-
- News
- Books
Featured Books
- smt007 Magazine
Latest Issues
Current IssueSupply Chain Strategies
A successful brand is built on strong customer relationships—anchored by a well-orchestrated supply chain at its core. This month, we look at how managing your supply chain directly influences customer perception.
What's Your Sweet Spot?
Are you in a niche that’s growing or shrinking? Is it time to reassess and refocus? We spotlight companies thriving by redefining or reinforcing their niche. What are their insights?
Moving Forward With Confidence
In this issue, we focus on sales and quoting, workforce training, new IPC leadership in the U.S. and Canada, the effects of tariffs, CFX standards, and much more—all designed to provide perspective as you move through the cloud bank of today's shifting economic market.
- Articles
- Columns
- Links
- Media kit
||| MENU - smt007 Magazine
Estimated reading time: 3 minutes
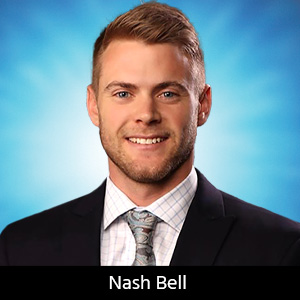
Knocking Down the Bone Pile: BGA and PCB Warpage—What to Do
Warpage of BGA packages or PCBs can occur when any heating and subsequent cooling cycle is gone through. This may leave the package to either bow in the middle. Pushing the corners up or downward will show up in bridging (caught on X-ray) or cause opens that would show up on endoscopic or visual inspection. If the PCB warps, then opens or shorts on a variety of other component areas may result.
Reasons for Problems
BGA and PCB warpage is a problem of material coefficient of thermal expansion (CTE) mismatch between the various packaging component materials, such as the substrate, silicon die, and EMC. The rate at which there are temperature increases can affect the temperature uniformity across the component during placement and removal, so this rate is indirectly correlated with warpage differences (Figure 1).
Figure 1: Opens due to BGA warpage.
Also, the larger the package, the greater chance of this warping phenomena with all other things being equal. Certainly, the type of rework heating method (hot air rework system, IR, hot air reflow oven, vapor phase oven, etc.) also has an impact. Using low-CTE thermal materials, it is possible to tailor CTE, partially or fully eliminating this problem. Some plastic bodied ball grid arrays (PBGAs) include a heat spreader, which causes the top of the BGA package to expand at a faster rate than the bottom of the BGA; this can pull the corners of the BGA down. Moisture in the BGA may also contribute to warpage as the component wants to spread in the middle. In these cases, the corners may curl upwards.
Through a series of design of experiments, you may want to confirm which part of the equation—the BGA or the PCB—is warping. Isolating which surface is doing the pulling and pushing will be useful in determining how to fix the problem.
How to Mitigate
Figure 2: Head-in-pillow defect.
For BGA warping, the corners will see the largest displacement, which can cause numerous opens and bridges to occur. Similarly, the circuit board can warp up or down and push into the solder paste, causing bridges or opens. These are caught either in visual or X-ray inspection. One of the methods to minimize warpage is to slow down your heating and cooling processes. You ramp up during your preheat section and cool down during your cooling section. Now, of course, in cooldown, you don’t want to go too slow because you don’t want to create a coarse-grained structure. As with many things in electronics manufacturing, it’s a trade-off.
Controlling MSD devices—including the boards and components—is another way to help mitigate the impact of warpage. The J-STD-0033 and JEDEC guidelines for moisture handling will be the best place to refer to for proper MSD handling. Prebaking of boards and components followed by keeping them in a dry environment will mitigate the problems if they are associated with moisture absorption. Limiting the exposure time and understanding the MSD level of the board and components will also go a long way to mitigating the warpage associated with moisture absorption. By using a solder paste that is formulated to reduce head-in-pillow and allows for the proper coalescing of the solder paste, solder ball warpage impacts will be limited as well (Figure 2).
Figure 3: Shadow moiré.
Through properly engineering the volume of solder paste deposited at each pad location, some of the problems related to PCB and device warpage can be limited. In some cases, overprinting some of the pads—while in other cases, underprinting other pads—may help compensate for the warpage impact. For example, where the BGA is bent inwards toward the PCB, there may be evidence of shorting. In those areas, the print volume may need to be minimized. Conversely, in areas where the BGA bends “away” from the board, a larger print volume may be the best solution.
If the board is warping (IPC-TM-650 2.4.22 test method for measuring bow and twist), then you may need to use other approaches to reduce the impact of device or board warpage (Figure 3). Besides the previously mentioned approaches, you may need to re-design the board to make sure the copper in the board is more evenly distributed. Low thermal mass (i.e., lower copper content) areas of the board will heat at different rates than higher thermal mass areas. In addition, very thin boards (0.020 inches) may need to laid out using a thicker board. Finally, different materials with closely matched CTEs may need to be used in the board or device construction.
Bob Wettermann is the principal of BEST Inc., a contract rework and repair facility in Chicago.
This article was published in the July 2019 issue of SMT007 Magazine.
More Columns from Knocking Down the Bone Pile
Knocking Down the Bone Pile: Addressing End-of-life Component Solderability Issues, Part 4Knocking Down the Bone Pile: Tin Whisker Mitigation in Aerospace Applications, Part 3
Knocking Down the Bone Pile: Gold Mitigation for Class 2 Electronics
Knocking Down the Bone Pile: Basics of Component Lead Tinning
Knocking Down the Bone Pile: Package on Package Rework—Skill Required
Knocking Down the Bone Pile: 2023’s Top Challenges in BGA Rework
Knocking Down the Bone Pile: Eliminating Solder Balls in Hand Soldering
Knocking Down the Bone Pile: Opening a Trace on the Surface of a PCB