-
- News
- Books
Featured Books
- pcb007 Magazine
Latest Issues
Current IssueInventing the Future with SEL
Two years after launching its state-of-the-art PCB facility, SEL shares lessons in vision, execution, and innovation, plus insights from industry icons and technology leaders shaping the future of PCB fabrication.
Sales: From Pitch to PO
From the first cold call to finally receiving that first purchase order, the July PCB007 Magazine breaks down some critical parts of the sales stack. To up your sales game, read on!
The Hole Truth: Via Integrity in an HDI World
From the drilled hole to registration across multiple sequential lamination cycles, to the quality of your copper plating, via reliability in an HDI world is becoming an ever-greater challenge. This month we look at “The Hole Truth,” from creating the “perfect” via to how you can assure via quality and reliability, the first time, every time.
- Articles
- Columns
- Links
- Media kit
||| MENU - pcb007 Magazine
Estimated reading time: 7 minutes
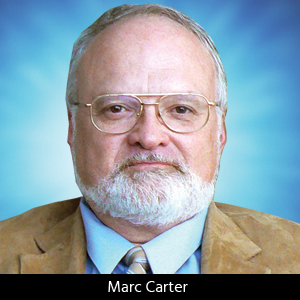
Contact Columnist Form
Better to Light a Candle: Chapter Four—Next Steps for Developing the Future Workforce
Editor’s Note: This column is part of a series on a new university course in PCB manufacturing at Michigan Technological University. Marc will chronicle the progress of this class, interview the guest lecturers, introduce the students, etc.
In my first column, I introduced the PCB fabrication course at Michigan Technological University to prepare the next generation of PCB experts. In my second update, I shared some participating student’s thoughts via a recorded interview on their experience. In the third installment, I acknowledged the contributions of many organizations and individuals that willingly and freely contributed their time, materials, and support to make this first “prototype” effort a success.
This fourth issue will give the prospects and status of repeat (perhaps even expanded) classes at Michigan Tech, report on developing contacts at other prospective university, industry, and government nodes for similar efforts to ensure basic printed circuit technology familiarity of college graduates over the next few years. It will also include a blatant call to action on the part of our industry to step up and provide the more substantive corporate-level support needed to put this effort on a sustainable basis, and to replicate that prototype across the Americas.
Background
The effort at Michigan Tech addressed one small aspect (shortage of replacement printed circuit engineers over the next few years) of a much larger issue (i.e., the complex and long-term current and projected shortfalls in the workforce, skill sets, and capabilities in electronics manufacturing generally).
This kind of local industry-academia partnership should be considered as only one element of a holistic, multiple-path system of workforce development options, beginning with introductory “technology can be cool” programs in K–8. Some examples include STEM/CTE (Certified Technical Education) programs in high schools, technical certificates, and associate degree programs in the field as well as full engineering degree programs.
If technology manufacturing in general, and electronics manufacturing specifically, is to remain viable in North America as a part of what some people are calling the Fourth Industrial Revolution, you and I (not the government or “somebody else”) need to do what we can, where we can, to enable, support, and participate in programs that develop a future workforce that meets the needs of Factory 4.0 versions of electronics manufacturing. Everything from design, through fabrication, assembly, and test will require an understanding of the basic traditional processes, but will be increasingly implemented by automation, robotics, artificial intelligence, and interconnected “smart” tools and processes. We don’t need just new designers, lab technicians, drill operators, and process engineers. The knowledge and experience “cliff” that’s been reported means we need all of those functions but to a greater degree by automation programmed, monitored, and overseen by humans rather than machines operated directly by humans.
It has been painfully obvious to the declining number of “board rats” (with a nod to Steve Williams’ I-Connect007 column from May 2017 [1]) that the knowledge, experience, and capabilities needed by electronics manufacturing were at risk, and high-level recognition and support were intermittent (or absent). Fortunately, there are indications that high-level corporate and government circles are beginning to evidence some recognition of the problem is (it is perhaps belated, and as much politically motivated as not, but we’ll take what we can get, won’t we, rats?).
As reported on July 23, 2019, a three-way discussion between the acting administrator of the U.S. Small Business Administration, Calumet Electronics employees, and representatives of Michigan Tech took place at Calumet [2]. This was followed by a larger industry, government, and academia roundtable in Houghton, Michigan with industry professionals, senior Michigan Tech administration, Administrator Pilkerton of the SBA, and IPC staff.
On July 25, industry representatives—including Audra Thurston, one of the remote participants in this year’s Michigan Tech classes—attended a White House event marking the first anniversary of an Executive Order mandating expansion of the U.S. skilled workforce. It's a good start, but much work remains.
Status of the Michigan Tech Effort and Potential Additional Universities
This fledgling effort is at a crossroads. Volunteer support as well as companies donating SME time and surplus consumables, out-of-pocket funding, bits and pieces of vintage lab-scale equipment scattered across three buildings, and lots and lots of sweat got this Michigan Tech “proof of concept” effort through the first year. As measured by the student feedback, it was successful on a small-scale. The amount of work/time put into starting and running that design, build, assembly, and test class with minimal installed infrastructure and one “champion” was adequate for the concept demonstration, but is not a sustainable, permanent solution. “Plucky underdog” is an attractive concept, but tougher to sustain in the wider world on a shoestring.
On July 17, 2019, in a meeting at Calumet, representatives of the industry, volunteers supporting last spring’s class, and Michigan Tech had a frank and realistic discussion comparing the relative success of the “prototype/proof of concept” test vs. limited tangible evidence of support from the wider board fabrication industry. Plexus has stepped up with serious support for a sustainable assembly operation, and Altium has enabled design workstations and training. Calumet Electronics has done more than its share, but wider industry corporate-level support from the fabrication side is needed to make this sustainable.
Other universities have expressed some cautious interest, but thus far, appear to have taken a “wait and see” attitude, seeing if local electronic manufacturing industries are willing to seriously support a similar effort. A part of that “wait and see” attitude may involve watching to see whether the first-year success at Michigan Tech can be repeated.
Next Steps
If the North American electronics manufacturing industry, particularly on the fabrication side, is truly serious about providing more than a one-shot demonstration of a resource to ensure near-term (1–5 years) availability of a minimally familiar workforce, more substantive support is needed. We’ve all attended conferences, workshops, legislature outreach sessions, etc., where we, representing the industry, have wrung our collective hands over the “dire consequences” predicted due to the current and imminent retirement of the few industry veterans that remain after decades of downsizing. So, let’s do something about it.
STEM (at the elementary, junior high, and high school levels) is a fine and needed effort and deserves our support, but is a long-term investment (a decade or so) for skilled replacement workforce [1]. If your organization is concerned about a skilled future workforce (locally or at the corporate level, and it’s hard to imagine how it could not [3]), organize your resources.
Large, multi-site organizations may have a person (or persons) at the corporate level tasked (and resourced) with workforce development or university outreach, and some of their individual manufacturing locations are near an engineering university, two- or four-year technical college, etc. Those sites will be in the best position to coordinate with the local educational entity to define and develop the right programs. It’s important to stress to the educational community the career advantage it offers their graduates as well as your organization’s commitment. It’s also a great community relations/news release opportunity. The estimated $100–200k needed to make a named, sustainable showcase printed circuit fabrication facility at Michigan Tech would be good press.
Smaller, single-site manufacturing operations may be able to combine their resources through their industry organization(s), their state workforce development agency, and depending on the local situation, in a burden-sharing scheme.
In any case, communicating the needs and support of the local industry to the education organization is critical. They are presented with multiple needs and have finite staff and physical resources, and will apportion those resources based on the perception of need and prospects of industry support.
For further information, you can reach Dr. Chris Middlebrook at ctmiddle@mtu.edu or me at pmcarter01@gmail.com.
References
- S. Williams, “Finding the Next Generation of ‘Board Rats,’” The PCB Magazine, May 2017.
- IPC, “U.S. SBA Chief Praises IPC Member Calumet Electronics,” July 23, 2019.
- IPC, “Findings on the Skills Gap in U.S. Electronics Manufacturing “Bannockburn, Illinois., pp. 7–9, Appendices A & B, 2017.
Marc Carter has worked in the electronics interconnection industry since 1984 in a variety of roles in fabrication and assembly materials, processes, environmental compliance, and supply chain management activities around the world. He has had the honor and privilege of working with and learning from many of the true giants of this industry in multiple functions over many years. His experience includes a major mil-aero OEM, field and development work at materials suppliers to the printed circuit industry, and an educational stint as the sole proprietor of a manufacturer’s agency representing multiple high-tech mil-aero material suppliers.
More Columns from Better to Light a Candle
Better to Light a Candle: A Solid Training Ground in New HampshireBetter to Light a Candle: Chapter 12—Light at the End of the COVID Tunnel
Better to Light a Candle: Chapter 11—Expanding and Adapting in the Face of the Pandemic
Better to Light a Candle: Chapter 10—Expanding the Base and Building the New
Better to Light a Candle: Chapter Nine—Growing Interest Around the Country
Better to Light a Candle: Chapter 8—Expanding the Model in This New Reality
Better to Light a Candle: Chapter Seven—Coping With COVID-19
Better to Light a Candle: Chapter Six—Spreading the Word