-
- News
- Books
Featured Books
- pcb007 Magazine
Latest Issues
Current IssueSales: From Pitch to PO
From the first cold call to finally receiving that first purchase order, the July PCB007 Magazine breaks down some critical parts of the sales stack. To up your sales game, read on!
The Hole Truth: Via Integrity in an HDI World
From the drilled hole to registration across multiple sequential lamination cycles, to the quality of your copper plating, via reliability in an HDI world is becoming an ever-greater challenge. This month we look at “The Hole Truth,” from creating the “perfect” via to how you can assure via quality and reliability, the first time, every time.
In Pursuit of Perfection: Defect Reduction
For bare PCB board fabrication, defect reduction is a critical aspect of a company's bottom line profitability. In this issue, we examine how imaging, etching, and plating processes can provide information and insight into reducing defects and increasing yields.
- Articles
- Columns
- Links
- Media kit
||| MENU - pcb007 Magazine
Alun Morgan on the Future of PCB Materials
May 16, 2019 | I-Connect007 Editorial TeamEstimated reading time: 5 minutes
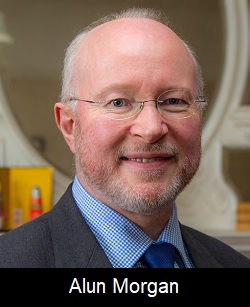
The I-Connect007 editorial team asked Alun Morgan, technology ambassador for Ventec International Group, to discuss materials at a high level. Our conversation delivered a detailed overview of the current state of the electronics industry. Put industry experts like Alun Morgan, Happy Holden, Patty Goldman, Barry Matties, Andy Shaughnessy, and Nolan Johnson together on the topic of materials, and the results are enlightening, to say the least.
Barry Matties: Thanks for taking the time to speak with us, Alun. We always appreciate the conversation.
Nolan Johnson: Today’s topic is materials, and as you know, there’s a great deal of demand from automotive, IoT, and other new technologies. These sectors are pushing the limits for designers and materials. We want to investigate what’s going on with the development of materials in the marketplace.
Matties: Also, there are so many choices out there. How do people navigate the options and make the proper choice?
Alun Morgan: That’s always a challenge. People publish lots of data sheets on new products, so it is difficult sometimes. Right now, there are a few drivers. The last driver was reliability, and the last transition for the past 15–20 years has been to improve reliability. Also, 5G is very hot and an enabler to help us move on with IoT, autonomous driving, etc. Now, we’re seeing a huge demand for products that will help enable the 5G rollout and revolution, which is coming towards the end of this year. Further, 5G brings a lot of issues because of the data rates. An entire infrastructure will have to be built. It’s probably the next big rollout of infrastructure since the technology boom around the late ‘90s with the huge amount of infrastructure built into the network that we’re still using today. There are two parts that concern PCB materials—the dielectric and conductor—and both have challenges with high speed.
Normally, in the digital space, people run 10– 20 Gbps fairly routinely, and that can be managed. But once you reach higher speeds and data rates—as we’ve seen with radar products, for example—then the substrate itself becomes a bit of an issue because the substrate is a dielectric. It can be polarized by high-frequency signals, so if you think back to when they showed you the north and south poles on magnets in school, north and south poles on magnets, you can align all of these by putting a magnet on the top. If you switch it around, all of the poles switch around the other way.
Alternating current does that all the time; it alternates up and down very quickly. All of these small, polarizable bits in the substrate flick back and forth all the time. Absorbing energy and generating heat is exactly the same way that a microwave oven works. In that case, it’s a water molecule that’s vibrating back and forth, generating heat. But overall, generating heat is bad in two ways. First, you have to get rid of it, so in big server farms, there’s a lot of heat to get rid of because you’ve generated a lot of extra heat. Second, it saps the signal, so if you put 100 in, 20 will be used for heat and only 80 will be used for the signal. You end up with a loss of signal.
The property we talk about for that is called the dissipation factor, which is a number; it’s dimensionless. The dissipation factor in a vacuum is zero, more or less, so you have no loss. And this number continues to rise depending on the kind of material you have and the frequency. There has been a big push to get that number lower and on the substrate side. About the lowest that we know of so far are PTFE materials, which are extremely difficult to polarize because the structure is pretty simple. It’s a carbon backbone with fluorine atoms on either side. As fluorine is highly reactive the atoms get as far away from each other as they can, so they form a twisted helix and force themselves in position so that they can’t vibrate, which is whyPTFE has a very low loss. Materials like FR-4 are very polarizable; they contain moisture and all kinds of things that can be polarized. You end up with orders of magnitude difference in loss, so the drive has been towards that low side.
The other big problem is copper. It has a certain roughness on one side, particularly to stick it to the substrates, you don’t want the copper falling off. Typically, in modern circuitry, the copper thickness is 17 microns or one-half ounce, sometimes even less. For a 17-micron foil, the treatment on the back of it can be five or even eight microns, even half of the total thickness can be treated, which is very rough; it’s like hills and valleys or a mountain range.
The problem is as you reach higher and higher frequencies, the electrons travel in the outside of the conductor—not through the bulk of it. Even at relatively low frequencies, you find all of the electrons flowing to the outside of the conductor. One side is pretty smooth and flat while the other side is very mountainous and hilly. The electrons have to travel a further distance on the lower side and through a higher resistance path. That compromises signal integrity as well. As you reach a higher frequency, you must have lower profiles on the copper down to submicron level, which is a bit of a challenge on the copper side.
You must also consider the reinforcement in the substrate, which is formed from a resin and a reinforcement. PTFE will most likely be the lowest loss that we have because we normally use glass fibers. Glass fibers are used for reinforcement because they’re very stable, hold everything in place, and stop things from moving around. They’re pretty inert, so you can process them through wet chemistry and not have them dissolve or become damaged. The problem is that the electrical properties of the resin and glass fiber are quite different.
You might think of the dielectric constant of the resin, and it could be a value in the order of three. The dielectric constant of the glass is at least double that, so around six, and it has a capacitive effect. How much charge can the material carry and hold? Glass holds a lot more than the resin does. If you try to send signals down there with a pair of conductors—like a differential pair—and one of those conductors runs along a bit of laminate with a lot of glass underneath it and another part of the pair runs along a bit that’s got a lot of resin underneath it, they see a very different dielectric property of the material. One of those conductors has a significantly slower signal speed compared to the other one, and you wind up with mismatches in the signal integrity.
To read the full article, which appeared in the May 2019 issue of PCB007 Magazine, click here.
Suggested Items
I-Connect007 Editor’s Choice: Five Must-Reads for the Week
07/18/2025 | Nolan Johnson, I-Connect007It may be the middle of the summer, but the news doesn’t quit, and there’s plenty to talk about this week, whether you’re talking technical or on a global scale. When I have to choose six items instead of my regular five, you know it’s good. I start by highlighting my interview with Martyn Gaudion on his latest book, share some concerning tariff news, follow that up with some promising (and not-so-promising) investments, and feature a paper from last January’s inaugural Pan-European Design Conference.
Elephantech Launches World’s Smallest-Class Copper Nanofiller
07/17/2025 | ElephantechJapanese deep-tech startup Elephantech has launched its cutting-edge 15 nm class copper nanofiller – the smallest class available globally. This breakthrough makes Elephantech one of the first companies in the world to provide such advanced material for commercial use.
Copper Price Surge Raises Alarms for Electronics
07/15/2025 | Global Electronics Association Advocacy and Government Relations TeamThe copper market is experiencing major turbulence in the wake of U.S. President Donald Trump’s announcement of a 50% tariff on imported copper effective Aug. 1. Recent news reports, including from the New York Times, sent U.S. copper futures soaring to record highs, climbing nearly 13% in a single day as manufacturers braced for supply shocks and surging costs.
I-Connect007 Editor’s Choice: Five Must-Reads for the Week
07/11/2025 | Andy Shaughnessy, Design007 MagazineThis week, we have quite a variety of news items and articles for you. News continues to stream out of Washington, D.C., with tariffs rearing their controversial head again. Because these tariffs are targeted at overseas copper manufacturers, this news has a direct effect on our industry.I-Connect007 Editor’s Choice: Five Must-Reads for the Week
Digital Twin Concept in Copper Electroplating Process Performance
07/11/2025 | Aga Franczak, Robrecht Belis, Elsyca N.V.PCB manufacturing involves transforming a design into a physical board while meeting specific requirements. Understanding these design specifications is crucial, as they directly impact the PCB's fabrication process, performance, and yield rate. One key design specification is copper thieving—the addition of “dummy” pads across the surface that are plated along with the features designed on the outer layers. The purpose of the process is to provide a uniform distribution of copper across the outer layers to make the plating current density and plating in the holes more uniform.