-
- News
- Books
Featured Books
- smt007 Magazine
Latest Issues
Current IssueSupply Chain Strategies
A successful brand is built on strong customer relationships—anchored by a well-orchestrated supply chain at its core. This month, we look at how managing your supply chain directly influences customer perception.
What's Your Sweet Spot?
Are you in a niche that’s growing or shrinking? Is it time to reassess and refocus? We spotlight companies thriving by redefining or reinforcing their niche. What are their insights?
Moving Forward With Confidence
In this issue, we focus on sales and quoting, workforce training, new IPC leadership in the U.S. and Canada, the effects of tariffs, CFX standards, and much more—all designed to provide perspective as you move through the cloud bank of today's shifting economic market.
- Articles
- Columns
- Links
- Media kit
||| MENU - smt007 Magazine
BTU International to Highlight Vacuum Reflow at SMTAI
August 20, 2019 | BTU International, Inc.Estimated reading time: 1 minute
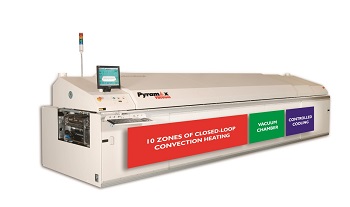
BTU International, Inc. will exhibit at SMTA International, scheduled to take place September 24-25, 2019 at the Stephens Convention Center in Rosemont, Illinois. The company will highlight its PYRAMAX Vacuum reflow oven in booth #816.
BTU has made the PYRAMAX Vacuum available for demonstration and product development by stationing a unit at ACI Technologies in Philadelphia, PA. At ACI customers can not only operate the vacuum reflow oven, but have access to the required process equipment and metrology as well.
The PYRAMAX Vacuum reflow oven has been designed around the requirements of large EMS/high-volume automotive customers. The unit is configured with 10 zones of closed-loop convection heating and a maximum production width of 18". Nitrogen atmosphere capable, the PYRAMAX Vacuum reflow oven offers a maximum process temperature of 350°C.
The unit features integrated controls with BTU’s proprietary Wincon Windows-based control system and full integration with factory MES/Industry 4.0 including the vacuum parameters. Additional features include:
- Automatic sequencing
- Programmable control of vacuum level and hold time
- Pass-through mode for non-vacuum operation
Existing PYRAMAX customers can easily transfer their process to the new PYRAMAX Vacuum reflow oven.
About BTU International
BTU International, a wholly-owned subsidiary of Amtech Group (Nasdaq: ASYS), is a global supplier and technology leader of advanced thermal processing equipment in the electronics manufacturing market. BTU’s high-performance reflow ovens are used in the production of SMT printed circuit board assemblies and in semiconductor packaging processes. BTU also specializes in precision controlled, high-temperature belt furnaces for a wide range of custom applications, such as brazing, direct bond copper (DBC), diffusion, sintering and advanced solar cell processing. BTU has operations in North Billerica, Massachusetts, and Shanghai, China, with direct sales and service in the U.S.A., Asia and Europe. Information about BTU International is available at www.btu.com.
Testimonial
"Our marketing partnership with I-Connect007 is already delivering. Just a day after our press release went live, we received a direct inquiry about our updated products!"
Rachael Temple - AlltematedSuggested Items
How Good Design Enables Sustainable PCBs
08/21/2025 | Gerry Partida, Summit InterconnectSustainability has become a key focus for PCB companies seeking to reduce waste, conserve energy, and optimize resources. While many discussions on sustainability center around materials or energy-efficient processes, PCB design is an often overlooked factor that lies at the heart of manufacturing. Good design practices, especially those based on established IPC standards, play a central role in enabling sustainable PCB production. By ensuring designs are manufacturable and reliable, engineers can significantly reduce the environmental impact of their products.
50% Copper Tariffs, 100% Chip Uncertainty, and a Truce
08/19/2025 | Andy Shaughnessy, I-Connect007If you’re like me, tariffs were not on your radar screen until a few months ago, but now political rhetoric has turned to presidential action. Tariffs are front-page news with major developments coming directly from the Oval Office. These are not typical times. President Donald Trump campaigned on tariff reform, and he’s now busy revamping America’s tariff policy.
Global PCB Connections: Understanding the General Fabrication Process—A Designer’s Hidden Advantage
08/14/2025 | Markus Voeltz -- Column: Global PCB ConnectionsDesigners don’t need to become fabricators, but understanding the basics of PCB fabrication can save you time, money, and frustration. The more you understand what’s happening on the shop floor, the better you’ll be able to prevent downstream issues. As you move into more advanced designs like HDI, flex circuits, stacked vias, and embedded components, this foundational knowledge becomes even more critical. Remember: the fabricator is your partner.
MKS’ Atotech to Participate in IPCA Electronics Expo 2025
08/11/2025 | AtotechMKS Inc., a global provider of enabling technologies that transform our world, announced that its strategic brands ESI® (laser systems) and Atotech® (process chemicals, equipment, software, and services) will showcase their latest range of leading manufacturing solutions for printed circuit board (PCB) and package substrate manufacturing at the upcoming 17th IPCA Show to be held at Pragati Maidan, New Delhi from August 21-23, 2025.
MKS Showcases Next-generation PCB Manufacturing Solutions at the Thailand Electronics Circuit Asia 2025
08/06/2025 | MKS Instruments, Inc.MKS Inc, a global provider of enabling technologies that transform our world, today announced its participation in Thailand Electronics Circuit Asia 2025 (THECA 2025), taking place August 20–22 at BITEC in Bangkok.