-
- News
- Books
Featured Books
- smt007 Magazine
Latest Issues
Current IssueWhat's Your Sweet Spot?
Are you in a niche that’s growing or shrinking? Is it time to reassess and refocus? We spotlight companies thriving by redefining or reinforcing their niche. What are their insights?
Moving Forward With Confidence
In this issue, we focus on sales and quoting, workforce training, new IPC leadership in the U.S. and Canada, the effects of tariffs, CFX standards, and much more—all designed to provide perspective as you move through the cloud bank of today's shifting economic market.
Intelligent Test and Inspection
Are you ready to explore the cutting-edge advancements shaping the electronics manufacturing industry? The May 2025 issue of SMT007 Magazine is packed with insights, innovations, and expert perspectives that you won’t want to miss.
- Articles
- Columns
- Links
- Media kit
||| MENU - smt007 Magazine
Cavity Board SMT Assembly Challenges (Part 2)
July 3, 2019 | Dudi Amir and Brett Grossman, Intel CorporationEstimated reading time: 17 minutes
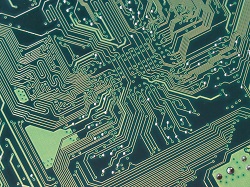
Editor’s Note: This is the second part of this article. Click here to read Part 1. This paper was first presented at SMTAI 2018 and published in the proceedings.
Stencil Selection and Design
To print solder paste into a cavity on a two-level board, a 3D stencil is required. A 3D stencil is a stencil comprised of different print levels [2]. In this case, there are two levels: the board surface and the board cavity. This differentiates it from a step-up and step-down stencil that has only one level—the board surface—which is used to print paste to achieve a thinner or a thicker deposit by varying the thickness of the stencil foil.
There are a few technologies available to build 3D stencils. The experiments in this study focused on three stencil technologies: electroformed, machined, and welded. Electroformed stencils use a metal deposition process to build a stencil and cavity around a built mandrel. The foil thickness grows as a function of time so that the process can create any stencil thickness. It forms a good quality stencil with a very smooth surface. A machined stencil requires using a machine tool to remove material from the original metal sheet to create a cavity. Some of the advantages to this method are that it provides options to selectively define the stencil thickness and to have a different thickness inside the cavity. It can also selectively machine a chamfer or have straight walls as selected by the design. Finally, a welded stencil has a hole cut into the foil where the cavity is needed. A cup is spot-welded on the foil to cover the hole. In this technology, there is a larger keep-out zone (KOZ) needed for the welding process. It also provides limited cavity depths due to set foil thickness and alignment challenges. Figure 14 shows images of the stencil cavity from all three 3D stencil technologies.
Figure 14: Stencil technology.
Each stencil technology has a unique signature that can impact the selection of that technology. Figure 14a shows an electroformed stencil with a smooth surface and a taper on both the paste and board side of the cavity walls. This taper is required in the electroforming process for easy release from the mandrill.
Figure 14b shows a machined cavity where the paste side has round corners while the board side has flat walls due to the machining process. The welded stencil in Figure 14c has flat walls with no taper and a couple of rows of spots from the welding process. The surface near the welded area is coarser, and the KOZ from the BGA aperture is smaller compared to the other stencils. There is no one stencil technology solution that can fit all applications. Selection should be made to fit the particular application in terms of build quantity, lead time, budget, cavity depth, and KOZ.
Table 2 provides comparisons of one design case for the different stencil technologies to a standard laser cut stencil in terms of cost and lead time. These estimates can change depending on the design.
Table 2: Stencils cost and lead time.
In this evaluation, the stencils’ apertures on the BGA were 330 μm square. The stencil thickness was 100 μm (4 mils). Since excessive paste was expected in the cavity, an additional machined stencil was made with reduced stencil thickness in the cavity area. The thickness was only 90 μm (3.5 mils) to reduce the risk of bridging. As mentioned, stencils from all three technologies were used in the evaluation.
SMT Setup Challenges
To use a 3D stencil with a cavity on a paste printing machine, a metal blade squeegee with two slits is used. Figure 15 shows a squeegee with two slits. The part of the squeegee between the two slits is the section that is riding inside the cavity. It has a clearance of about 0.15 mm from the cavity wall on each side to compensate for positional errors and be able to apply the full pressure to the cavity.
Figure 15: Slit squeegee.
It is critical during the printer set up to align the slit with the cavity. This may require a few trials and needs to be done to each blade separately since each blade has its own holder. A good practice is to run the blade with low pressure and speed on the stencil and observe the position of the slit. After adding the paste to the stencil, the paste lines will help to determine the correct position.
Figure 16: Slit squeegee alignment.
Figure 16a shows an improper setup where the squeegee blade needs to move to the right. The slit to the left of the cavity is riding outside of the cavity walls, causing excessive solder paste. Figure 16b shows the proper setup of the squeegee slit in the cavity where both slits are riding inside the cavity. Some paste printing machine suppliers offer a lateral squeegee adjustment, which makes this task much easier. Figure 17 illustrates a squeegee blade holder with a lateral squeegee adjustment installed.
Figure 17: Slit squeegee with a lateral adjustment head.
There are no special considerations for setup in the pick-and-place (PnP) machine or the reflow oven due to the cavity. It is worth mentioning that in the board file, the BGA pads in the cavity are non-existent on the first layer as they normally are on standard boards. Some SMT tools cannot deal with multilevel BGA pads. For example, SPI tools will need to have a modified board file which transfers the paste layer to one level. The board file image in Figure 7 illustrates this issue. Figure 7a is the information typically provided to the SPI tool, which clearly provides no reference to the BGA pads located in the cavity. Figure 7b is the result of merging the PCB bottom and the cavity layer artwork such that all of the necessary information can be provided to the SPI tool.
Page 1 of 4
Suggested Items
Driving Innovation: Direct Imaging vs. Conventional Exposure
07/01/2025 | Simon Khesin -- Column: Driving InnovationMy first camera used Kodak film. I even experimented with developing photos in the bathroom, though I usually dropped the film off at a Kodak center and received the prints two weeks later, only to discover that some images were out of focus or poorly framed. Today, every smartphone contains a high-quality camera capable of producing stunning images instantly.
Hands-On Demos Now Available for Apollo Seiko’s EF and AF Selective Soldering Lines
06/30/2025 | Apollo SeikoApollo Seiko, a leading innovator in soldering technology, is excited to spotlight its expanded lineup of EF and AF Series Selective Soldering Systems, now available for live demonstrations in its newly dedicated demo room.
Indium Corporation Expert to Present on Automotive and Industrial Solder Bonding Solutions at Global Electronics Association Workshop
06/26/2025 | IndiumIndium Corporation Principal Engineer, Advanced Materials, Andy Mackie, Ph.D., MSc, will deliver a technical presentation on innovative solder bonding solutions for automotive and industrial applications at the Global Electronics A
Fresh PCB Concepts: Assembly Challenges with Micro Components and Standard Solder Mask Practices
06/26/2025 | Team NCAB -- Column: Fresh PCB ConceptsMicro components have redefined what is possible in PCB design. With package sizes like 01005 and 0201 becoming more common in high-density layouts, designers are now expected to pack more performance into smaller spaces than ever before. While these advancements support miniaturization and functionality, they introduce new assembly challenges, particularly with traditional solder mask and legend application processes.
Knocking Down the Bone Pile: Tin Whisker Mitigation in Aerospace Applications, Part 3
06/25/2025 | Nash Bell -- Column: Knocking Down the Bone PileTin whiskers are slender, hair-like metallic growths that can develop on the surface of tin-plated electronic components. Typically measuring a few micrometers in diameter and growing several millimeters in length, they form through an electrochemical process influenced by environmental factors such as temperature variations, mechanical or compressive stress, and the aging of solder alloys.