-
- News
- Books
Featured Books
- smt007 Magazine
Latest Issues
Current IssueWhat's Your Sweet Spot?
Are you in a niche that’s growing or shrinking? Is it time to reassess and refocus? We spotlight companies thriving by redefining or reinforcing their niche. What are their insights?
Moving Forward With Confidence
In this issue, we focus on sales and quoting, workforce training, new IPC leadership in the U.S. and Canada, the effects of tariffs, CFX standards, and much more—all designed to provide perspective as you move through the cloud bank of today's shifting economic market.
Intelligent Test and Inspection
Are you ready to explore the cutting-edge advancements shaping the electronics manufacturing industry? The May 2025 issue of SMT007 Magazine is packed with insights, innovations, and expert perspectives that you won’t want to miss.
- Articles
- Columns
- Links
- Media kit
||| MENU - smt007 Magazine
The Effectiveness of 75% IPA/25% DI Extraction Solution on No-clean Flux Residues
June 13, 2019 | David Lober and Mike Bixenman, DBA, KYZEN; and Marietta Lemieux and Mark McMeen, STIEstimated reading time: 12 minutes
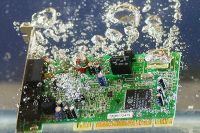
The continuous challenge in the electronics industry is to keep up with the demand for smaller, faster, and more reliable electronics. This places great strains on the manufacturers of those electronics. The strain on manufacturing electronics comes from every direction. Environmental regulations have removed lead from the majority of electronics, forcing materials changes. Packages have become smaller with more voltage requirements. Complex devices are expected to work reliably for years under harsh environments that would be unimaginable to a circuit designer one decade ago. These examples and many more combine to create a multitude of challenges.
This rapid development of manufacturing and reliability challenges is juxtaposed with the slow pace of new test method development. Resistance of Solvent Extract (ROSE) testing is the de facto ionic contamination testing method primarily because it was developed in 1970, when PCBs were becoming more common in military and other high-reliability applications. In the ROSE method, a PCB to be tested is submerged in a solution of 75% isopropanol or IPA (but more properly propan-2-ol) and 25% DI water. The change in the resistance of the solution is monitored. As ionic materials dissolve into solution, the resistance of the solution decreases, indicating that there is ionic contamination.
This dip in resistance is then converted into the mass of sodium chloride per unit area that would be expected to produce an equivalent dip in the resistance of the solution. Traditionally, this is expressed as micrograms of sodium chloride equivalent per square centimeter (μg NaCl eq. /cm2). Shortly after ROSE’s development, the United States Department of Defense decided that a value of 1.56 μg NaCl eq. /cm2 was to be used as a criterion for product acceptance. If a particular assembly was below this value, it would be acceptable for field use.
Relevant to the current work is the decision to use the extraction solution of 75%/25% IPA/DI water. This decision was made because the vast majority of solder fluxes on the market were rosin based, and therefore, highly soluble in IPA. This is because the major constituent of rosin is abietic acid and is highly soluble in IPA [1]. The true systematic name for abietic acid is abieta-7,13-dien-18-oic acid (CAS Number 514-10-3) and is shown in Figure 1 [2]. It is commonly cited as virtually insoluble in water, but it does exhibit some solubility in water [3]. It is also known to be highly soluble in various organic solvents, although exact numbers are hard to come by [2, 4, & 5].
Once dissolved into solution, abietic acid can ionize into an electrically conductive species that can be measured by resistance. This is what characterizes abietic acid as what our industry calls weak organic acids (WOAs). The degree to which the ionization occurs is highly dependent on pH, but will cause a change in resistance none the less.
Figure 1: Abietic acid structure [1].
As time progressed, newer fluxes entered the market that were not based on rosin, namely water soluble (WS), or sometimes called “water wash flux,” and no-clean (NC), or “low-residue flux.” There is a multitude of reasons why these fluxes came onto the market and why they necessitated different WOAs, but those are beyond the scope of this article. The flux manufacturers turned toward a different type of organic acid, linear dicarboxylic acids. Dicarboxylic acids are organic molecules that have two carboxylic acid groups, and linear dicarboxylic acids are simply the dicarboxylic acid derivatives of straight chain hydrocarbons.
The exact identities of the dicarboxylic acids used are considered proprietary, but there are a series of dicarboxylic acids that have been reported in the literature, such as adipic acid, succinic acid, glutaric acid, malic acid [6,7], and more recently, pimelic acid [8]. Table 1 shows the structure of these acids [9]. The important thing to note from the structures in Table 1 is that they are substantially different from that of abietic acid, and as a result, they all have some degree of solubility in water.
Table 1: Common dicarboxylic acids.
One additional consideration is that the WOAs can react. One known chemical reaction that they undergo is acid-base reactions. In this reaction, WOAs react with a base, such as an amine activator, metals, or other bases that are present. These result in the formation of a salt. Typically, organic salts are more soluble in water than organic solvents; this property is a common way to purify WOAs [10]. It is suspected by the authors that these WOA salts are capable of causing current leakage paths or even ECM. When dissolved, these salts result in the formation of an electrolyte solution.
During this time, a new cleanliness assessment method was introduced to the industry in the form of ion chromatography (IC). IC is an analytical technique from the liquid chromatography family and can be used to identify and quantify ionic species in solution. A small portion of a liquid sample (typical volume ~25 μL) is injected into a moving fluid called an eluent. The eluent carries the sample to an analytical column. This column consists of very fine particles coated with an ionic compound. This coating attracts the ions of interest, slowing them down. The degree of this slowing depends on a number of factors, but the ultimate goal is to slow each ion of interest down enough that they travel as discrete bands in the plumbing of the instrument. This causes the ions to be removed by the eluent from the column at different times.
Page 1 of 3
Suggested Items
Driving Innovation: Direct Imaging vs. Conventional Exposure
07/01/2025 | Simon Khesin -- Column: Driving InnovationMy first camera used Kodak film. I even experimented with developing photos in the bathroom, though I usually dropped the film off at a Kodak center and received the prints two weeks later, only to discover that some images were out of focus or poorly framed. Today, every smartphone contains a high-quality camera capable of producing stunning images instantly.
Hands-On Demos Now Available for Apollo Seiko’s EF and AF Selective Soldering Lines
06/30/2025 | Apollo SeikoApollo Seiko, a leading innovator in soldering technology, is excited to spotlight its expanded lineup of EF and AF Series Selective Soldering Systems, now available for live demonstrations in its newly dedicated demo room.
Indium Corporation Expert to Present on Automotive and Industrial Solder Bonding Solutions at Global Electronics Association Workshop
06/26/2025 | IndiumIndium Corporation Principal Engineer, Advanced Materials, Andy Mackie, Ph.D., MSc, will deliver a technical presentation on innovative solder bonding solutions for automotive and industrial applications at the Global Electronics A
Fresh PCB Concepts: Assembly Challenges with Micro Components and Standard Solder Mask Practices
06/26/2025 | Team NCAB -- Column: Fresh PCB ConceptsMicro components have redefined what is possible in PCB design. With package sizes like 01005 and 0201 becoming more common in high-density layouts, designers are now expected to pack more performance into smaller spaces than ever before. While these advancements support miniaturization and functionality, they introduce new assembly challenges, particularly with traditional solder mask and legend application processes.
Knocking Down the Bone Pile: Tin Whisker Mitigation in Aerospace Applications, Part 3
06/25/2025 | Nash Bell -- Column: Knocking Down the Bone PileTin whiskers are slender, hair-like metallic growths that can develop on the surface of tin-plated electronic components. Typically measuring a few micrometers in diameter and growing several millimeters in length, they form through an electrochemical process influenced by environmental factors such as temperature variations, mechanical or compressive stress, and the aging of solder alloys.