-
- News
- Books
Featured Books
- pcb007 Magazine
Latest Issues
Current IssueThe Hole Truth: Via Integrity in an HDI World
From the drilled hole to registration across multiple sequential lamination cycles, to the quality of your copper plating, via reliability in an HDI world is becoming an ever-greater challenge. This month we look at “The Hole Truth,” from creating the “perfect” via to how you can assure via quality and reliability, the first time, every time.
In Pursuit of Perfection: Defect Reduction
For bare PCB board fabrication, defect reduction is a critical aspect of a company's bottom line profitability. In this issue, we examine how imaging, etching, and plating processes can provide information and insight into reducing defects and increasing yields.
Voices of the Industry
We take the pulse of the PCB industry by sharing insights from leading fabricators and suppliers in this month's issue. We've gathered their thoughts on the new U.S. administration, spending, the war in Ukraine, and their most pressing needs. It’s an eye-opening and enlightening look behind the curtain.
- Articles
- Columns
- Links
- Media kit
||| MENU - pcb007 Magazine
How Changing Cleaning Technologies Affect Reliability
July 22, 2019 | Andy Shaughnessy, I-Connect007Estimated reading time: 4 minutes
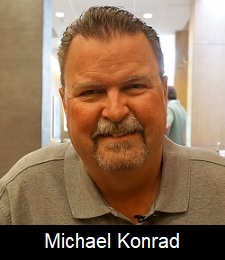
At the recent IPC High-Reliability Forum and Microvia Summit, Andy Shaughnessy spoke with Michael Konrad, founder and president of Aqueous Technologies and a speaker and panelist at the event in Baltimore, Maryland. They discussed Konrad’s presentation and the recent proliferation of cleaning, from solely high-reliability products to Class 1 consumer products.
Andy Shaughnessy: Good to see you, Michael. Can you start by telling us about your upcoming presentation?
Michael Konrad: I’ll be talking about the factors that influence the reduction in residue tolerance on circuit assemblies. Historically, circuit assemblies were—almost without exception—cleaned after solder and reflow. With the introduction of the Montreal Protocol and a ban on the cleaning solvents that were used to remove the containment species from the circuit assemblies, the majority of the industry switched to no-clean technologies. The hope was that this would eliminate the need for cleaning, and it largely did for a long time.
Now, due to miniaturization and very minimal—if any—gaps between the bottom of the component and the top of the board, the amount of tolerable residue has shrunk on assemblies to the point where now most assemblies are cleaned again. It’s an evolution.
I’ll also be introducing the new IPC J-STD-001 Amendment 1 change to the cleanliness testing requirements of the J-Standard as the way the industry has responded to the sudden need for cleaning again and the consequential need to test for cleanliness.
Shaughnessy: What’s the change with that standard?
Konrad: Much of the change has to do with resistivity of solvent extract (ROSE) testing, which was the predominant method of testing cleanliness for the last 30–40 years. But ROSE testing isn’t going away; it’s going to be used more. What is going away is the historical pass-fail limit that was associated with the ROSE test. ROSE testers were used to determine pass or fail, clean or dirty; now, they’re going to monitor process control and provide validation. The pass-fail method was designed in the ‘70s when the Bee Gees were on the radio every other song. I’m glad we’re not in the ‘70s anymore for a number of reasons, but the standard we’ve been using until last October was established in the ‘70s. Boards, of course, have changed dramatically since then.
Shaughnessy: You used IoT as an example of electronics now being in environments that are new and nontraditional. Can you talk about some of the contamination effects?
Konrad: It’s not often that we are in a revolutionary moment. Usually, we’re in an evolution, but now, the revolution of electronics has allowed us to largely take consumer goods and throw them into harsh environments. We’re putting electronics into smart electrical meters that are in harsh environments outside of hundreds of millions of homes. We’re putting electronics in toothbrushes and refrigerators and accelerometers in footballs and tennis rackets. All of these things experience harsh environmental conditions. Whenever the temperature or humidity increases, the amount of residue tolerance decreases. With what would normally be Class 1 electronics—which really have no high expectation of reliability—we’re throwing them outside and causing them to fail.
The explosion of IoT—and taking electronic components and assemblies and putting them in places where we traditionally have not had them—is creating a need to remove residues more than it would have before. Normally, we remove residues if somebody is going to die if the component or the assembly fails. That’s considered a high-reliability requirement; we clean so we don’t kill people. Now, a lot of consumer goods—even Class 1 consumer goods—are being cleaned because it will create a better reputation for the manufacturer. For example, the failure of an electronic flea collar will not kill anyone; you just have an itchy dog. We’re seeing a lot of things being cleaned that historically—at least in the last 30 years—were not.
Shaughnessy: Are you talking about contamination during manufacture that presents once the product is deployed?
Konrad: Yes. Ionic contamination, specifically, is not an issue unless it’s merged with moisture and electrical current. Three factors work together to produce electrochemical migration, which has a number of knock-on fatal effects on an assembly: ionic residue, moisture, and electrical current. Remove any one of those three, and you solve the problem. If the power is turned off, electrochemical migration won’t occur. Prevent the assembly from ever coming into contact with moisture, and we can leave residue on the assembly. In most cases, however, we really can’t prevent moisture from ever contacting the assembly. And we certainly can’t suggest our customers turn off their products to improve reliability, so what's left is to remove the residue.
To read the full article, which appeared in the July 2019 issue of PCB007 Magazine, click here.
Suggested Items
SHENMAO Strengthens Semiconductor Capabilities with Acquisition of PMTC
07/10/2025 | SHENMAOSHENMAO America, Inc. has announced the acquisition of Profound Material Technology Co., Ltd. (PMTC), a premier Taiwan-based manufacturer of high-performance solder balls for semiconductor packaging.
KYZEN to Highlight Understencil and PCB Cleaners at SMTA Querétaro Expo and Tech Forum
07/09/2025 | KYZEN'KYZEN, the global leader in innovative environmentally responsible cleaning chemistries, will exhibit at the SMTA Querétaro Expo & Tech Forum, scheduled to take place Thursday, July 24, at Centro de Congresos y Teatro Metropolitano de Querétaro.
Driving Innovation: Direct Imaging vs. Conventional Exposure
07/01/2025 | Simon Khesin -- Column: Driving InnovationMy first camera used Kodak film. I even experimented with developing photos in the bathroom, though I usually dropped the film off at a Kodak center and received the prints two weeks later, only to discover that some images were out of focus or poorly framed. Today, every smartphone contains a high-quality camera capable of producing stunning images instantly.
Hands-On Demos Now Available for Apollo Seiko’s EF and AF Selective Soldering Lines
06/30/2025 | Apollo SeikoApollo Seiko, a leading innovator in soldering technology, is excited to spotlight its expanded lineup of EF and AF Series Selective Soldering Systems, now available for live demonstrations in its newly dedicated demo room.
Indium Corporation Expert to Present on Automotive and Industrial Solder Bonding Solutions at Global Electronics Association Workshop
06/26/2025 | IndiumIndium Corporation Principal Engineer, Advanced Materials, Andy Mackie, Ph.D., MSc, will deliver a technical presentation on innovative solder bonding solutions for automotive and industrial applications at the Global Electronics A