-
- News
- Books
Featured Books
- pcb007 Magazine
Latest Issues
Current IssueInventing the Future with SEL
Two years after launching its state-of-the-art PCB facility, SEL shares lessons in vision, execution, and innovation, plus insights from industry icons and technology leaders shaping the future of PCB fabrication.
Sales: From Pitch to PO
From the first cold call to finally receiving that first purchase order, the July PCB007 Magazine breaks down some critical parts of the sales stack. To up your sales game, read on!
The Hole Truth: Via Integrity in an HDI World
From the drilled hole to registration across multiple sequential lamination cycles, to the quality of your copper plating, via reliability in an HDI world is becoming an ever-greater challenge. This month we look at “The Hole Truth,” from creating the “perfect” via to how you can assure via quality and reliability, the first time, every time.
- Articles
- Columns
- Links
- Media kit
||| MENU - pcb007 Magazine
Estimated reading time: 1 minute
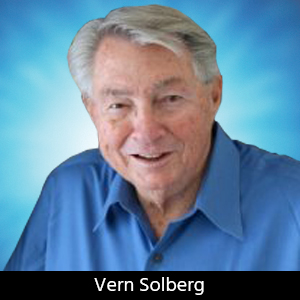
Embedding Components, Part 1
The printed circuit has traditionally served as the platform for mounting and interconnecting active and passive components on the outer surfaces. Companies attempting to improve functionality and minimize space are now considering embedding a broad range of these components within the circuit structure. Both uncased active and passive component elements are candidates for embedding but the decision to embed components within the multilayer circuit structure must be made early in the design process.
Some components are easy candidates for integrating into the substrate while others may involve more complex processes and will be difficult to rationalize. Processes have evolved for embedding and interconnecting a range of common passive components: resistor, capacitor and inductor elements. Embedding formed resistor elements, however, is the most mature and economical process to implement. A formed resistor will have two copper lands with resistance material applied between the lands.
The shape of the resistance material can be a simple rectangle, or a shape designed to maximize resistor element length while minimizing area. In each case, the resistance material must overlap the copper lands.
Formed resistor elements may be furnished as a printed thick-film composition or by employing a chemically etched thin-film process.
- Thick-film resistor materials are formulated to furnish a wide range of primary values. The resistor formulations are based on carbon-filled epoxy chemistry that enables screen printing the elements directly onto pre-patterned terminations on a designated circuit board layer followed by curing the product at temperatures in the range of 150°C. This carbon-filled epoxy thick film (TF) chemistry has been successfully used for a broad number of commercial applications. The process is generally employed where tolerances are less critical. Applications are varied and range from simple discrete potentiometers to pull-up and pull-down resistors.
To read the full version of this article which appeared in the June 2017 issue of The PCB Magazine, click here.
More Columns from Designer's Notebook
Designers Notebook: Basic PCB Planning Criteria—Establishing Design ConstraintsDesigners Notebook: Layer Stackup Planning for RF Circuit Boards
Designers Notebook: Addressing Future Challenges for Designers
Designers Notebook: Impact of Advanced Semiconductor Packaging on PCB Stackup
Designers Notebook: Implementing HDI and UHDI Circuit Board Technology
Designer's Notebook: Heterogeneous Integration and High-density SiP Technologies
Designers Notebook: PCB Design and IPC-CFX for Assembly Automation
Designer’s Notebook: What Designers Need to Know About Manufacturing, Part 2