-
- News
- Books
Featured Books
- design007 Magazine
Latest Issues
Current IssueProper Floor Planning
Floor planning decisions can make or break performance, manufacturability, and timelines. This month’s contributors weigh in with their best practices for proper floor planning and specific strategies to get it right.
Showing Some Constraint
A strong design constraint strategy carefully balances a wide range of electrical and manufacturing trade-offs. This month, we explore the key requirements, common challenges, and best practices behind building an effective constraint strategy.
All About That Route
Most designers favor manual routing, but today's interactive autorouters may be changing designers' minds by allowing users more direct control. In this issue, our expert contributors discuss a variety of manual and autorouting strategies.
- Articles
- Columns
- Links
- Media kit
||| MENU - design007 Magazine
Estimated reading time: 1 minute
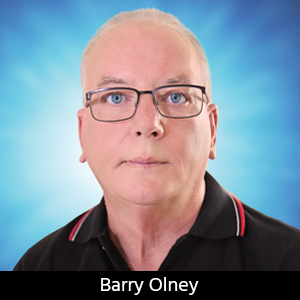
Beyond Design: Not All PCB Substrates Are Created Equal
PCB substrates are all around us in every gadget we use whether it’s a computer, smartphone, or simple child’s toy. The substrate may be rigid or flexible, or a combination of both. It is a carrier for the electronic devices and the signal and power interconnects and is usually planar in structure with conductors separated by insulating dielectric materials. However, each product has a specific performance requirement and may need a distinct type of substrate to comply with the product’s specifications—particularly for high-speed designs.
Because the impedance of transmission lines is a function of substrate dielectric constant, essential requirements for a multilayer PCB dielectric material is extremely tight tolerance and consistency in the dielectric constant and thermal coefficient of dielectric constant (the amount of change in the dielectric constant as a function of temperature). In addition, the coefficient of thermal expansion (CTE)—especially in the z-axis (through the thickness of the material)—is of particular importance in multilayer designs because plated through-holes (PTHs) are used to make connections between different layers of the stackup. The CTE is a yardstick for expected PTH barrel reliability.
A wire suspended in free air has impedance in the order of 330 ohms. This impedance may have been viable in the old vacuum tube days but is not a good starting point for any digital design. A twisted pair cable with an outer shield has 100 ohms differential impedance. A coax cable with an inner wire surrounded by dielectric material and an outer shield is typically 50–75 ohms. As we add a coupled return path close to the signal conductor in the presence of a dielectric, the impedance reduces.
Typically, for a digital design, a characteristic impedance of 40–60 ohms and differential impedance of 80–120 ohms are used. This becomes more important as the edge rates become faster. Also, different technologies have their specific requirements. For instance, USB requires 90 ohms differential impedance, and DDR3/4 require 40/80 ohms single-ended/differential impedance. For perfect energy transfer, the impedance of the driver must match the impedance of the transmission line. A good transmission line is one that has constant impedance along the entire length of the line so that there are no mismatches resulting in reflections.
To read this entire column, which appeared in the February 2019 issue of Design007 Magazine, click here.
More Columns from Beyond Design
Beyond Design: Effective Floor Planning StrategiesBeyond Design: Refining Design Constraints
Beyond Design: The Metamorphosis of the PCB Router
Beyond Design: Radiation and Interference Coupling
Beyond Design: Key SI Considerations for High-speed PCB Design
Beyond Design: Electro-optical Circuit Boards
Beyond Design: AI-driven Inverse Stackup Optimization
Beyond Design: High-speed Rules of Thumb