-
-
News
News Highlights
- Books
Featured Books
- smt007 Magazine
Latest Issues
Current IssueWhat's Your Sweet Spot?
Are you in a niche that’s growing or shrinking? Is it time to reassess and refocus? We spotlight companies thriving by redefining or reinforcing their niche. What are their insights?
Moving Forward With Confidence
In this issue, we focus on sales and quoting, workforce training, new IPC leadership in the U.S. and Canada, the effects of tariffs, CFX standards, and much more—all designed to provide perspective as you move through the cloud bank of today's shifting economic market.
Intelligent Test and Inspection
Are you ready to explore the cutting-edge advancements shaping the electronics manufacturing industry? The May 2025 issue of SMT007 Magazine is packed with insights, innovations, and expert perspectives that you won’t want to miss.
- Articles
- Columns
- Links
- Media kit
||| MENU - smt007 Magazine
Tips & Tricks: Wave Solder Bridging
April 3, 2019 | Jason Fullerton, MacDermid Alpha Electronics SolutionsEstimated reading time: 1 minute
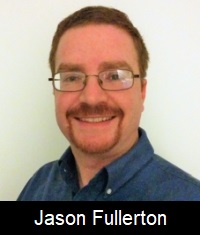
Wave solder bridging is the most difficult defect to troubleshoot because it has a number of potential causes. The key is to understand the role of flux during wave contact—reducing the surface tension of the solder to reduce the tendency to bridge between pins as the board leaves the wave. Bridging occurs when the flux has been chemically depleted before exiting the wave. This can be a function of the flux and process.
With respect to flux, in general, fluxes with higher activity levels are more resistant to bridging. This means that no-clean fluxes can be more likely to result in bridging, especially with older formulations. Newer flux formulations are available that have higher levels of performance while still meeting the requirements of no-clean classification.
Regarding the process, the flux loading and total thermal input to the board are key factors. An inadequate amount of flux can result in flux exhaustion before wave exit. Excessively high thermal inputs can also lead to bridging with three factors to measure. Preheat temperature is the first, contact time on the wave is the second, and solder pot temperature is the third. The optimal values for each should be available on the data sheet for any flux, and they will be different for every flux formulation.
There are other reasons outside of flux and process that can lead to bridging. The design of masking pallets can cause bridging if there is inadequate clearance around the devices. The PCB layout can also cause bridging if rows of leads are unable to be processed through the wave in the proper orientation (orthogonally and not parallel to the wave). These factors may not be able to be overcome through process optimizations or flux selection.
Jason Fullerton is the customer technical support engineer at the Assembly Division of MacDermid Alpha Electronics Solutions.
Suggested Items
Silicon Mountain Contract Services Enhances SMT Capabilities with New HELLER Reflow Oven
07/17/2025 | Silicon Mountain Contract ServicesSilicon Mountain Contract Services, a leading provider of custom electronics manufacturing solutions, is proud to announce a significant upgrade to its SMT production capability with the addition of a HELLER 2043 MK5 10‑zone reflow oven to its Nampa facility.
Knocking Down the Bone Pile: Addressing End-of-life Component Solderability Issues, Part 4
07/16/2025 | Nash Bell -- Column: Knocking Down the Bone PileIn 1983, the Department of Defense identified that over 40% of military electronic system failures in the field were electrical, with approximately 50% attributed to poor solder connections. Investigations revealed that plated finishes, typically nickel or tin, were porous and non-intermetallic.
SHENMAO Strengthens Semiconductor Capabilities with Acquisition of PMTC
07/10/2025 | SHENMAOSHENMAO America, Inc. has announced the acquisition of Profound Material Technology Co., Ltd. (PMTC), a premier Taiwan-based manufacturer of high-performance solder balls for semiconductor packaging.
KYZEN to Highlight Understencil and PCB Cleaners at SMTA Querétaro Expo and Tech Forum
07/09/2025 | KYZEN'KYZEN, the global leader in innovative environmentally responsible cleaning chemistries, will exhibit at the SMTA Querétaro Expo & Tech Forum, scheduled to take place Thursday, July 24, at Centro de Congresos y Teatro Metropolitano de Querétaro.
Driving Innovation: Direct Imaging vs. Conventional Exposure
07/01/2025 | Simon Khesin -- Column: Driving InnovationMy first camera used Kodak film. I even experimented with developing photos in the bathroom, though I usually dropped the film off at a Kodak center and received the prints two weeks later, only to discover that some images were out of focus or poorly framed. Today, every smartphone contains a high-quality camera capable of producing stunning images instantly.