-
-
News
News Highlights
- Books
Featured Books
- pcb007 Magazine
Latest Issues
Current IssueThe Hole Truth: Via Integrity in an HDI World
From the drilled hole to registration across multiple sequential lamination cycles, to the quality of your copper plating, via reliability in an HDI world is becoming an ever-greater challenge. This month we look at “The Hole Truth,” from creating the “perfect” via to how you can assure via quality and reliability, the first time, every time.
In Pursuit of Perfection: Defect Reduction
For bare PCB board fabrication, defect reduction is a critical aspect of a company's bottom line profitability. In this issue, we examine how imaging, etching, and plating processes can provide information and insight into reducing defects and increasing yields.
Voices of the Industry
We take the pulse of the PCB industry by sharing insights from leading fabricators and suppliers in this month's issue. We've gathered their thoughts on the new U.S. administration, spending, the war in Ukraine, and their most pressing needs. It’s an eye-opening and enlightening look behind the curtain.
- Articles
- Columns
Search Console
- Links
- Media kit
||| MENU - pcb007 Magazine
Estimated reading time: 4 minutes
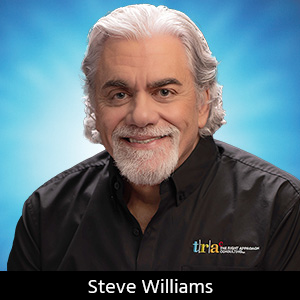
The New Frontier of Manufacturing
Even my good friend James Tiberius Kirk, who has spurred major technological advancements in the medical field, could have predicted the quantum shift in today’s manufacturing technologies. What just a short time ago would have been fodder for a Jetson’s episode is now manufacturing reality in today’s smart factory realm.
It’s All About Connectivity
In the rise of this fourth industrial revolution (Industry 4.0), connectivity is king. Buzzwords like the internet of things (IoT), and machine-to-machine (M2M) and human-to-machine (H2M) communication appear to be involved in every conversation as the industry shifts from more traditional automation to a fully connected and flexible system—one that can use a constant stream of data from connected equipment and manufacturing systems to learn and adapt to ever-changing customer needs (Figure 1).
At IPC APEX EXPO 2019, I interviewed Norihiro Koike, president and CEO of Saki. Nori described the technology behind Saki’s industry- leading automated optical inspection (AOI) and 3D equipment. Imagine if a 3D AOI or solder paste inspection (SPI) system could be self-programming, require only a few clicks, and take less than 10 minutes to program. There’s no need to imagine because Saki offers this technology today! Focusing on smart contract manufacturing factories, automated SMT lines require cutting-edge innovation to keep up. These systems feed back real-time process data that allows the SMT equipment to make on-the-fly process adjustments based on the incoming data. Amazing!
A History Lesson
It is hard to believe that iPhones have only been around since 2007. The smartphone was such a step-function advancement in mobile technology that it led to the concept of IoT a short year later. Apple sold about 11 million iPhones in the first full year after their launch—a number that has skyrocketed every year since to a level of 217 million last year [1]. In addition, there were less than five billion connected devices in the world in 2008, but by the end of this year, it is predicted that this number will explode to over 50 billion [2].
What Makes a Factory Smart?
Automation? Duh! However, it is not enough to employ automation whenever possible; smart factories require intelligent automation. In other words, equipment must talk to each other and adjust the process based on the data being collected. Challenges that many operations face are the fact that we have a lot of equipment and/or processes that do not lend themselves to connectivity, either as mechanical processes or the capability of the equipment. This is where mobile solutions can play a major role. Such solutions collect data from stranded assets that are not digitally integrated and can be sent digitally to decision makers through tablets or apps. The overall productivity and efficiency of the workplace improves using actionable insights derived from the data using mobile access.
Quality Has a Role
AOI has been around a long time in our industry, but new technologies make use of incredibly high-resolution cameras that can detect defects and concerns far more reliably (and infinitely faster) than the human eye. When integrated with a cloud-based data collection system, defects are instantly flagged and actions are automatically coordinated.
Artificial Intelligence
There have been a number of science-fiction movies over the years about well-meaning machines built with AI that learn too much and became autonomous and malicious. Most of these movies deal with a single machine that rebels against its inventor. I could make a convincing argument that the absolutely horrid 1986 movie “Maximum Overdrive” was actually the first introduction of IoT and M2M in the movies, which is astounding since the World Wide Web was not even created until 1990 (I really don’t recommend renting the DVD to prove my point).
In the context of IoT and M2M, machine learning is a reality and equipment really can learn from performing a task over and over or collecting repetitive process data. One such application is the concept of predictive maintenance, which is your typical PM program on steroids. Smart factories are employing machine learning cloud-based software to detect and predict defects in their machinery before issues arise through data collection. This allows for predictive maintenance that can cut down on unexpected delays, which can cost time, money, and customers.
Machine-to-business
While M2M and H2M connectivity are the primary focus of Industry 4.0, the true underlying benefit of Industry 4.0 comes in the form of machine-to-business (M2B) connectivity or the "machine-as-a-service" concept. This is changing the way we purchase equipment. Today, some companies look past the traditional efficiency equipment and focus instead on how it can drive revenue. For example, contract manufacturers no longer purchase manufacturing equipment in a one-and-done payment. Instead, they negotiate the key performance indicators (KPIs) of the equipment in advance, and then partially finance or lease the equipment based on the machine’s output. This ensures that their equipment set is always the latest and greatest and that their technology remains fresh and current. PCB manufacturers could take a lesson from their upstream brethren here.
I have been a life-long believer in the old adage “Work smarter, not harder.” I preach this to all of my clients. It is both interesting and exciting to watch our factories begin to follow suit.
References
1. Statista. 2019. “Unit Sales of the Apple iPhone Worldwide from 2007 to 2018 (in Millions).”
2. Otto Motors (originally posted via ARC Advisory Group). July 27, 2018. “Five Key Industry 4.0 Technologies.”
Steve Williams is the president of The Right Approach Consulting.
This article was initially published in the March 2019 issue of The PCB Magazine.
More Columns from The Right Approach
The Right Approach: ‘Twas the Night Before Christmas (Harley-style)The Right Approach: I Hear the Train A Comin'
The Right Approach: Culture Change is Key to a QMS
The Right Approach: Leadership 101—Be a Heretic, Not a Sheep
The Right Approach: Leadership 101—The Law of Legacy
The Right Approach: Leadership 101: The Law of Explosive Growth
The Right Approach: Leadership 101—The Law of Timing
The Right Approach: The Law of Sacrifice