-
- News
- Books
Featured Books
- design007 Magazine
Latest Issues
Current IssueProper Floor Planning
Floor planning decisions can make or break performance, manufacturability, and timelines. This month’s contributors weigh in with their best practices for proper floor planning and specific strategies to get it right.
Showing Some Constraint
A strong design constraint strategy carefully balances a wide range of electrical and manufacturing trade-offs. This month, we explore the key requirements, common challenges, and best practices behind building an effective constraint strategy.
All About That Route
Most designers favor manual routing, but today's interactive autorouters may be changing designers' minds by allowing users more direct control. In this issue, our expert contributors discuss a variety of manual and autorouting strategies.
- Articles
- Columns
- Links
- Media kit
||| MENU - design007 Magazine
Estimated reading time: 3 minutes
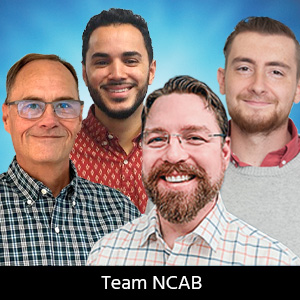
Fresh PCB Concepts: Qualities of Medically Applied PCBs
At NCAB Group, we receive many questions regarding the applications of our PCBs. Where are they used? How does that affect the designs? How is the board produced to meet the demands? Can anyone make such boards?
In this inaugural column, I will discuss details of PCBs used in medical applications, highlighting some of the differences in terms of demands and how the design must be handled.
We have seen electronics become increasingly significant in the medical field. Advancements in medical technology have provided dramatically improved diagnostics and treatments for patients.
Look at how the da Vinci Surgical System has helped to offer the ability of some of the world’s most skilled surgeons irrespective of their proximity to the patient.
Technical developments in research tools now allow scientists to examine diseases on a molecular level and provide vaccines that the WHO estimates saves around 3 million lives per year. Such technological development in medical electronics will only continue to grow, and we know that this also means the need for more complex PCBs will track accordingly.
Some examples of where PCBs are used in medical applications include:
- Electronic scales
- Electric wheelchairs
- Electron microscopes
- Monitoring instruments
- CT scanning systems
- X-ray machines
- Pacemakers
- Artificial heart valves
As you can see from this list, there are various categories of medical devices, ranging from what could be considered standard to the very complex. These medical applications can be grouped into three different categories.
Class 1: General Medical Equipment
These products are seen as low risk in that while they will be used for medical purposes, they are not likely to cause personal injuries. Some examples of these products include patient scales, gloves, gauges, and dental mirrors.
Class 2: Instruments With Risk
These products carry a higher risk than Class 1 products but are limited to operational and maintenance risks. Examples include electric wheelchairs and monitoring instruments.
Class 3: Life-sustaining Devices
These products are life-critical and must be produced in accordance with the highest standards so that reliability is ensured as unplanned device downtime cannot be tolerated. Some examples of these products are pacemakers and heart valves.
Continuing with the theme of standards, we know that medical devices have to meet certain criteria and adhere to specific standards, be this in design, function, production, quality system, etc. Examples of some of the different key criteria and associated standards are shown in Table 1.
It is also important to consider how these standards translate directly into demands or considerations that can be placed directly upon the design of the PCB (Table 2).
After looking at the design elements, consideration must be given to the manufacturing elements that correspond to medical applications. These elements can have a direct influence on the acceptance of the circuit board as well as the reliability of the product whilst in the field. When it comes to safety, the elements in Table 3 are crucial.
In addition to these elements, NCAB Group also calls out for the following elements in our specification:
- Cleanliness requirements which beyond those of IPC
- Internationally known base material types (we do not accept or allow local or unknown brands)
- Specific solder mask thickness demands for both the surface of the boards and also on the surface of the conductors
- Defined cosmetic and repair requirements (no open circuit repair and a limited number of cosmetic repairs)
- Tighter requirements for the depth of via fill when type VI solder mask demands are called for, which are above industry standards
The certification associated with these quality standards is ISO 13485, which serves as a regulatory or legal requirement in many countries and will ensure the use of best practices throughout all steps of a medical device’s lifecycle. ISO 13485 is largely consistent with ISO 9001. Organizations that possess this certification can be involved in one or more stages of the lifecycle, including design and development, production, storage and distribution, installation, or servicing of a medical device and design and development or provision of associated activities (like technical support).
PCB designs for medical applications will have specific elements that cover demands for power, signal quality, crosstalk, and grounding. But the most important aspects are reliability and safety.
Safety must be upheld in all areas, including radiation, electrical, thermal, and mechanical safety. This is all driven by IPC Class 3 standards; therefore, it is crucial to have manufacturing facilities that are proven in terms of achieving these demands and supplying reliable circuit boards for medical applications.
Alifiya Arastu is a field application engineer at NCAB Group.
More Columns from Fresh PCB Concepts
Fresh PCB Concepts: Designing for Success at the Rigid-flex Transition AreaFresh PCB Concepts: More Than Compliance—A Human-centered Sustainability Approach
Fresh PCB Concepts: Assembly Challenges with Micro Components and Standard Solder Mask Practices
Fresh PCB Concepts: The Power of a Lunch & Learn for PCB Professionals
Fresh PCB Concepts: Key Considerations for Reliability, Performance, and Compliance in PCBs
Fresh PCB Concepts: Traceability in PCB Design
Fresh PCB Concepts: Tariffs and the Importance of a Diverse Supply Chain
Fresh PCB Concepts: PCB Stackup Strategies—Minimizing Crosstalk and EMI for Signal Integrity