-
- News
- Books
Featured Books
- smt007 Magazine
Latest Issues
Current IssueSupply Chain Strategies
A successful brand is built on strong customer relationships—anchored by a well-orchestrated supply chain at its core. This month, we look at how managing your supply chain directly influences customer perception.
What's Your Sweet Spot?
Are you in a niche that’s growing or shrinking? Is it time to reassess and refocus? We spotlight companies thriving by redefining or reinforcing their niche. What are their insights?
Moving Forward With Confidence
In this issue, we focus on sales and quoting, workforce training, new IPC leadership in the U.S. and Canada, the effects of tariffs, CFX standards, and much more—all designed to provide perspective as you move through the cloud bank of today's shifting economic market.
- Articles
- Columns
- Links
- Media kit
||| MENU - smt007 Magazine
Estimated reading time: 3 minutes
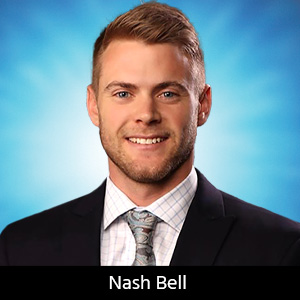
Filling the Gap: Underfill Rework
Ball grid arrays (BGAs), chip-scale packages (CSPs), flip chips, and other component packages on handheld devices are commonplace today in consumer products, including GPS, cellphones, and computers. In addition, these devices are being used in high-end handheld devices, such as military personnel communicators or space data collection devices. Due to handling and the brittle nature of lead-free solders and packaging materials, these handheld products have used underfill to withstand the mechanical shock or impact when the devices are dropped or struck. The underfilling of these component packages to provide a compliant layer between the package and PCB is one method for increasing the reliability of these interconnections. Figure 1 shows a package before being underfilled, and Figure 2 illustrates the underfill removed.
Figure 1: Underfilled device prior to rework.
Underfill is a polymeric material used to fill the gap between the electronic component body and the PCB and encapsulate the solder joints underneath the package. This material enhances the reliability of the component subject to mechanical shocks and impacts by distributing the forces. In addition, it distributes the thermal stresses caused by the coefficient of thermal expansion mismatch between the component and PCB. Typically, underfills have a high glass transition temperature (Tg), a high modulus (E), and a matched coefficient of thermal expansion (CTE) with respect to the solder. Underfill is the “bumper” and distributes the stress more uniformly on the solder joints, thereby increasing the reliability of the solder interconnections.
While there are reworkable underfills in theory, the practical challenges still make reworking an underfilled component very cumbersome and with low resultant yields. The concept of these reworkable underfills is that the material can be thermally decomposed at low temperatures and then removed using various solvents or chemicals without disturbing the solder joints or destroying the substrate or neighboring components. While the marketing material may indicate that the material is reworkable, rework process challenges are numerous.
Figure 2: Device location after component removal and site preparation.
Reworking these underfilled devices creates challenges for the rework technician. One of the biggest issues they face is that the softening point of the underfill is below the solder liquidus temperature. In practice, this means that when the device is reworked at one location on a PCB, a neighboring or mirrored underfilled device may reach the softening point and become plasticized. When this happens, the underfills will exhibit lateral pressure underneath the underfilled component. This presents a problem when the solder reflow temperature is reached on a neighboring underfilled device. This force presses on the reflowed solder, which causes the solder to squirt out from the proper location and solder to be pushed to neighboring non-common solder locations. This phenomenon creates a solder short.
A second challenge in reworking an underfilled component is the tack and adhesive strength of the bond created between the underfilled board and component. This force causes several practical process challenges in the rework process. The first is the force necessary to remove the underfilled device from the board. The force of the pick-up tube nozzle on the rework system will not be enough to pick the reflowed component from the board because the underfill holds it tightly to the board. This means that a twisting and prying force must be applied after the solder liquidus temperature is reached. These forces are such that neighboring devices can be destroyed, the mask can come off of the component or the board, or neighboring devices may even be disturbed in the rework process.
In addition, when the device is finally removed from the board, both the board surface and the bottom of the device may need to have the underfill scraped off its surface. This is done with lateral force and heat, both of which may scratch the mask or lift pads. When cleaning the device location on the PCB of the remnant underfill, solder mask may be also be scratched, pads may be lifted, or neighboring devices may be destroyed.
A third challenge with reworking underfilled components is that while one method or solvent may work on one type of underfill, this same material set process may not work on another board as they are constantly being changed. New generations of packaging materials and technology require new underfills that work with new alloys and solder masks, finer pitches, and ever thinner substrate materials. This will cause the challenges in reworking underfilled components to be ever present.
Rework technicians must take into account a variety of factors when considering whether or not to rework an underfilled component. However, without a full understanding of the underfill characteristics and a process development distinctive to the specific board material, underfill, and board design, expect the outcome to be low yields unless the board was designed with reworkability in mind.
More Columns from Knocking Down the Bone Pile
Knocking Down the Bone Pile: Addressing End-of-life Component Solderability Issues, Part 4Knocking Down the Bone Pile: Tin Whisker Mitigation in Aerospace Applications, Part 3
Knocking Down the Bone Pile: Gold Mitigation for Class 2 Electronics
Knocking Down the Bone Pile: Basics of Component Lead Tinning
Knocking Down the Bone Pile: Package on Package Rework—Skill Required
Knocking Down the Bone Pile: 2023’s Top Challenges in BGA Rework
Knocking Down the Bone Pile: Eliminating Solder Balls in Hand Soldering
Knocking Down the Bone Pile: Opening a Trace on the Surface of a PCB