-
- News
- Books
Featured Books
- smt007 Magazine
Latest Issues
Current IssueWhat's Your Sweet Spot?
Are you in a niche that’s growing or shrinking? Is it time to reassess and refocus? We spotlight companies thriving by redefining or reinforcing their niche. What are their insights?
Moving Forward With Confidence
In this issue, we focus on sales and quoting, workforce training, new IPC leadership in the U.S. and Canada, the effects of tariffs, CFX standards, and much more—all designed to provide perspective as you move through the cloud bank of today's shifting economic market.
Intelligent Test and Inspection
Are you ready to explore the cutting-edge advancements shaping the electronics manufacturing industry? The May 2025 issue of SMT007 Magazine is packed with insights, innovations, and expert perspectives that you won’t want to miss.
- Articles
- Columns
- Links
- Media kit
||| MENU - smt007 Magazine
From DataED’s NPI Center to the Manufacturing Floor
May 17, 2019 | I-Connect007 Editorial TeamEstimated reading time: 5 minutes
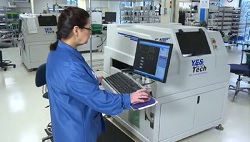
The I-Connecct007 team recently spoke with a team of technologists and managers at Data Electronic Devices (DataED). We had a wide-ranging discussion with Jeff Hamlett, director of sales and marketing; Lori Giglio, general manager at the NPI Engineering Center; Vic Giglio, president and CEO; and Ron Sprizza, VP of quality for DataED. They provided an overview of the importance of company culture and making your customers the first priority. They also discuss how they collaboratively help customers move from NPI to making products on the manufacturing floor.
Nolan Johnson: Jeff, can you tell us about DataED, where you are located, and what your role is with the company?
Jeff Hamlett: We’re headquartered in Salem, New Hampshire. We have two facilities in Salem, one being the worldwide headquarters plus domestic production. We also have our new product introduction (NPI) prototype facility, which stands alone and is located about four miles from our headquarters where we do a lot of NPIs and prototypes for quick turns. We also have two facilities in Shenzhen, China, that we opened up in 2002, and we’ve been running successfully over there for 15–17 years. DataED started in 1980, so we’ve been in existence in the contract manufacturing arena for 39 years now. We’ve grown tremendously over the last few years. I joined DataED in 2010 as the director of sales and marketing. Before DataED, I was with another contract manufacturer in Vermont as well as Massachusetts—Nexus, a small Tier 3 CM. I’ve been in the contract manufacturing world for close to 30 years.
Johnson: What’s the one thing you want every customer to understand about delivering a job to your shop?
Hamlett: It’s mostly about understanding the culture of our company. We’re in Tier 2 manufacturing and we’re in the $100 million category now. We like to think of ourselves as a family atmosphere and build relationships with the customers we have. Anybody can build a product, but it’s important to have established relationships and treat the customers well, which has led to our success today. We have all of the bells and whistles that other CMs do, but that’s the one factor that makes us stand apart.
Johnson: Lori, can you tell us a little bit about your background and your role at DataED?
Lori Giglio: I’m the general manager at the NPI Engineering Center for Data Electronic Devices and have been with DataED for 18 years now. I started as an account manager, and when they opened up the NPI Center about four years ago, I came over with a small team to head up the project, which has been very successful.
We came over with approximately 4–5 dedicated employees, and now we’re up to 13. The business has been successful since day one. We were profitable in the first year, which was a surprise to everybody. But it speaks to the service we offer, and the commitment that we have to our customers and their success.
Johnson: What’s the one thing that you want every customer to understand about delivering a job to your shop?
Lori Giglio: Our customers are our first priority. Every customer that walks through our door, in my philosophy of business, should feel like they’re the only customer and that their project is of the utmost importance to us. It should be completed in a timely manner within the timeframe we commit to, and they should be treated with the respect that they deserve.
Hamlett: Recently, we’ve been talking about what differentiates us from other companies. Some of our customers had complaints about the way we were doing business, and we listened and came up with a solution for everyone. And with that, the word spread. We don’t have people trying to sell the business; it has been spread by word of mouth.
Lori Giglio: We have a high referral rate from our customers. We receive a lot from customers once they’ve engaged with us, done business with us, and are happy with the service they received. Customers often send me referrals to other companies in different industries that they are aware of that need the services we offer at the NPI Center. Again, our customer-focused philosophy is working.
Johnson: What services or assistance can you provide at DataED that your customers seem to overlook?
Hamlett: From a production standpoint, one of the things that people don’t know that we have is conformal coatings for the assemblies. We offer tests and test design and do a lot of repair work, including ball grid arrays (BGAs), as well as design for manufacturing (DFM) and design for testing (DFT). We have some environmental stuff too. A lot of people don’t know that because they think of us as a board house that builds boards and stuffs parts on them, but we offer more than that. And in terms of materials, we can look at the bill of materials (BOM) and give customers an idea of if there are obsolete parts listed. If parts are going to go end of life, we can make them aware of that so that they can do last-time buys.
Lori Giglio: I agree, Jeff. Even though I don’t have conformal coatings at the NIP Center, I have the extension of the production facility. I can offer services that a small, standalone NPI center could not offer because I can offer them through the other facility. I can offer to do conformal coatings, for example. And we can offer the test aspect if customers need it because we have a big production facility on the other side of town.
We also offer that same engineering and manufacturing expertise. We’re approaching it from an engineering perspective to look at the design, build it, critique it, and help the customers. Often, the customers are on site and present. If not, they’re definitely involved. We engage throughout the whole process, so they’re learning as well.
To read the full article, which appeared in the May 2019 issue of SMT007 Magazine, click here.
Suggested Items
Hon Hai Education Foundation Continues to Promote Quantum Education
07/04/2025 | FoxconnHon Hai Education Foundation has long been committed to promoting forward-looking technology education in Taiwan's high schools, and held the "High School Quantum Teacher Training Camp" in Tainan City on July 1.
Incap UK Achieves JOSCAR Zero Accreditation
07/04/2025 | IncapIncap Electronics UK has been accredited under JOSCAR Zero, a new sustainability-focused extension of the defence and aerospace sector’s supplier assurance system.
Kitron Secures Contract for Components Supporting Unmanned Aerial Systems
07/04/2025 | KitronKitron has received a contract with an estimated value between EUR 4 and 8 million for the production and supply of advanced electronic components used in unmanned aerial systems (UAS).
NOTE Receives Order Worth 132 MSEK and Expands Collaboration with Customer within Security & Defense
07/04/2025 | NOTENOTE has received an order worth SEK 132 million from one of its existing customers operating within Security & Defense. NOTE thereby strengthens its long-term collaboration with the industry-leading customer.
Delta SEA Partner Event 2025 Unites Regional Partners to Embrace a “Future Ready” Vision
07/03/2025 | Delta ElectronicsDelta Electronics (Thailand) Public Company Limited, successfully hosted its Delta SEA Partner Event 2025: Future Ready at Delta Chungli Plant 5, Taiwan on June 10 – 11 , 2025.