-
- News
- Books
Featured Books
- pcb007 Magazine
Latest Issues
Current IssueInventing the Future with SEL
Two years after launching its state-of-the-art PCB facility, SEL shares lessons in vision, execution, and innovation, plus insights from industry icons and technology leaders shaping the future of PCB fabrication.
Sales: From Pitch to PO
From the first cold call to finally receiving that first purchase order, the July PCB007 Magazine breaks down some critical parts of the sales stack. To up your sales game, read on!
The Hole Truth: Via Integrity in an HDI World
From the drilled hole to registration across multiple sequential lamination cycles, to the quality of your copper plating, via reliability in an HDI world is becoming an ever-greater challenge. This month we look at “The Hole Truth,” from creating the “perfect” via to how you can assure via quality and reliability, the first time, every time.
- Articles
- Columns
- Links
- Media kit
||| MENU - pcb007 Magazine
A Guide to High-reliability PCBs from Design to Specification
July 24, 2019 | Jeff Beauchamp, NCAB GroupEstimated reading time: 3 minutes
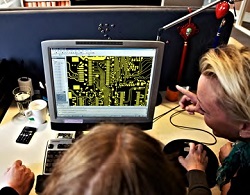
In our daily lives, we constantly interact with electronic products, and all of these products contain a printed circuit board (PCB). Because the PCB serves as the interconnect for all the various components required for the electronic system to function reliably, it is often referred to as the key component.
Thus, it comes as no surprise that PCB reliability is a critical factor right from the start of the PCB production process. If a PCB has a reliability issue, the end product itself is at risk. The important thing is getting it right the first time. Trying to improve reliability once the product is designed and in production can lead to massively high costs for the product owner. In some cases, such as medical equipment or motor vehicles, it could even become a matter of life or death.
Creating reliable PCBs is an outcome of considering all aspects that can affect reliability as early as possible in the design process. The further down the design process, the more expensive and risky it can be to fix. Because its design has been tailored to a specific function and application, you can’t compare a PCB to other components. As a custom component, the PCB’s role is critical. A good board design improves the reliability of the end product and lessens the risk of failure. Furthermore, as technology advances, design solutions become increasingly complex, which requires more comprehensive planning in terms of design and manufacturing. It follows, of course, that the more complex the function of the PCB, the more complex both construction and manufacturing becomes.
Important Features
The following list highlights the 14 most important features for designing and producing a reliable PCB as seen by NCAB Group. Note that some of these features are not included in IPC standards, but NCAB finds these particular constraints to be critical. IPC standards are guidelines for the industry, but they are not always comprehensive in terms of producing the most robust board feasible. For high-reliability and/or high-technology circuit boards, guidelines usually need to exceed IPC standards to increase performance and lifetime.
1. 25-micron nominal hole plating per IPC Class 3
2. No track welding or open circuit repair
3. Cleanliness requirements beyond those of IPC
4. Tight control on the age of specific finishes
5. Internationally known base material types used—no local or unknown brands allowed
6. Tolerance for copper-clad laminate is IPC-4101 Class B/L
7. Defined solder mask, ensuring accordance to IPC-SM-840 class T
8. Defined tolerances for profile, holes, and other mechanical features
9. Specific solder mask thickness (IPC does not require this)
10. Defined cosmetic and repair requirements (IPC does not require this)
11. Tighter requirements for the depth of via fill (IPC requires 60%, but we require at least 70%)
12. Peters SD2955 peelable as standard
13. Specific qualification-and-release process for every purchase order
14. No X-outs accepted
At the same time, boards should be designed in a way that they can be manufactured reliably by as many factories as possible. The extra investment in thought up front gives the product better lead times overall while maintaining quality.
Applying the very latest technology required by the component manufacturers often only increases the challenge level. For example, if you can avoid BGA escape routes that use six or seven different layers of blind or buried vias and reduce it to a standard multilayer board, it’s a good idea to do so. Reduced layer counts do away with all of the extra drilling and plating processes, significantly reducing costs while also improving the manufacturability of the product. By keeping manufacturing options as open as possible through smart design, this will allow easier switching from one production facility to another. Further, this reduces the design’s overall supply chain risks. If one factory, for example, is underperforming or dealing with a technical issue, production could more easily move to another facility. The riskiest PCB design is one that is limited to a single factory’s unique processes.
Data and Documentation
But there is more to reliability than just the manufacturing process or careful design practice. Reliability is achieved through the mindset that plans the entire process from design through delivery. Therefore, it is critical that complete and concise information, build notes, and instructions are provided to your PCB supplier and that the partner demonstrably puts quality first. Look for a partner with a seamless approach that will take the project from prototype manufacturing to production manufacturing without sacrificing quality or reliability. Design teams do their part in this reliability process by creating a complete and detailed manufacturing package.
To read the full article, which appeared in the July 2019 issue if PCB007 Magazine, click here.
Testimonial
"We’re proud to call I-Connect007 a trusted partner. Their innovative approach and industry insight made our podcast collaboration a success by connecting us with the right audience and delivering real results."
Julia McCaffrey - NCAB GroupSuggested Items
Dr. Jennie Hwang to Present on ‘Solder Joint Reliability’ at SMTA International 2025
09/03/2025 | Dr. Jennie HwangDr. Jennie Hwang to address “Solder Joint Reliability” at the 2025 SMTA International Conference on Monday, October 20. Leveraging her decades of extensive real-world experiences and deep knowledge,
Indium to Highlight Energy-Efficient, High-Reliability Solder Solutions for EV and Electronics at Productronica India
09/03/2025 | Indium CorporationIndium Corporation, a leading materials refiner, smelter, manufacturer, and supplier to the global electronics, semiconductor, electric vehicle (EV), thin-film, and thermal management markets, will feature a range of sustainable, high-reliability solder products at Productronica India, to be held September 17-19 in Bengaluru, India.
Altus Supports Datalink Electronics with Advanced Selective Soldering Solution to Boost Manufacturing Efficiency
09/02/2025 | Altus GroupDatalink Electronics has partnered with Altus Group to integrate a cutting-edge automated soldering solution, enhancing its production capabilities and reinforcing its strategic focus on quality, automation, and scalability.
Connect the Dots: How to Avoid Five Common Causes of Board Failure
09/03/2025 | Matt Stevenson -- Column: Connect the DotsBoards fail for various reasons, and because I’ve been part of the PCB industry for a long time, I’ve seen most of the reasons for failure. As part of my ongoing crusade to help designers design for the reality of manufacturing, here are five common causes for board failure and how to avoid them.
More Than a Competition: Instilling a Champion's Skill in IPC Masters China 2025
09/01/2025 | Evelyn Cui, Global Electronics Association—East AsiaNearly 500 elite professionals from the electronics industry, representing 18 provinces and municipalities across China, competed in the 2025 IPC Masters Competition China, March 26–28, in Pudong, Shanghai. A total of 114 contestants advanced to the practical competition after passing the IPC Standards Knowledge Competition. Sixty people competed in the Hand Soldering and Rework Competition (HSRC), 30 in the Cable and Wire Harness Assembly Competition (CWAC), and 24 in the Ball Grid Array/Bottom Termination Components (BGA/BTC) Rework Competition.