-
- News
- Books
Featured Books
- smt007 Magazine
Latest Issues
Current IssueSupply Chain Strategies
A successful brand is built on strong customer relationships—anchored by a well-orchestrated supply chain at its core. This month, we look at how managing your supply chain directly influences customer perception.
What's Your Sweet Spot?
Are you in a niche that’s growing or shrinking? Is it time to reassess and refocus? We spotlight companies thriving by redefining or reinforcing their niche. What are their insights?
Moving Forward With Confidence
In this issue, we focus on sales and quoting, workforce training, new IPC leadership in the U.S. and Canada, the effects of tariffs, CFX standards, and much more—all designed to provide perspective as you move through the cloud bank of today's shifting economic market.
- Articles
- Columns
- Links
- Media kit
||| MENU - smt007 Magazine
Estimated reading time: 4 minutes
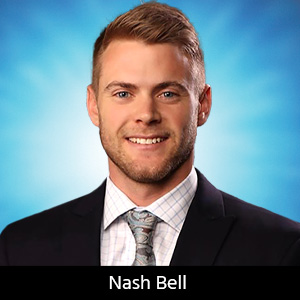
Knocking Down the Bone Pile: Straightening Out Those Corners
Physical damage to a printed circuit assembly is typically done to the board through improper handling. A board can be dropped, dinged, or mishandled as it is placed into a board carrier in the PCB assembly operations area (Figure 1). When the laminated material is damaged in this manner, can it be repaired? The answer, like most engineering answers, is that it depends.
The industry standard IPC-A-610 “Acceptability of Electronics Assemblies” describes the various conditions for what is acceptable and what is defective based on the class of the electronics. This inspection specification calls out broken corners or laminate damage as a defect when the minimum electrical clearance is violated, and the assembly does not fit the “form, fit, or function” as it is designed to be part of the assembly or it does not meet the specification on the customer’s print.
Figure 1: A PCB with a damaged corner.
All of the above are defects per the acceptability standards for all classes of products. In addition, for any of the classes, if the base metal is exposed because of the edge or corner damage, it too would be determined to be a defect. Per section 10.2.5 of the IPC-A-610 standard, if the “nick” or corner damage exceeds 50% of the distance from the PCB edge to the nearest conductor of 2.5 mm (0.1 inches) or less, that would also be deemed a defect.
While customers will ultimately decide what is a defect by choosing the previously cited industry standards, there are various types of disposition once it has been determined that the damaged corner represents a defect condition.
The options are to use the board as is (with customer approval), repair it (physical damage to the PCB), or scrap it. When the second option is chosen, the corner of the PCB requires repair.
When a board is physically damaged either by mishandling, or by the assembly being dropped, and the corner is damaged or missing, there are several other items to inspect on the assembly. In some cases—especially for brittle solders, such as various lead-free alloys—the solder joints may be fractured due to the physical event. In addition, parts near the corner may have pads or traces ripped off. If the PCB has a coating, then it may have become fractured after the assembly was dropped. Finally, there needs to be an inspection of the solder mask as well as the component bodies that may have been destroyed during the impact.
There are a variety of methods outlined in the PCB repair guidelines for PCBs—IPC-7721 “Rework, Modification, and Repair of Electronic Assemblies.” The first method is a repair using epoxy to repair the laminate. Generally, this method is used to repair minor damage to the laminate. Second, you can use an area or corner transplant method. This is used when there is extensive damage to the PCB laminate or when the material is no longer existing, such as in the case when a corner is broken off. As the name of the method implies, a replacement laminate is used and glued using a tongue and groove joint to make the repair.
Figure 2: Repaired corner of a PCB (not color-matched for illustration purposes).
The focus of this column will be on the epoxy method, which has been adopted for the repair of broken or damaged corners on rigid, assembled PCBs. The first step is discerning to what extent the PCB has been damaged. First, clean the area to make sure that the area can be thoroughly inspected. Either through evaluation of the Gerber file set or X-ray analysis, determine if any inner layer circuit traces may have been damaged. If there are no circuits in the inner layers or missing parts due to the damage, then the repair method described will be the only one required.
Use a ball mill to grind off rough edges or fibers of the laminate. If it is a large corner, perform an undercut into the laminate edge to increase the bonding area. If interior circuitry has been damaged, then you will need to have the approval and/or skill to make those repairs. Then, find a small plastic box that you would find for holding small tools or nuts and bolts. This will be a single use of the box, so make sure that if you “borrow” it from somewhere else that you can easily get a replacement.
Next, mix the two-part resin and hardener over the manufacturer’s instructions. Now, using the small container that has been modified to leave only a single corner, place the remaining corner so that it aligns with the damaged corner. Pour the epoxy mixture into the box and smooth the surface. Cure the epoxy per the manufacturer’s instructions as well. Using emery cloth and some water, wet sand to make fit the corner. You may have to add some epoxy and/or colorant to match the form, fit, and function of the corner (Figure 2). Clean and re-inspect the repaired area per the acceptance criteria based on the class of the electronics assembly.
Using this epoxy method, you can successfully straighten out the corner of the board and not have to discard it in the scrap heap.
Bob Wettermann is the principal of BEST Inc., a contract rework and repair facility in Chicago.
More Columns from Knocking Down the Bone Pile
Knocking Down the Bone Pile: Addressing End-of-life Component Solderability Issues, Part 4Knocking Down the Bone Pile: Tin Whisker Mitigation in Aerospace Applications, Part 3
Knocking Down the Bone Pile: Gold Mitigation for Class 2 Electronics
Knocking Down the Bone Pile: Basics of Component Lead Tinning
Knocking Down the Bone Pile: Package on Package Rework—Skill Required
Knocking Down the Bone Pile: 2023’s Top Challenges in BGA Rework
Knocking Down the Bone Pile: Eliminating Solder Balls in Hand Soldering
Knocking Down the Bone Pile: Opening a Trace on the Surface of a PCB