-
- News
- Books
Featured Books
- smt007 Magazine
Latest Issues
Current IssueSpotlight on India
We invite you on a virtual tour of India’s thriving ecosystem, guided by the Global Electronics Association’s India office staff, who share their insights into the region’s growth and opportunities.
Supply Chain Strategies
A successful brand is built on strong customer relationships—anchored by a well-orchestrated supply chain at its core. This month, we look at how managing your supply chain directly influences customer perception.
What's Your Sweet Spot?
Are you in a niche that’s growing or shrinking? Is it time to reassess and refocus? We spotlight companies thriving by redefining or reinforcing their niche. What are their insights?
- Articles
- Columns
- Links
- Media kit
||| MENU - smt007 Magazine
Dymax Introduces BlueWave MX-275
January 7, 2019 | DymaxEstimated reading time: Less than a minute
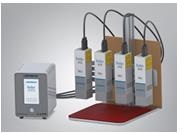
Dymax introduces the BlueWave MX-275 high-intensity flood-curing system. Its light energy is delivered in a line pattern instead of the traditional round spot or rectangular flood-curing patterns, to allow for consist curing of batches of parts for maximum productivity.
The system utilizes BlueWave RediCure, PrimeCure, or VisiCure emitters (365, 385, or 405 nm) to quickly cure light-curable materials. A single emitter provides a 5 mm x 50 mm curing area, but when paired with a multichannel controller, up to four emitters can be used to produce a curing area as large as 5 mm x 200 mm. It offers very high uniformity across the entire cure area and multiple emitters can be positioned to assure uniform curing across the entire multiple-emitter curing area.
This system’s wavelength flexibility (365, 385, and 405 nm) allows co-optimization of adhesive and curing system for optimal cure results. As with other emitters from the MX product family, the BlueWave MX-275 can be set up as a bench-top unit, on an array stand to create extended line patterns, or installed on automated curing processing equipment for maximum flexibility. Emitters can also be paired with MX-series single or multichannel controllers.
Testimonial
"The I-Connect007 team is outstanding—kind, responsive, and a true marketing partner. Their design team created fresh, eye-catching ads, and their editorial support polished our content to let our brand shine. Thank you all! "
Sweeney Ng - CEE PCBSuggested Items
AV Delivers First Two Multi-Purpose High Energy Laser Systems to U.S. Army
09/04/2025 | BUSINESS WIREAeroVironment, Inc. (AV) announced the successful delivery of the first two mobile counter-unmanned aircraft system (C-UAS) prototype Laser Weapon System (LWS) to the U.S. Army Rapid Capabilities and Critical Technologies Office (RCCTO) as part of the first increment of the Army Multi-Purpose High Energy Laser (AMP-HEL) prototyping effort.
New Podcast Episode Drop: MKS’ Atotech’s Role in Optimize the Interconnect
09/04/2025 | I-Connect007In this episode of On the Line With…, host Nolan Johnson sits down with Patrick Brooks, MKS' Atotech's Global Product Director, EL Systems, to discuss the critical role that wet processes play alongside laser systems in advancing the Optimize the InterconnectSM initiative. Brooks points to Bondfilm as a key example—a specialized coating that enables CO₂ lasers to ablate more effectively than ever before.
UHDI Fundamentals: UHDI Technology and Industry 4.0
09/03/2025 | Anaya Vardya, American Standard CircuitsUltra high density interconnect (UHDI) technology is rapidly transforming how smart systems are designed and deployed in the context of Industry 4.0. With its capacity to support highly miniaturized, high-performance, and densely packed electronics, UHDI is a critical enabler of the smart, connected, and automated industrial future. Here, I’ll explore the synergy between UHDI and Industry 4.0 technologies, highlighting applications, benefits, and future directions.
What EMS Firms Want From Their Software—and What They Get
09/03/2025 | Thiago Guimaraes, Global Electronics AssociationLast November, the Global Electronics Association [as IPC] surveyed EMS and OEM companies to better understand the software tools driving their operations and uncover trends in adoption, satisfaction, and challenges. The survey assessed software tools across critical functions, including ERP, MES, PLM, QMS, LMS, quoting systems, and CRM. Participants shared insights on tool adoption, satisfaction, and selection priorities.
BAE Systems Delivers 1,000th THAAD Seeker for Ballistic Missile Defense Program
09/01/2025 | BAE SystemsBAE Systems recently delivered its 1,000th infrared seeker to Lockheed Martin for integration on the Terminal High Altitude Area Defense (THAAD) interceptor missile, achieving a major production milestone.