-
- News
- Books
Featured Books
- smt007 Magazine
Latest Issues
Current IssueWhat's Your Sweet Spot?
Are you in a niche that’s growing or shrinking? Is it time to reassess and refocus? We spotlight companies thriving by redefining or reinforcing their niche. What are their insights?
Moving Forward With Confidence
In this issue, we focus on sales and quoting, workforce training, new IPC leadership in the U.S. and Canada, the effects of tariffs, CFX standards, and much more—all designed to provide perspective as you move through the cloud bank of today's shifting economic market.
Intelligent Test and Inspection
Are you ready to explore the cutting-edge advancements shaping the electronics manufacturing industry? The May 2025 issue of SMT007 Magazine is packed with insights, innovations, and expert perspectives that you won’t want to miss.
- Articles
- Columns
- Links
- Media kit
||| MENU - smt007 Magazine
DSG: Breaking Ground on the Smart Factory Revolution
April 17, 2019 | Barry Matties, I-Connect007Estimated reading time: 4 minutes
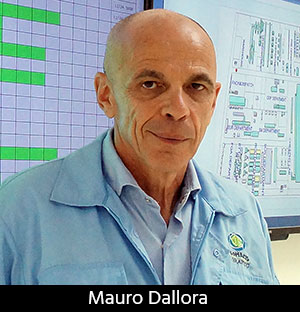
Mauro Dallora leads the I-Connect007 team through the Dongguan Somacis Graphic (DSG) PCB Co. Ltd. facility in China, lays out the company’s strategy for becoming an Industry 4.0 smart factory, and explains the current ongoing major expansion. Read about various topics in this factory tour and interview.
I-Connect007 first visited DSG about eight years ago. At that time, DSG was four years into taking on the challenge of building a PCB manufacturing factory from the ground up in Dongguan, China. As a joint venture between SOMACIS SpA and Graphic Plc, Mauro was charged to handle the enormous project, and he did just that.
Giovanni Tridenti, Mauro, and a few young guys arrived at the dirt lot in Dongguan with a suitcase, a checkbook, and a lot of ideas. Then, they got started. Two years and a million decisions later, the showcase factory was tooled with state-of-the-art equipment, well-thought-out systems, and an entire team of exclusively Chinese workers producing world-class PCBs.
At that time, most of the employees lived at the company’s newly constructed on-site dormitories. Mauro was also responsible for training his team on not just the process of building a board but also how to take care of customers, the facility, and process equipment. Aside from all of that, he also had to build a cafeteria to feed and nourish the workforce properly. Again, this was from the ground up in a China that was very different from today.
China is a rapidly and ever-changing environment from business to social issues. It was not that many years back when a large segment of the population relied on bicycles as their primary mode of transport. Today, the roads are congested with private cars and ride services, and all are filled with people connected on their mobile devices. Not only are the roads congested, but factories are now faced with a new problem—parking. Since most factories were built before the boom in privately owned vehicles, allowing space for employee parking was not a consideration. In my recent visit to DSG in Dongguan, China, that’s exactly what Mauro commented on:
Mauro Dallora: Look at the cars. When we started the facility, there were two cars—the company cars. Now, operators come in by car, and you can see the road is full of our employees’ cars.
Barry Matties: Parking space for cars isn’t the only change facing Chinese companies; wage pressure is a growing and ever-present concern. What have wages been like over the past 13 years, and what sort of percentage increase has there been?
Mauro: Wages increased from 20–25% year to year. The labor cost is a big matter because you have to spend on recruitment and for them to go through the procedure including taking them to a hospital for examination. Then, before they can do any operation, they must take at least one month of training in the factory. It is a big investment.
Now, after 13 years of meeting all of the challenges with success, Mauro and the leadership of DSG recognize their factory will be less and less competitive if they do not make some serious changes. This is much more than updating a few pieces of equipment; it starts with the idea of becoming a leading 4.0 smart factory.
The goal is to be a factory that will meet the needs of future technology and increase capability and yields while counteracting the demanding wage pressure and other rising costs faced in China.
To accomplish this new manufacturing model, Mauro is again leading this major project to retool and expand the entire factory. The plans have been made, the smart systems have been mapped out, the new equipment has been ordered, and the ground has been broken.
As you would expect, the new digital smart factory will be managed in real-time. Every item will be tracked and monitored throughout the entire process from planning to shipping. Automation will take over, and process operators will become a thing of the past. Incoming work will be uniquely marked so the machines will automatically adjust their parameters accordingly.
All of this automation will be supported with high-level mechanization to keep it a hands-off process virtually from start finish. Mauro describes it this way:
Mauro: We are talking about a smart factory—Industry 4.0. Each piece of equipment will be able to read and record every single panel in real-time. We will no longer manually record process by process; instead, every single board will have identifying marks, and everything will be done automatically. We will have a central control room where we have access to all of the information, and we will have full traceability in real-time for every single board not only for us but also for the customer.
Also, we have a commitment to double the size in revenue in five years. In South China, if you have a company that strategically fits with the region’s growth plan, you get support from the local government. If you’re not strategic, forget Guangdong because the labor cost will be too high, fewer people are available to employ, and there are tough environmental regulations and social requirements. There’s no way you can make clothes or garments here anymore.
To read the full article, which appeared in the March 2019 issue of SMT007 Magazine, click here.
Suggested Items
China Plus One, Part 3: Inorsen Group, a Vietnam Success Story
07/03/2025 | Manfred Huschka, Manfred Huschka Management Consulting (Shenzhen) Ltd.In recent years, Western OEMs have continued to push for China Plus One factories and the advancement of China’s Belt and Road Initiative (BRI). At present, there are two main modes for PCB companies to go global: building greenfield factories or through mergers and acquisitions (M&A). Thailand is currently the primary geographic choice to build greenfield factories, whereas, increasingly, mergers and acquisitions in Vietnam and Malaysia provide opportunities for companies to expand markets and acquire resources.
I-Connect007 Editor’s Choice: Five Must-Reads for the Week
06/20/2025 | Andy Shaughnessy, I-Connect007It’s been a busy week in this industry, and we have news and articles from the PCB design, fabrication and assembly communities. Some of this news is out of this world. We may be losing the high ground—the really high ground. Columnist Jesse Vaughan explains how the U.S. seems to be falling behind in space, and how this could affect our ability to defend ourselves in the future. We have an update on the U.S.-China tariff talks, which seem to be moving forward, though sometimes at a snail’s pace.
MRSI Systems, LLC Files Patent Infringement Lawsuit Against Suzhou LieQi in China
06/16/2025 | MRSI Systems, LLCMRSI Systems, LLC (a part of Mycronic Group), a global high-tech company that provides high precision production solution in electronics industry, filed a patent infringement lawsuit against Suzhou LieQi Intelligent Equipment Co., Ltd. (SZLQ) with Shenzhen Intermediate People’s Court for infringement of MRSI Systems’ patent related to die bonder (Case No. (2025) YUE03minchu No. 7154).
Takeaways from the Keynotes at the Edinburgh EIPC Summer Conference
06/16/2025 | Pete Starkey, I-Connect007It was seasonably wet and windy in Edinburgh, Scotland, June 3-4, where delegates from 17 countries convened for the 2025 EIPC Summer Conference to enjoy a superlative program of 18 technical presentations over two days, plus an excursion to a whisky distillery. EIPC President Alun Morgan welcomed everyone to the Delta Hotel, reminding us that in its previous iteration, it was the Royal Scot, traditionally the annual venue of the Institute of Circuit Technology Northern Symposium.
Global Citizenship: Cultivating Cross-border Partnerships With Integrity
06/11/2025 | Tom Yang -- Column: Global CitizenshipWith rising geopolitical pressures, cross-border partnerships are essential for businesses looking to expand their reach, enhance innovation, and drive sustainable growth. However, these partnerships thrive only when founded on trust and transparency. Otherwise, even the most promising collaborations can quickly unravel, leading to financial losses and reputation damage.