-
- News
- Books
Featured Books
- smt007 Magazine
Latest Issues
Current IssueIntelligent Test and Inspection
Are you ready to explore the cutting-edge advancements shaping the electronics manufacturing industry? The May 2025 issue of SMT007 Magazine is packed with insights, innovations, and expert perspectives that you won’t want to miss.
Do You Have X-ray Vision?
Has X-ray’s time finally come in electronics manufacturing? Join us in this issue of SMT007 Magazine, where we answer this question and others to bring more efficiency to your bottom line.
IPC APEX EXPO 2025: A Preview
It’s that time again. If you’re going to Anaheim for IPC APEX EXPO 2025, we’ll see you there. In the meantime, consider this issue of SMT007 Magazine to be your golden ticket to planning the show.
- Articles
- Columns
Search Console
- Links
- Media kit
||| MENU - smt007 Magazine
Electrolube on Managing Thermal Interfaces and Conformal Coatings
December 3, 2018 | Pete Starkey, I-Connect007Estimated reading time: 7 minutes
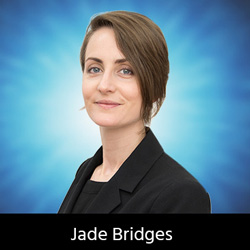
While visiting Electrolube at the electronica show in Munich, Germany, I was delighted to have the opportunity to talk to Jade Bridges, global technical support manager, about how to manage thermal interfaces for maximum heat transfer efficiency. She also provides an update on conformal coatings.
Pete Starkey: Can you tell me about recent developments in your thermal management materials? What's the market looking to achieve, and what's been coming out of your development labs to help them achieve it?
Jade Bridges: We've been working for a good while and have concentrated a lot of resources into extending our thermal management range. We've seen massive changes in the market with new applications coming from far and wide.
Starkey: Can you give me some examples?
Bridges: The LED industry is one we've focused on a lot where efficiency is key there. The automotive industry is another important area—basically, anywhere they need good heat dissipation. Electric vehicles are a key example in the automotive industry, as well as battery packs, etc.
We've looked at the requirements of these industries and how they differ from what we were doing 10, 15, and 20 years ago. It's a growing market, and the range of applications is expanding, so we decided to invest in a thermal management specialist team that solely concentrates on that area. We have chemists developing new technologies and making our current technologies even better. That's the basis of what that team does, which has resulted in a massive expansion of our range over the past four years not just in current product technology, but in new technology like our phase-change materials (PCMs), for example.
Starkey: Can you explain a little about what PCMs are and how they work? What are the benefits?
Bridges: Certainly. You apply PCMs to the substrate, and when it reaches its softening temperature, then it will “relax.” There's the concept that a PCM will be solid at one temperature and liquid at another, which has made people a little bit concerned that they will be subject to pump-out with changes in thermal expansion, but the reality is that it just softens. It’s a solid material once it’s applied to the substrate, and then around 50°C—depending on the exact softening temperature—it will soften slightly, and that allows everything to conform.
Starkey: So, you get better thermal contact with the device that you're heat-sinking?
Bridges: Yes, any remaining gaps or little air pockets due to unevenness of the surfaces are filled in.
Starkey: How are they applied?
Bridges: Our PCMs are very easy to apply via a stencil or a screen. You just put them onto the surface and allow the solvent to evaporate before putting on the mating interface.
Starkey: What sort of thicknesses do you apply?
Bridges: It’s very similar to thermal paste. Typically, 50 microns up to slightly higher, such as 100–150 microns. Obviously, that's controlled by the screen mesh or stencil design. The reality is that we get a much more stable product without pump-out at that same thickness as a thermal paste. Overall, that means the thermal resistance is much lower.
Starkey: What sort of thermal conductivity do you achieve?
Bridges: We have two products that we're promoting at the show—TPM350 and TPM550—which are 3.5 and 5.5 watts per metre Kelvin. We've also increased our range of what we offer in terms of thermal conductivity. That's our key focus at the moment, but we have a wide range of other thermal management products as well. We're expanding in all avenues.
Starkey: Is there anything further we need to talk about regarding thermal management materials?
Bridges: If anyone wants to see the products—particularly the PCMs—then we can do some demonstrations. That's something we're trying to focus on this time—allowing people to see the products in action and gain a better idea of what they are.
Starkey: I think your basic explanation removes a lot of mystery about PCMs, which is great. Many thanks. Changing the subject now, what is the industry asking for in conformal coating materials?
Bridges: The situation in conformal coatings is very similar to what's happening in thermal management—it’s another fast-growing market with an increasing variety of applications. Different industries are realizing that they need some level of protection because of warranties on electrical products and the importance that electronics continue to have in our everyday lives. As a result, that means harsher conditions, a longer working life, more thermal cycles or thermal shock conditions, and with conformal coatings—as in many other industries—it’s high throughput.
Starkey: What are the preferred chemistries for conformal coatings presently?
Bridges: There are lots of different chemistries available, and what people realize now is that you don't have to stick with an exact chemistry type to get what you need. The market is evolving, and there are hybrid chemistries out there. The UV-cure coating market is another example, but that's also something we've pushed. Traditional UV-cure coatings will be a dual-cure system of UV cure and moisture, possibly taking over seven days to reach full cure. It requires a hybrid chemistry within the system for that to work.
What we've developed and what we're demonstrating at electronica is 2K850—a two-component UV-cure coating. Since it’s two component, you don’t have issues with shadow areas not curing within a certain amount of time, which allows customers to control that process fully. When you put 2K850 through the UV-cure oven, everything that is exposed to UV will cure immediately. Anything that's not exposed to UV in the two-component system sets into action and everything will be cured within 16 to 24 hours. That's a massive improvement on the current situation.
Starkey: Is that at an ambient temperature? Will the cure carry on?
Bridges: Yes, it cures at ambient temperature, and if customers need to speed that up, it will heat cure as well. It’s a very flexible system because it’s 2K technology, which we've been pushing for a number of years now. We are demonstrating the process of 2K850 at our conformal coatings stand so that people can see how it sprays and applies, how thick it is, how it protects, and then moving onto the UV cure process, how to inspect it.
Starkey: Does the UV cure really just set it in place and you rely on the chemistry of the two pack to bring about the cure, or is it more subtle than that?
Bridges: In a way, yes, it’s a very clever technology. By passing it through UV, it will cure as you would normally expect it to. Mixing the two components together is what sets the product in other areas.
Starkey: You mentioned spraying for application methods.
Bridges: Yes, spray—it’s like any other conformal coating. You do have a different applicator because you're mixing the two components before spraying.
Starkey: Do you mix them at the point of application?
Bridges: Yes, it’s a two-component spray head with pumps that feed into a static mixer. Then, the static mixer goes through an atomizing spray cap, which allows the product to be applied to the board, and you program it in as normal.
Page 1 of 2
Suggested Items
Laird Thermal Systems Unveils New Identity
05/05/2025 | Laird Thermal SystemsLaird Thermal Systems, a global leader in active thermal management solutions with more than 60 years of application expertise, today announced its rebrand to Tark Thermal Solutions.
Ansys Strengthens Collaboration with TSMC on Advanced Node Processes Certification and 3D-IC Multiphysics Design Solutions
04/24/2025 | PRNewswireThrough continued collaboration with TSMC, Ansys announced enhanced AI-assisted workflows for radio frequency (RF) design migration and photonic integrated circuits (PICs), and new certifications for its semiconductor solutions. Together,
Explore Thermal Management Solutions in Latest Podcast Series—New Episode Now Available
04/30/2025 | I-Connect007I-Connect007 is excited to share the latest episode in our new podcast series! In this episode, Ryan returns to discuss practical strategies for managing heat, starting early in the design planning and specification phases. After all, prevention means there’s less to mitigate later.
Google Signs Taiwan’s First Corporate Geothermal Energy Deal in Asia-Pacific
04/23/2025 | I-Connect007 Editorial TeamGoogle announced that it has entered Taiwan’s first corporate geothermal power purchase agreement (PPA) with Baseload Capital to expand access to around-the-clock clean energy in the Asia-Pacific region and beyond.
Laird Thermal Systems Announces Max Kley as New CEO
04/18/2025 | Laird Thermal SystemsLaird Thermal Systems (LTS) is pleased to announce the appointment of Dr. Max Kley as its new Chief Executive Officer, effective April 1, 2025. Max Kley brings a wealth of international leadership experience to LTS, having successfully led and developed businesses across the USA, Europe, and Asia.