-
- News
- Books
Featured Books
- pcb007 Magazine
Latest Issues
Current IssueThe Hole Truth: Via Integrity in an HDI World
From the drilled hole to registration across multiple sequential lamination cycles, to the quality of your copper plating, via reliability in an HDI world is becoming an ever-greater challenge. This month we look at “The Hole Truth,” from creating the “perfect” via to how you can assure via quality and reliability, the first time, every time.
In Pursuit of Perfection: Defect Reduction
For bare PCB board fabrication, defect reduction is a critical aspect of a company's bottom line profitability. In this issue, we examine how imaging, etching, and plating processes can provide information and insight into reducing defects and increasing yields.
Voices of the Industry
We take the pulse of the PCB industry by sharing insights from leading fabricators and suppliers in this month's issue. We've gathered their thoughts on the new U.S. administration, spending, the war in Ukraine, and their most pressing needs. It’s an eye-opening and enlightening look behind the curtain.
- Articles
- Columns
- Links
- Media kit
||| MENU - pcb007 Magazine
Conventional Exposing: Direct Imaging Solder Mask
July 4, 2019 | Nikolaus SchubkegelEstimated reading time: 4 minutes
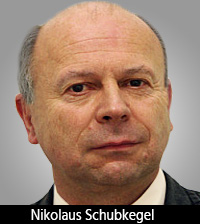
When you compare direct imaging of solder mask with contact exposure of solder mask, the positive aspects and the advantages are clear. Without a doubt, direct imaging shortens the throughput time and eliminates artwork production. It also eliminates the costly measurement of the panels and manufacturing of artwork with different scaling factors.
In this article, I present seven of these defects. These defects occur rarely on contact exposing and only when the process is not well balanced. The occurrence of these defects can be explained by the fundamental differences between contact exposure and direct exposure. But first, let’s review the direct imaging processes.
The biggest advantage of direct imaging is the ability to scale and change the dimension of each individual exposure for the best fit. With direct imaging, it is possible to expose different cards on the same panel with different spreads. The scrap rate due to misregistration tends toward zero. This is because, with artwork, you need to produce photo tools with different scaling factors, making nonlinear scaling impossible.
Direct exposure solder mask, however, does have its own set of unique defects that occur. Thankfully, these defects are well known. Due to the increased use of direct imaging of solder resists, these defects occur more often. These defects depend on the solder mask chemical composition and the photoinitiator package (a compound that reacts to light, initiating or catalysing a chemical reaction), so they can be a bit different from solder mask to solder mask. How the defects appear depends on the direct imaging unit, the wavelengths of the system, the general process parameters, the drying conditions, and the developing parameters. Even the pre-cleaning process can sometimes have an influence.
These direct exposure defects occur early on during implementation of a direct exposure unit. Once the process is optimized, the defects no longer occur. In general, there are also possibilities to prevent these defects; in other words, they are manageable.
Four Fundamental Differences Between Direct Exposure and Contact Exposure
1. Oxygen Inhibition of Surface Crosslinking
First, a fundamental difference is the oxygen inhibition of surface crosslinking. Contact exposure occurs under vacuum. A side effect of this is that oxygen adsorbed on the solder mask surface is desorbed. This low oxygen concentration does not interfere with the crosslinking of the solder mask. With direct imaging, rather, the exposure happens in the air and under normal pressure. The oxygen inhibition effect strongly depends on the photoinitiator package. Some solder resists are very sensitive to oxygen inhibition while other systems are insensitive to the presence of oxygen.
Exposure transforms certain photoinitiators from the solder resist into free radicals. These free radicals start the crosslinking of the solder resist. A portion of the free radicals stabilizes by a reaction with atmospheric oxygen. These stabilized radicals are no longer available for crosslinking. As a result, the crosslinking on the solder mask surface is disturbed by the loss. When crosslinking is incomplete, the solder mask surface will be sticky, dull, and porous. Some photoinitiators start the polymerization via a cationic photopolymerization. In this case, oxygen inhibition generally does not occur, but there are exceptions.
2. Narrow-band Light Frequencies for Direct Imaging
The second problem with direct imaging happens because light in the 200–350 nm range is missing. Contact exposure relies on mercury vapor lamps, short arc lamps, ultra-high-pressure lamps, etc., for its radiation sources. These lamps radiate throughout the UV range (200–400 nm), in the visible range (400–760 nm), and far into the infrared range.
In contrast, direct-exposure light sources emit a few discrete wavelengths in the 355–420 nm range. This radiation penetrates deep into the solder resist and starts the crosslinking in the entire mask. But these light sources do not penetrate into the solder mask because the solder mask resin absorbs strongly in this area.
The solder mask starts a massive crosslinking on the solder mask surface, creating a protective skin. The surface is sealed, the chemical resistance is improved, and the moisture absorption is reduced.
3. Quantum Yield Mismatches Due to Wavelength and Solder Mask Not Being Compatible
A third difference is the quantum yield in the formation of radicals at different wavelengths. In contact exposure, the difference in the quantum yield between the individual wavelengths does not play a major role. The whole UV range is available. Conversely, in direct exposure, one or more wavelengths are used, which form free radicals with a certain yield. Some wavelengths are very efficient with some solder resists while other wavelengths are very ineffective, which explains the different results when exposing a solder resist on different direct imagers.
4. Longer Exposure Times in Direct Imaging
The fourth problem with direct imaging is the need for longer exposing times compared to contact exposure. This is not a defect, but it does make implementation more difficult. Presently, more and more companies are switching entirely to the direct imaging of the solder mask. Some companies have maintained contact exposing and partly switched to direct exposure for reasons of capacity. However, contact exposure is still the first choice for other companies.
Since the exposing times are long, solder mask manufacturers have responded to the requirements of PCB shops by optimizing coatings for direct exposure. Existing solder masks have been modified so that all qualifications remain. It should be noted that these are still more traditional coatings and are not developed purely for direct exposure.
To read the full article, which appeared in the June 2019 issue of PCB007 Magazine, click here.
Suggested Items
SHENMAO Strengthens Semiconductor Capabilities with Acquisition of PMTC
07/10/2025 | SHENMAOSHENMAO America, Inc. has announced the acquisition of Profound Material Technology Co., Ltd. (PMTC), a premier Taiwan-based manufacturer of high-performance solder balls for semiconductor packaging.
KYZEN to Highlight Understencil and PCB Cleaners at SMTA Querétaro Expo and Tech Forum
07/09/2025 | KYZEN'KYZEN, the global leader in innovative environmentally responsible cleaning chemistries, will exhibit at the SMTA Querétaro Expo & Tech Forum, scheduled to take place Thursday, July 24, at Centro de Congresos y Teatro Metropolitano de Querétaro.
Driving Innovation: Direct Imaging vs. Conventional Exposure
07/01/2025 | Simon Khesin -- Column: Driving InnovationMy first camera used Kodak film. I even experimented with developing photos in the bathroom, though I usually dropped the film off at a Kodak center and received the prints two weeks later, only to discover that some images were out of focus or poorly framed. Today, every smartphone contains a high-quality camera capable of producing stunning images instantly.
Hands-On Demos Now Available for Apollo Seiko’s EF and AF Selective Soldering Lines
06/30/2025 | Apollo SeikoApollo Seiko, a leading innovator in soldering technology, is excited to spotlight its expanded lineup of EF and AF Series Selective Soldering Systems, now available for live demonstrations in its newly dedicated demo room.
Indium Corporation Expert to Present on Automotive and Industrial Solder Bonding Solutions at Global Electronics Association Workshop
06/26/2025 | IndiumIndium Corporation Principal Engineer, Advanced Materials, Andy Mackie, Ph.D., MSc, will deliver a technical presentation on innovative solder bonding solutions for automotive and industrial applications at the Global Electronics A