The Changing Shape of the HDI Market
October 15, 2018 | Roger Massey, ATOTECHEstimated reading time: 1 minute
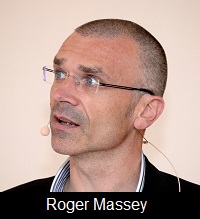
Evolution of the HDI PCB
Since their advent in the early-to-mid-1990s, high-density interconnect (HDI) PCBs have undergone several changes and could now be said to be entering their third evolution. Based on subtractive, or print-and-etch processes, the early HDI panels made use of traditional cores and sequential lamination steps to produce high-end boards with ~60 mm line and space (L/S) capabilities. But most importantly, they relied on microvias to enable their high interconnect density, which, at that time, could not be readily achieved with other technologies.
As board producers improved their processes, HDI board capability also improved; with the release of what we now accept as the smartphone, in the early 2000s, the second generation of HDI panels came into being. While the laser microvias remained, stacked vias began to replace staggered vias, and in combination with the “any layer” or “every layer” build-up technique, these new HDI boards eventually begin to exhibit 40 mm L/S.
Still based on subtractive technologies, this any-layer approach remains the king of the HDI techniques, and it is true to say that the majority of the advanced HDI PCBs that are typical to mobile devices are still produced with this technique. However, in 2017, the HDI market began its next evolution by starting to move away from subtractive processes and into those based on pattern plating. While still reasonably common in Europe and the USA, in Asia HDI has been generally limited to IC substrate manufacturers.
Semi-additive processing (SAP) uses pattern plating processes to realize features
To read the full version of this article which originally appeared in the September 2018 issue of PCB007 Magazine, click here.
Suggested Items
Real Time with... IPC APEX EXPO 2025: Exploring Burkle's Innovations at IPC APEX EXPO 2025
03/27/2025 | Real Time with...IPC APEX EXPOBurkle North America's Andy Turner shares insights from the show, highlighting the excitement surrounding the event and Burkle North America's growth potential. He invited attendees to their booth to interact with the InfoCube, a cutting-edge touchscreen showcasing Burkle's diverse product offerings.
All Flex Solutions Upgrades Lamination Layup
01/17/2025 | All Flex SolutionsAll Flex Solutions has invested in Ulrich Rotte lamination layup stations in their rigid flex layup area. The Ulrich Rotte stations automate the layup process by handling the lamination plates, which are heavy, and sequencing the layup process for the operators.
Effects of Advanced Packaging and Stackup Design
12/26/2024 | I-Connect007 Editorial TeamKris Moyer teaches several PCB design classes for IPC and Sacramento State, including advanced PCB design. His advanced design classes take on some really interesting topics, including the impact of a designer’s choice of advanced packaging upon the design of the layer stackup. Kris shares his thoughts on the relationship between packaging and stackup, what PCB designers need to know, and why he believes, “The rules we used to live by are no longer valid.”
Partial HDI: A Complete Solution
10/10/2024 | I-Connect007 Editorial TeamWe recently spoke with IPC instructor Kris Moyer about partial HDI, a process that’s recently been growing in popularity. Partial HDI allows designers to escape route out from tight-pitch BGAs on one layer, where a mechanically drilled plated through-hole is not an option, while avoiding the complexity and expense of sequential lamination cycles. As Kris explains, this process doesn’t add much to the cost, and it’s fairly straightforward. But there are some competing signal integrity and fabrication requirements to contend with. We asked Kris to walk us through this process.
TTM Selects Lamination Press From Lauffer and all4-PCB for New Syracuse Facility
09/10/2024 | all4-PCBall4-PCB is pleased to announce that TTM Technologies has chosen Lauffer GmbH & Co., Germany to supply the automated multilayer press system for TTM’s new facility in Syrcause, New York. The system will include hot and cold presses, storage towers, lay-up and depinning stations.