-
-
News
News Highlights
- Books
Featured Books
- smt007 Magazine
Latest Issues
Current IssueWhat's Your Sweet Spot?
Are you in a niche that’s growing or shrinking? Is it time to reassess and refocus? We spotlight companies thriving by redefining or reinforcing their niche. What are their insights?
Moving Forward With Confidence
In this issue, we focus on sales and quoting, workforce training, new IPC leadership in the U.S. and Canada, the effects of tariffs, CFX standards, and much more—all designed to provide perspective as you move through the cloud bank of today's shifting economic market.
Intelligent Test and Inspection
Are you ready to explore the cutting-edge advancements shaping the electronics manufacturing industry? The May 2025 issue of SMT007 Magazine is packed with insights, innovations, and expert perspectives that you won’t want to miss.
- Articles
- Columns
- Links
- Media kit
||| MENU - smt007 Magazine
Investigation on the Assembly Process for m03015 and a Brief Look at m0201 Components
November 14, 2018 | David Geiger, Robert Pennings, and Jane Feng, FlexEstimated reading time: 7 minutes
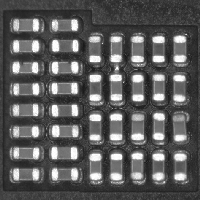
Over the years, components have continued to reduce in size. The latest components—m03015 and m0201—are starting to appear in the markets. The m03015 is the metric designation for the EIA 009005 and m0201 is the metric designation for the EIA 008004.
These types of components will be used in module assembly, which would include items for smart wearables where miniaturization is required for higher functional densities. SiPs—the latest term for these modules—are already seen in wearables such as watches, wristbands, and other devices. These parts will not be mainstream for some time because the 01005 components have only been used for a small portion of products today.
Figure 1 shows how the components have reduced in size over the years.
Figure 1: Component sizes timeline.
Test Vehicle
For this testing, Flex's miniaturized test vehicle was used. This board has many features, including package-on-package (PoP), 0.3-mm pitch chip-scale package (CSP), 01005, 0201, high-density spacing, solder flip chip down to 180-um pitch, and others. The bare board can be seen in Figure 2. The pads for m03015 were placed on the boards in anticipation of these parts about five years ago.
Figure 2: Miniaturized test vehicle.
The land pattern used has the following dimensions: 0.15 x 0.15 mm copper pad with a gap of 0.076 mm. This pad will have a toe of approximately 0.038 mm based on the nominal component design. Figure 3 shows the schematic of the pad design. The pad design is slightly larger than different designs seen in other studies. The spacing between the copper depends on the panel location; the pad spacing is 200, 150, and 100 μm. The board is 130 x 77 mm and 1 mm thick with an organic solderability preservative (OSP) surface finish.
Figure 3: Pad design.
This pad was designed to help printability, and would not be the best for miniaturization; this is being done with a new test board that will be discussed briefly at the end of this article. For a 76-µm stencil, the area ratio (AR) is about 0.49; for a 50-µm stencil, the AR is approximately 0.75.
Process Materials and Parameters
For this testing, it was decided to use a 50-µm fine-grain stainless-steel stencil with 150 x 150 µm apertures. The stencil was also nanocoated to help provide the best release possible. A dedicated support fixture was used for the print process. The equipment being used is typically in a standard SMT manufacturing line. The pick-and-place machine had all the necessary upgrades (e.g., camera, software, nozzles) required to move m03015 components. The equipment was verified before running the actual samples. For reflow, we created a typical profile and ran in a nitrogen environment with 200–600ppm of O2 during processing. Figure 4 shows the profile used.
Figure 4: Reflow profile.
The solder paste material used was one that has been used in volume production—the only difference being that a Type 5 particle size was evaluated. This was a low-residue flux system with halogen-free, ROL0 (RO stands for rosin, L for low-activity, and zero for no detectible halides) materials. A Type 4 material was trialed, but the decision was made to use the Type 5 for this study. Figure 5 shows print comparisons.
Figure 5: Type 4 (L) and Type 5 (R) after printing.
Page 1 of 3
Suggested Items
Silicon Mountain Contract Services Enhances SMT Capabilities with New HELLER Reflow Oven
07/17/2025 | Silicon Mountain Contract ServicesSilicon Mountain Contract Services, a leading provider of custom electronics manufacturing solutions, is proud to announce a significant upgrade to its SMT production capability with the addition of a HELLER 2043 MK5 10‑zone reflow oven to its Nampa facility.
Knocking Down the Bone Pile: Addressing End-of-life Component Solderability Issues, Part 4
07/16/2025 | Nash Bell -- Column: Knocking Down the Bone PileIn 1983, the Department of Defense identified that over 40% of military electronic system failures in the field were electrical, with approximately 50% attributed to poor solder connections. Investigations revealed that plated finishes, typically nickel or tin, were porous and non-intermetallic.
SHENMAO Strengthens Semiconductor Capabilities with Acquisition of PMTC
07/10/2025 | SHENMAOSHENMAO America, Inc. has announced the acquisition of Profound Material Technology Co., Ltd. (PMTC), a premier Taiwan-based manufacturer of high-performance solder balls for semiconductor packaging.
KYZEN to Highlight Understencil and PCB Cleaners at SMTA Querétaro Expo and Tech Forum
07/09/2025 | KYZEN'KYZEN, the global leader in innovative environmentally responsible cleaning chemistries, will exhibit at the SMTA Querétaro Expo & Tech Forum, scheduled to take place Thursday, July 24, at Centro de Congresos y Teatro Metropolitano de Querétaro.
Driving Innovation: Direct Imaging vs. Conventional Exposure
07/01/2025 | Simon Khesin -- Column: Driving InnovationMy first camera used Kodak film. I even experimented with developing photos in the bathroom, though I usually dropped the film off at a Kodak center and received the prints two weeks later, only to discover that some images were out of focus or poorly framed. Today, every smartphone contains a high-quality camera capable of producing stunning images instantly.