-
- News
- Books
Featured Books
- smt007 Magazine
Latest Issues
Current IssueWhat's Your Sweet Spot?
Are you in a niche that’s growing or shrinking? Is it time to reassess and refocus? We spotlight companies thriving by redefining or reinforcing their niche. What are their insights?
Moving Forward With Confidence
In this issue, we focus on sales and quoting, workforce training, new IPC leadership in the U.S. and Canada, the effects of tariffs, CFX standards, and much more—all designed to provide perspective as you move through the cloud bank of today's shifting economic market.
Intelligent Test and Inspection
Are you ready to explore the cutting-edge advancements shaping the electronics manufacturing industry? The May 2025 issue of SMT007 Magazine is packed with insights, innovations, and expert perspectives that you won’t want to miss.
- Articles
- Columns
- Links
- Media kit
||| MENU - smt007 Magazine
IPC High-reliability Forum and Microvia Summit Review, Part II
August 6, 2019 | Pete Starkey, I-Connect007Estimated reading time: 8 minutes
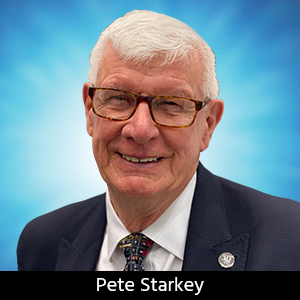
Editor’s Note: Click here to read Part I.
The Microvia Summit on May 16 was a special feature of the 2019 event, since microvia challenges and reliability issues have become of great concern to the PCB manufacturing industry. It provided updates on the work of members of the IPC V-TSL-MVIA Weak Interface Microvia Failures Technology Solutions Subcommittee and opportunities to learn about latest developments in methods to reveal and explain the presence of latent defects, identify causes and cures, and be able to consistently and confidently supply reliable products.
Dr. Michael H. Azarian of CALCE at the University of Maryland explored the effects of design and manufacturing factors on the reliability of microvia interconnects, discussing the relative strengths and weaknesses of blind, buried, isolated, staggered, and stacked microvias in HDI circuits. He stressed this point, “What looks like a relatively simple structure is actually associated with a vast number of design and process parameters that can impact reliability.”
Azarian began by considering quality issues associated with microvia filling by electrolytic copper plating. Incomplete filling or voiding could degrade reliability through localised stress concentration reducing fatigue life. He then showed several examples of corner cracks, barrel cracks, and interface separation, some attributed to inadequate process control, some to brittle fracture of the electroless copper.
Also, Azarian used finite element analysis to help determine the effects of microvia defects and process parameters on microvia lifetime, using fatigue modelling to simulate a series of solder reflow cycles followed by thermal cycling. He commented that the total strain range of the first solder reflow cycle was much larger than that of the second and third cycles due to work hardening of the copper. Fatigue life was affected by the size and shape of voids, and Azarian observed that small spherical voids actually increased the fatigue life, whereas for conical voids, the fatigue life decreased with the void size. Microvia aspect ratio also affected fatigue life when voids were present, and for a given conical void shape and volume ratio, the smaller the aspect ratio, the longer the microvia fatigue life. CALCE developed a second-order regression model to predict the cycles to failure of copper-filled stacked microvias under thermal loading and used finite element modelling for fracture analysis
Then, Azarian highlighted some of the challenges involved in microvia testing and the detection of delamination and cracking, particularly at the early stages of degradation. Advantage had been taken of the high-frequency skin effect to monitor interconnect degradation by observing changes in RF impedance. And time-domain reflectometry at high frequencies provided a further route to the early detection of interconnect failure.
Lance Auer from Conductor Analysis Technologies reported highlights from IPC committee meetings at IPC APEX EXPO 2019 and the movement towards performance-based acceptance testing for microvia reliability. He commented on the shortcomings of testing to existing IPC 6010-series specifications, which often did not identify the failures. There had been many examples of failures after passing all testing requirements, observed at in-circuit test after reflow, at environmental stress screening during box-level assembly, or in the field by the end customer. And traditional microsection techniques were not always capable of detecting many of these defects.
The IPC V-TSL-MVIA Weak Interface Microvia Failures Technology Solutions Subcommittee reported its findings during an open forum at IPC APEX EXPO 2019. In response, IPC issued a warning statement about post-fabrication microvia failures occurring during reflow but remaining undetectable at room temperature.
Several OEMs had been successfully screening lots with D-coupon testing per Method 2.6.27 Appendix A of IPC-TM-650, and IPC was moving away from traditional microsection evaluation towards performance-based acceptance testing. Reflow simulation testing for structural integrity during thermal stress was being added into the IPC-6012E qualification and performance specification for rigid printed boards.
Auer summarised the recommendations for performance-based acceptance testing agreed at the APEX 2019 committee meetings. He demonstrated the thermal profiles for reflow simulation and thermal shock testing and showed examples of change-in-resistance measurements corresponding to microvia failures. The suggested drawing notes described the design of IPC D-coupons, the number to be tested per manufacturing panel, the conditions for reflow simulation and acceptance criteria for change in resistance, the conditions for thermal shock and acceptance criteria for change in resistance, and the reporting of results.Page 1 of 2
Suggested Items
Driving Innovation: Direct Imaging vs. Conventional Exposure
07/01/2025 | Simon Khesin -- Column: Driving InnovationMy first camera used Kodak film. I even experimented with developing photos in the bathroom, though I usually dropped the film off at a Kodak center and received the prints two weeks later, only to discover that some images were out of focus or poorly framed. Today, every smartphone contains a high-quality camera capable of producing stunning images instantly.
Hands-On Demos Now Available for Apollo Seiko’s EF and AF Selective Soldering Lines
06/30/2025 | Apollo SeikoApollo Seiko, a leading innovator in soldering technology, is excited to spotlight its expanded lineup of EF and AF Series Selective Soldering Systems, now available for live demonstrations in its newly dedicated demo room.
Indium Corporation Expert to Present on Automotive and Industrial Solder Bonding Solutions at Global Electronics Association Workshop
06/26/2025 | IndiumIndium Corporation Principal Engineer, Advanced Materials, Andy Mackie, Ph.D., MSc, will deliver a technical presentation on innovative solder bonding solutions for automotive and industrial applications at the Global Electronics A
Fresh PCB Concepts: Assembly Challenges with Micro Components and Standard Solder Mask Practices
06/26/2025 | Team NCAB -- Column: Fresh PCB ConceptsMicro components have redefined what is possible in PCB design. With package sizes like 01005 and 0201 becoming more common in high-density layouts, designers are now expected to pack more performance into smaller spaces than ever before. While these advancements support miniaturization and functionality, they introduce new assembly challenges, particularly with traditional solder mask and legend application processes.
Knocking Down the Bone Pile: Tin Whisker Mitigation in Aerospace Applications, Part 3
06/25/2025 | Nash Bell -- Column: Knocking Down the Bone PileTin whiskers are slender, hair-like metallic growths that can develop on the surface of tin-plated electronic components. Typically measuring a few micrometers in diameter and growing several millimeters in length, they form through an electrochemical process influenced by environmental factors such as temperature variations, mechanical or compressive stress, and the aging of solder alloys.