-
- News
- Books
Featured Books
- smt007 Magazine
Latest Issues
Current IssueSupply Chain Strategies
A successful brand is built on strong customer relationships—anchored by a well-orchestrated supply chain at its core. This month, we look at how managing your supply chain directly influences customer perception.
What's Your Sweet Spot?
Are you in a niche that’s growing or shrinking? Is it time to reassess and refocus? We spotlight companies thriving by redefining or reinforcing their niche. What are their insights?
Moving Forward With Confidence
In this issue, we focus on sales and quoting, workforce training, new IPC leadership in the U.S. and Canada, the effects of tariffs, CFX standards, and much more—all designed to provide perspective as you move through the cloud bank of today's shifting economic market.
- Articles
- Columns
- Links
- Media kit
||| MENU - smt007 Magazine
Novel Approach to Void Reduction Using Microflux Coated Solder Preforms
July 26, 2018 | By A. Lifton, P. Salerno, J. Sidone and O. Khaselev, Alpha Assembly SolutionsEstimated reading time: 8 minutes
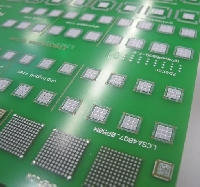
Bottom terminated component packages, such as QFN, are becoming increasingly relevant due to their ability to carry high-power dies in a small form factor. With increasing reliability performance requirements, power management components in packages like QFNs are critical to optimizing thermal and electrical performance. Additionally, low voiding is important for decreasing the current path of the circuit to maximize high-speed and RF performances. The market demand for void reduction under thermal pads of QFN components due to shrinking package sizes and increasing power requirements has generated the need to evaluate key process factors that contribute to voiding to design an optimal solution.
The addition of a micro-fluxed preform in conjunction with a low-voiding solder paste and process know-how is seen to create ideal solder volume with minimal voiding. As IPC 7093 specification acknowledges, one of the key concerns with bottom termination components (BTC) such as QFNs is achieving the solder volume required for a high-reliability solder joint. A multitude of processing factors such as reflow profile, reflow atmosphere, pad finish, and stencil design have been assessed in this study to develop a solution for achieving a high-reliability solder joint with low voiding for QFN packages.
Experimental Procedure
A full factorial DOE was designed based on key factors contributing to voiding under bottom termination components. The use of a solder preform was investigated compared to a solder paste only benchmark sample. The key factors in this DOE were identified and selected by subject matter experts from a leader in semiconductor manufacturing, an OEM of specialized test and measurement equipment for radio communications, and a solder manufacturer.
Figure 1: Image of the PCB test vehicle and some of the components used in this DOE.
A custom single layer 1.6 mm PCB test vehicle was designed specifically for this investigation that encompassed numerous variables that can contribute to voiding in bottom termination components. A single-layer PCB design (Figure 1) was chosen so that other factors (i.e., multilayer board and ground planes) would not influence the key factors being addressed in this study. QFN components of various sizes and pin configurations were among the variables addressed and further defined. In this study, only QFN components were selected (Table 1).
Table 1: Component details.
There were two types of test boards generated: one with an immersion tin (ImmSn) plating, which is widely used in automotive application and another with an immersion silver (ImmAg) plating, which is used in high-reliability and high-power application.
The test board also addressed via design including through hole via, no via, and plugged via configurations under the QFN and LCS components. The through hole via had a 0.3 mm diameter with and 0.5 mm diameter resist on top and bottom. The plugged via maintained the same 0.3 mm diameter hole and depth of 0.4 mm with 0.7 mm diameter resist on top and bottom. Vias were configured in a pattern as indicated in Figure 2.
Figure 2: Via design and configuration on the test vehicle.
The investigation also addressed reflow profile and reflow atmosphere. A low voiding SAC305, type 4 solder paste was used for this study with solidus temperature of 217°C and liquidus temperature 220°C. Thermocouples were strategically placed on the QFN32, and QFN64 component locations on the test vehicle. Proven straight ramp and high soak reflow profiles were evaluated as shown in Figure 3.
Figure 3: Reflow profiles using in this study.
The straight ramp profile increased at a rate of 1°C/s until reaching liquidus temperature of 220°C. The test vehicle was subjected to 65 seconds above liquidus (TAL) with peak temperature on the test vehicle reaching 240°C. The high-soak reflow profile increased temperature at a rate of 1°C/s up to 150°C before slowing to a rate of 0.5°C/s up to 200°C to allow more time for the flux to activate the surfaces.
Table 2: Assemblies' configuration details.
The high-soak profile subjected the test vehicle to 50 seconds above liquidus (220°C) with a peak temperature of 240°C on the test vehicle. Finally, both air and nitrogen reflow atmospheres were evaluated in this investigation to further understand the effect of voiding under bottom termination components.
The focus of the investigation involved the use of the micro-flux coated solder preform to increase solder volume relative to fluxing agent and reduce voiding. The use of a SAC305 microflux coated solder preform in conjunction with paste was benchmarked against a solder paste only test vehicle for each of the configurations summarized in Table 2. Four replicate boards of each iteration were processed to ensure statistically viable data.
Figure 4: Solder paste print configuration. (Examples of window pane solder prints on QFN components used in benchmark samples.)
Close to 2,000 data points were generated combining 54 components on each test vehicle and four replicates of each configuration. The solder paste only benchmark samples were printed in a window pane configuration commonly used in the industry for void reduction and shown in Figure 4.
The design of a solder preforms to allow intimate contact with the thermal pad of the component and increase solder volume played a significant role in the results presented in this investigation. Figure 5 represents an example of the use of solder paste only in window pane format on a QFN where mechanical stack-up issues on the component and reflow characteristics of solder paste make it difficult to achieve good voiding.
Page 1 of 2
Testimonial
"Advertising in PCB007 Magazine has been a great way to showcase our bare board testers to the right audience. The I-Connect007 team makes the process smooth and professional. We’re proud to be featured in such a trusted publication."
Klaus Koziol - atgSuggested Items
Standard of Friendship: Debbie McDade and Symon Franklin Went From Classmates to Colleagues
08/27/2025 | Debbie McDade, Advanced Rework Technology Ltd.As a fairly new IPC Master Trainer, I nervously attended my first IPC committee meeting in 2002 in New Orleans—a 4,600-mile trip from my home in the UK—for the IPC-610 Task Group. With more than 250 members, it was the largest IPC committee at that time.
Flexible Circuit Technologies to Host Free Flex Heater Webinar
08/18/2025 | Flexible Circuit TechnologiesGlobal Supplier of flexible circuits, flex design services, and assembly/box-build services, Flexible Circuit Technology will host their latest webinar, "Thermal Precision Meets Flexibility: The Technology Behind Heater Circuits" on Tuesday, August 26th, 2025 at 11 AM EDT.
A.R.T. Ltd. Nominated in Four Categories at 2025 Instrumentation and Electronics Industry Awards
08/11/2025 | A.R.T. Ltd.Advanced Rework Technology Ltd. (A.R.T. Ltd.), a leading provider of electronics training and consultancy, has been shortlisted in four categories at the 2025 Instrumentation and Electronics Industry Awards, including Industry Personality, Academic Support, Rising Star, and Best Customer Service.
EMC Taiwan Receives IPC-4101 Qualified Products Listing Certification
08/08/2025 | Global Electronics AssociationIPC’s Validation Services Program has awarded an IPC-4101 Qualified Products Listing (QPL) to Elite Materials Co. (EMC), an electronics base material manufacturing company headquartered in Taoyuan City, Taiwan.
Global Excellence in PCB Design: The Global Electronics Association Expands to Italy
08/07/2025 | Global Electronics AssociationIn today's rapidly evolving electronics industry, printed circuit boards (PCBs) serve as the critical backbone influencing the success, reliability, and time-to-market of countless products. Recognizing this essential role, the Global Electronics Association (formerly IPC), a worldwide leader in electronics standards, certification, and education, is now expanding its internationally acclaimed PCB design training to Italy.