-
- News
- Books
Featured Books
- smt007 Magazine
Latest Issues
Current IssueIntelligent Test and Inspection
Are you ready to explore the cutting-edge advancements shaping the electronics manufacturing industry? The May 2025 issue of SMT007 Magazine is packed with insights, innovations, and expert perspectives that you won’t want to miss.
Do You Have X-ray Vision?
Has X-ray’s time finally come in electronics manufacturing? Join us in this issue of SMT007 Magazine, where we answer this question and others to bring more efficiency to your bottom line.
IPC APEX EXPO 2025: A Preview
It’s that time again. If you’re going to Anaheim for IPC APEX EXPO 2025, we’ll see you there. In the meantime, consider this issue of SMT007 Magazine to be your golden ticket to planning the show.
- Articles
- Columns
Search Console
- Links
- Media kit
||| MENU - smt007 Magazine
Investigation on the Assembly Process for m03015 and a Brief Look at m0201 Components
November 14, 2018 | David Geiger, Robert Pennings, and Jane Feng, FlexEstimated reading time: 7 minutes
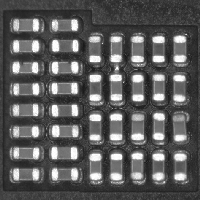
Over the years, components have continued to reduce in size. The latest components—m03015 and m0201—are starting to appear in the markets. The m03015 is the metric designation for the EIA 009005 and m0201 is the metric designation for the EIA 008004.
These types of components will be used in module assembly, which would include items for smart wearables where miniaturization is required for higher functional densities. SiPs—the latest term for these modules—are already seen in wearables such as watches, wristbands, and other devices. These parts will not be mainstream for some time because the 01005 components have only been used for a small portion of products today.
Figure 1 shows how the components have reduced in size over the years.
Figure 1: Component sizes timeline.
Test Vehicle
For this testing, Flex's miniaturized test vehicle was used. This board has many features, including package-on-package (PoP), 0.3-mm pitch chip-scale package (CSP), 01005, 0201, high-density spacing, solder flip chip down to 180-um pitch, and others. The bare board can be seen in Figure 2. The pads for m03015 were placed on the boards in anticipation of these parts about five years ago.
Figure 2: Miniaturized test vehicle.
The land pattern used has the following dimensions: 0.15 x 0.15 mm copper pad with a gap of 0.076 mm. This pad will have a toe of approximately 0.038 mm based on the nominal component design. Figure 3 shows the schematic of the pad design. The pad design is slightly larger than different designs seen in other studies. The spacing between the copper depends on the panel location; the pad spacing is 200, 150, and 100 μm. The board is 130 x 77 mm and 1 mm thick with an organic solderability preservative (OSP) surface finish.
Figure 3: Pad design.
This pad was designed to help printability, and would not be the best for miniaturization; this is being done with a new test board that will be discussed briefly at the end of this article. For a 76-µm stencil, the area ratio (AR) is about 0.49; for a 50-µm stencil, the AR is approximately 0.75.
Process Materials and Parameters
For this testing, it was decided to use a 50-µm fine-grain stainless-steel stencil with 150 x 150 µm apertures. The stencil was also nanocoated to help provide the best release possible. A dedicated support fixture was used for the print process. The equipment being used is typically in a standard SMT manufacturing line. The pick-and-place machine had all the necessary upgrades (e.g., camera, software, nozzles) required to move m03015 components. The equipment was verified before running the actual samples. For reflow, we created a typical profile and ran in a nitrogen environment with 200–600ppm of O2 during processing. Figure 4 shows the profile used.
Figure 4: Reflow profile.
The solder paste material used was one that has been used in volume production—the only difference being that a Type 5 particle size was evaluated. This was a low-residue flux system with halogen-free, ROL0 (RO stands for rosin, L for low-activity, and zero for no detectible halides) materials. A Type 4 material was trialed, but the decision was made to use the Type 5 for this study. Figure 5 shows print comparisons.
Figure 5: Type 4 (L) and Type 5 (R) after printing.
Page 1 of 3
Suggested Items
Indium’s Karthik Vijay to Present on Dual Alloy Solder Paste Systems at SMTA’s Electronics in Harsh Environments Conference
05/06/2025 | Indium CorporationIndium Corporation Technical Manager, Europe, Africa, and the Middle East Karthik Vijay will deliver a technical presentation on dual alloy solder paste systems at SMTA’s Electronics in Harsh Environments Conference, May 20-22 in Amsterdam, Netherlands.
SolderKing Achieves the Prestigious King’s Award for Enterprise in International Trade
05/06/2025 | SolderKingSolderKing Assembly Materials Ltd, a leading British manufacturer of high-performance soldering materials and consumables, has been honoured with a King’s Award for Enterprise, one of the UK’s most respected business honours.
Knocking Down the Bone Pile: Gold Mitigation for Class 2 Electronics
05/07/2025 | Nash Bell -- Column: Knocking Down the Bone PileIn electronic assemblies, the integrity of connections between components is paramount for ensuring reliability and performance. Gold embrittlement and dissolution are two critical phenomena that can compromise this integrity. Gold embrittlement occurs when gold diffuses into solder joints or alloys, resulting in mechanical brittleness and an increased susceptibility to cracking. Conversely, gold dissolution involves the melting away of gold into solder or metal matrices, potentially altering the electrical and mechanical properties of the joint.
'Chill Out' with TopLine’s President Martin Hart to Discuss Cold Electronics at SPWG 2025
05/02/2025 | TopLineBraided Solder Columns can withstand the rigors of deep space cold and cryogenic environments, and represent a robust new solution to challenges facing next generation large packages in electronics assembly.
BEST Inc. Reports Record Demand for EZReball BGA Reballing Process
05/01/2025 | BEST Inc.BEST Inc., a leader in electronic component services, is pleased to announce they are experiencing record demand for their EZReball™ BGA reballing process which greatly simplifies the reballing of ball grid array (BGA) and chip scale package (CSP) devices.