-
- News
- Books
Featured Books
- smt007 Magazine
Latest Issues
Current IssueSupply Chain Strategies
A successful brand is built on strong customer relationships—anchored by a well-orchestrated supply chain at its core. This month, we look at how managing your supply chain directly influences customer perception.
What's Your Sweet Spot?
Are you in a niche that’s growing or shrinking? Is it time to reassess and refocus? We spotlight companies thriving by redefining or reinforcing their niche. What are their insights?
Moving Forward With Confidence
In this issue, we focus on sales and quoting, workforce training, new IPC leadership in the U.S. and Canada, the effects of tariffs, CFX standards, and much more—all designed to provide perspective as you move through the cloud bank of today's shifting economic market.
- Articles
- Columns
- Links
- Media kit
||| MENU - smt007 Magazine
Estimated reading time: 3 minutes
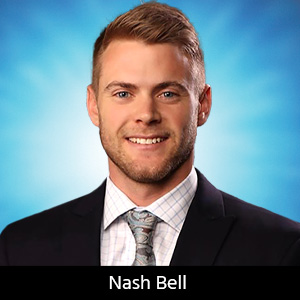
Inspection of BGAs After Rework
After removing and replacing a ball grid array (BGA), the acceptability of the interconnection of the solder balls to the PCB should be assured. This assurance and the criteria for that assurance are the customer’s outgoing inspection criteria. These acceptance criteria are outlined in a very general fashion in the latest version of IPC-A-610—Acceptability of Electronic Assemblies, Revision G as of this writing—based on the class of the assembly. Other approaches to the acceptance criteria can be found by augmenting the requirements of 610 guidelines with your own criteria based on testing outcomes or the suggestions found in IPC-7095—Design and Assembly Process Implementation for BGAs, currently at Revision C.
Figure 1: BGA X-ray image for inspection post-rework.
Most of the requirements for the inspection of BGAs are based on IPC-A-610 standards. The current standard does not require X-ray inspection. However, process validation can be used in lieu of X-ray inspection provided there is objective evidence of compliance. When visual inspection is done on a BGA post-rework, and the requirements of IPC-A-610 are the basis for inspection, the proper inspection magnification is taken from the latest IPC-A-610 standard. Solder terminations from the outside perimeter need to be visually inspected whenever practical. By looking at the ball-board or ball-package interface, the degree of wetting, the amount of remnant flux residue or any obvious cracks, shorting or other anomalies can be noted. In addition, visual inspection will usually determine the proper pin “1” alignment of the component body.
Other visual indications include missing solder balls, minimum electrical clearance distance to neighboring conductors, head-in-pillow defects, solder bridging, fractured solder connections, improper wetting, or lack of evidence of solder coalescing (if a paste print-based rework process is used). If X-ray inspection is utilized for BGA inspection, a couple of the criteria to look for during BGA X-ray inspecting taking place need to be reviewed.
If X-ray inspection is used post-BGA rework, then there are a couple of criteria called for in the IPC-A-610 standard. For collapsing (typically tin-lead alloy) solder balls, the maximum allowable voiding allowable is 30% of the inspection area. What is excluded from this amount are plating process-related voids, which should be established between the end customer and the company performing the rework. For noncollapsing balls, these voiding criteria are not established in IPC-A-610.
As a reminder, the BGA may need to be reworked for a variety of reasons. Some of the reasons for BGA rework include a defective component, an upgrade in memory size, or a change in a revision of the part. After removal and replacement of the component, inspection of the newly placed component—whether it is a new component or a reballed component—needs to take place to ensure the replacement components’ interconnections.
X-ray inspection of BGAs post rework (Figure 1) require inspection time to determine the acceptability of the solder interconnection. A “scan” of the BGA area from a far enough field of view to see the entire array is a good way to begin the BGA post rework inspection process. After this far field of view scan, the technician should zoom in to get a good visual indication at close range of the ball shape, size, and consistency.
Figure 2: Automated BGA X-ray inspection post-rework can catch a missing ball.
Starting at one corner, the technician manipulates the X-ray back and forth over the array until all of the balls have been scanned. More advanced X-ray systems can be programmed with acceptance/reject criteria to more fully automate this process. More automated X-ray systems can scan for concentricity (i.e., ball shape), ball diameter, pitch, and other parameters (Figure 2).
Summary
Many of today’s designs include a BGA or area array package. When this component needs to be swapped out for rework, the inspection of the replaced BGA may include both visual as well as X-ray inspection. Following the customer agreed-upon inspection criteria, there may be visual, basic X-ray inspection, or more advanced automated inspection of the reworked location may need to be made to make a go/no-go determination of the interconnection.
Bob Wettermann is the principal of BEST Inc., a contract rework and repair facility in Chicago. To read past columns or contact Wettermann, click here.
More Columns from Knocking Down the Bone Pile
Knocking Down the Bone Pile: Addressing End-of-life Component Solderability Issues, Part 4Knocking Down the Bone Pile: Tin Whisker Mitigation in Aerospace Applications, Part 3
Knocking Down the Bone Pile: Gold Mitigation for Class 2 Electronics
Knocking Down the Bone Pile: Basics of Component Lead Tinning
Knocking Down the Bone Pile: Package on Package Rework—Skill Required
Knocking Down the Bone Pile: 2023’s Top Challenges in BGA Rework
Knocking Down the Bone Pile: Eliminating Solder Balls in Hand Soldering
Knocking Down the Bone Pile: Opening a Trace on the Surface of a PCB