilled hole to registration across multiple sequential lamination cycles, to the quality of your copper plating, via reliability in an HDI world is becoming an ever-greater challenge. This month we look at “The Hole Truth,” from creating the “perfect” via to how you can assure via quality and reliability, the first time, every time.
In Pursuit of Perfection: Defect Reduction
For bare PCB board fabrication, defect reduction is a critical aspect of a company's bottom line profitability. In this issue, we examine how imaging, etching, and plating processes can provide information and insight into reducing defects and increasing yields.
Voices of the Industry
We take the pulse of the PCB industry by sharing insights from leading fabricators and suppliers in this month's issue. We've gathered their thoughts on the new U.S. administration, spending, the war in Ukraine, and their most pressing needs. It’s an eye-opening and enlightening look behind the curtain.
- Articles
- Columns
- Links
- Media kit
||| MENU - pcb007 Magazine
Thermal Management Materials: Easing the Decision-Making Process
August 2, 2018 | Jade Bridges, ElectrolubeEstimated reading time: 2 minutes
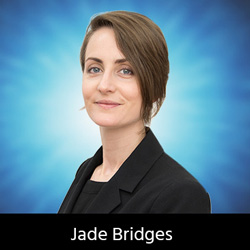
Last year I introduced the subject of thermal management materials—why they are necessary, what materials and methods are available to us, how best to apply them and so on—basing each column on our customers’ frequently asked questions. My colleague, Alistair Little, has discussed resins in greater detail in each of his columns; now, I’ve been invited back to pick up from my last series, this time concentrating more closely on the practicalities of thermal management with this five-point guide to material choice and application.
Understanding the Dimensions: Interface or Gap Filler?
Knowledge of the dimensions of your application is critical to the selection of appropriate thermal management materials. A thermal interface is the space between a component and its heat sink, and the thermally conductive media used in this space are referred to as thermal interface materials (TIMs). This space is usually very small (i.e., on the micron scale). A gap filling application, on the other hand, is more to do with the distance between a component and the metal housing that encloses an electronics assembly and is typically measured in millimetres. In this case, a thermally conductive material is used to help minimise the chances of hot spots within the unit itself while the casing is used as the heat sink.
The difference between a few microns and a few millimetres could be critical to the performance of the thermal medium chosen. For example, if you place a TIM in a gap filling application, it is likely to be unstable in the thicker layer: with vibration, or following a period of temperature cycling, it could easily be displaced. Likewise, if a gap filling material is used in a thermal interface application, it will be very difficult to achieve a thin, even film, creating a higher thermal resistance at the interface and consequently reduced heat transfer efficiency.
Bonding or Non-Bonding: Paste or Pad?
There are many different types of thermally conductive materials, and choosing between them will be dictated by production requirements and application design, as well as critical performance factors that must be achieved. For example, choosing between a bonding or non-bonding material may depend on whether the heat sink needs to be held in place by the interface material, in which case a bonding compound is the better choice. Alternatively, a compound that is fixed (does not move) may be required, in which case it may be appropriate to choose a thermal pad, which has the additional benefit of being pre-cut to size for ease of application. However, both options may result in a thicker interface layer and therefore a higher thermal resistance. The trade-off then comes from the performance requirements of the chosen compounds and understanding the conditions of the application.
To read this entire article, which appeared in the June 2018 issue of Design007 Magazine, click here.
Suggested Items
Symposium Review: Qnity, DuPont, and Insulectro Forge Ahead with Advanced Materials
07/02/2025 | Barb Hockaday, I-Connect007In a dynamic and informative Innovation Symposium hosted live and on Zoom on June 25, 2025, representatives from Qnity (formerly DuPont Electronics), DuPont, and Insulectro discussed the evolving landscape of flexible circuit materials. From strategic corporate changes to cutting-edge polymer films, the session offered deep insight into design challenges, reliability, and next-gen solutions shaping the electronics industry.
Indium Corporation Expert to Present on Automotive and Industrial Solder Bonding Solutions at Global Electronics Association Workshop
06/26/2025 | IndiumIndium Corporation Principal Engineer, Advanced Materials, Andy Mackie, Ph.D., MSc, will deliver a technical presentation on innovative solder bonding solutions for automotive and industrial applications at the Global Electronics A
Gorilla Circuits Elevates PCB Precision with Schmoll’s Optiflex II Alignment System
06/23/2025 | Schmoll MaschinenGorilla Circuits, a leading PCB manufacturer based in Silicon Valley, has enhanced its production capabilities with the addition of Schmoll Maschinen’s Optiflex II Post-Etch Punch system—bringing a new level of precision to multilayer board fabrication.
Day 1: Cutting Edge Insights at the EIPC Summer Conference
06/17/2025 | Pete Starkey, I-Connect007The European Institute for the PCB Community (EIPC) Summer Conference took place this year in Edinburgh, Scotland, June 3-4. This is the second of three articles on the conference. The other two cover the keynote speeches and Day 2 of the technical conference. Below is a recap of the first day’s sessions.
American Made Advocacy: Supporting the Entire PCB Ecosystem—Materials to OEMs
06/17/2025 | Shane Whiteside -- Column: American Made AdvocacyWith the addition of RTX to PCBAA’s membership roster, we now represent the interests of companies in the entire PCB ecosystem. From material providers to OEMs, the insights of our collective members help us educate, advocate, and support legislation and policy favorable to America’s microelectronics manufacturers. The industry veterans who lead these companies provide valuable perspective, and their accumulated wisdom makes us an even stronger association.