-
- News
- Books
Featured Books
- smt007 Magazine
Latest Issues
Current IssueWhat's Your Sweet Spot?
Are you in a niche that’s growing or shrinking? Is it time to reassess and refocus? We spotlight companies thriving by redefining or reinforcing their niche. What are their insights?
Moving Forward With Confidence
In this issue, we focus on sales and quoting, workforce training, new IPC leadership in the U.S. and Canada, the effects of tariffs, CFX standards, and much more—all designed to provide perspective as you move through the cloud bank of today's shifting economic market.
Intelligent Test and Inspection
Are you ready to explore the cutting-edge advancements shaping the electronics manufacturing industry? The May 2025 issue of SMT007 Magazine is packed with insights, innovations, and expert perspectives that you won’t want to miss.
- Articles
- Columns
- Links
- Media kit
||| MENU - smt007 Magazine
eSMART Factory Conference 2019, Day 2
September 4, 2019 | Happy Holden, I-Connect007Estimated reading time: 11 minutes
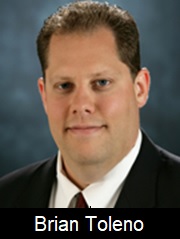
Editor’s note: Click here to read about Day 1.
On the second day of the eSMART Factory Conference in June in Dearborn, Michigan, Trevor Galbraith, the conference chair, introduced the keynote speaker, Brian Toleno, Ph.D. His keynote was titled "Augmented Reality: Next-Generation Computing for Front-Line Workers."
Brian Toleno is the director of Microsoft’s Virtual Reality Group in Mountain View, California. His keynote highlighted the overview of the growing technologies of mixed reality (MR)—the third wave of computing. Toleno started with a thorough history of MR developments. The MR spectrum is made up of augmented reality (AR) and virtual reality (VR).
Around the 1950s, inventors began trying to make head-mounted displays (HMD) with TV visors and evolving with flat-panel displays to being smaller, lighter, and more dynamic. With the increase in resolution for smartphones, 2012 brought the first of the modern HMDs. The technology is accelerating, and by 2025, MR will change the way that we work, learn, and get things done. Uses for MR will include remote assistance, training and task guidance, collaborative visualization, and contextual data access.
Providing value for improving skills, boosting productivity and efficiency, and empowering first-line workers, an example of the HMD for these tasks is the new Microsoft HoloLens 2. Its characteristics include:
- 2X field of view
- Fully articulated hand tracking
- 3X more comfortable with balanced weight distribution
- Flip-up visor
- Support software from third-party/industry solutions
- Integrated to cloud computing
All of this power provides opportunities to create a new vision for work and training, such as:
- Remote assist: Technicians solve problems in real-time with help of remote experts; manager walk the job site without being on-site; actional information now into view
- Guides: Engage employees with hands-on learning; generate data to improve processes; improve training effectiveness
- Layout: Experience room layouts in real-world scale; edit physical designs easily; move from concept to completion with confidence
- Product visualize: Visualize products using MR; seamless sales integration; add voice notes and annotations
Michael Ford of Aegis Corporation gave the second presentation of the day titled “Human Automation: Hands-Free Industry 4.0,” which addressed the opportunity for AR to improve human work instructions and training. Ford started with a review of AR in the military, automobiles, and early adopters in gaming. The challenge for industry was in finding a cost-effective application, which turned out to be work instructions.
Ford continued with an excellent review of work instruction evolution (WIE):
- Old school: The apprentice
- Mass production: Repetitive work
- Complex assembly: Paper-based work instructions
- Modern assembly: Electronic displays
- Smart factory assembly: Digital operator cockpit (direct data-driven)
- Next-generation smart factory: Hands-free operator cockpit (AR digital-driven virtual assistant)
- AR-assisted human with robot cooperation: Will provide an opportunity for a new definition of work
The third presenter was unable to attend, so Brian Toleno and Michael Ford led a roundtable discussion of MR.
The fourth presentation was by Jamison Shaver of SWIM on “Smart Factories: Solving Real-Rime Data Challenges for Predictive Maintenance.” Shaver has focused on the data challenges for predictive maintenance.
There are several barriers when leveraging data for insights on maintenance:
- Data volume: Large and inefficient using traditional methods
- Latency: Batch processing delays results
- Expertise: Leveraging data scientists and machine-learning (ML) algorithms is challenging
- Cost: Solutions or infrastructure may be expensive
To transition to the smart factory, start with your infrastructure and data insights. Select software that:
- Uses an object-oriented architecture
- Design for web agents (similar to web pages)
- Programmed as a digital representation of the object to be modeled, real or abstract
- Composed together with application logic
- Dynamically instantiated and updated from the data
- Captures domain expertise
- Process faults and other important metrics
- ML algorithms dynamically build a model and learn
- Allow the model to self-train over time, improving accuracy and removing false positives
- Incorporate business rules (i.e., conditions for an alarm)
- Format intuitive dashboards for the line engineer
Apply distributed computing with the following:
- Compose applications
- Incorporate monitoring, alerts, and insights into apps
- Lightweight web apps provide design flexibility
- Decouple applications from infrastructure
- Run on existing equipment (e.g., six machines, 10GB RAM)
- Application can migrate between edge and cloud
- Deployment flexibility
The benefits to be gained include:
- Less infrastructure
- Reduced data transport, server, and database fees
- Leverage the available compute at the edge
- Distribute the solution as necessary
- Reusable solutions
- Design provides simplicity and flexibility in building apps
- ML models are tailored to local conditions
- Domain/local knowledge is captured and applied
- Integrations are repeatable and allow applications to collaborate with existing software solutions
The resulting benefits, as noted earlier, also include higher productivity, lower costs, and empowerment of line personnel to “keep products moving at the highest quality levels.”
John Johnson of Electronic Assembly Products gave the fifth presentation about “Digitization of Manual Assembly Process on Your Shop Floor,” covering the benefits of creating a smart factory using the digital twin and digital shadow to model your manual assembly processes.
Johnson focused on low-volume and high-mix assembly processes with their many variants. Instead of relying on the traditional approach of increased training, poka-yoke, manual quality control (QC) inspection, and more to create complex assembly instructions, more continuous training and education, and extensive resource planning. These can lead to lower productivity and higher error rates during vacation or sick leave, increased customer complaints, higher quality assurance (QA) costs, and decreased productivity by >20%.
Johnson advocates a digital assistant system, consisting of automatic quality control, operator overall equipment effectiveness (OEE) availability, digitized variants, no training required, and understanding problems on the line as they occur. Overall, the idea behind digital assistant (DA) is to remove errors from the assembly process and create flexibility in production including variants (including production down to lot size of one, which still requires shop floor experts) all by the digitization of your analog processes.
The DA creates these solutions to increase the assembly operator OEE by:
- Guiding the worker through the process with real-time verification by the same DA system
- Making training, poka-yoke and separate final inspection unnecessary
- Producing digital data for manual steps and verifying
Johnson concluded by providing an example of DA innovations at Wielputz Corporation where they assemble complex automotive components. The resulting benefits were:
- Savings in lead-time by 1–2 days
- Savings due to cycle time reduction and zero parts per million (PPM) of $1,100 per user month
- Savings in fixture costs of $570
- A reduction of assembly-related complaint costs of >$1,000
- No stress on the assemblers as errors and complaints were eliminated
The final presentation of the morning was “Reducing the Fake Electronic Component Ingress Using Blockchain” by Radu Diaconescu of Swissmic S.A.
Diaconescu presented a very interesting presentation about using blockchain to certify components. He started with an overview of blockchain as well as the current status of the modern electronics supply chain. Then, Diaconescu demonstrated how blockchain could be used to eliminate fake components.
It was very useful that he explained what and how blockchain is used in cryptocurrencies transactions. Many in the audience were not that familiar with the data structure, including me. Diaconescu described that blockchain is a structure that stores data chronologically in blocks that are chained together in a continuously growing series. It operates as a distributed digital ledger where participants must reach consensus to record any new input.
Blockchain’s capabilities include the following:
- Data consolidation can speed up processing time in supply chains
- Verification of product or process characteristics can take less time and be more effective
- Visualization of real-time supply chain situations can lead to process improvement and quick identification of issues
- Its use of zero-knowledge proofs (ZKP), which is a method that one party (“the prover”) can convince another party (“the verifier”) about the truthfulness of a statement
- The protocol conveys nothing apart from the veracity of the statement (ZKP), maintains the privacy of data by design, and ensures the authenticity of a transaction without accessing its details
The modern supply chain has many challenges, such as:
- Margin erosion and sudden demand changes
- Ineffective risk management
- Lack of end to end visibility
- Obsolescence of systems
- Security of the supply chain is as strong as the weakest firewall
The smart manufacturing industrial Cloud (SMIC) application can combine blockchain and IoT to allow sensors and tamper-proof packaging to track the history, location, and usage of physical assets by:
- Automatic detection of IP infringements
- Machine-to-machine (M2M) communication on the factory floor
- Recurrent payments for commercial operations
- Crowdfunding authentication
- Product recall management
- Traceability of components
- Conflict resolution by automatics defaults
Diaconescu concluded, “Trust takes years to build, seconds to break, and forever to repair.”
The final three speakers of the day addressed subjects on smart factory inspection and test. The first was by Joel Scutchfield of Koh Young America substituting for David Suh, discussing “Combining Advanced Process Control (APC) With Feedback to Revolutionize PCBA.” His presentation was a short overview of how artificial intelligence (AI) helps in the data collection and interpretation for solder paste inspection (SPI), 3D automated optical inspection (AOI) and automated X-ray inspection (AXI) and detection.
Scutchfield opened with an obligatory overview of Industry 4.0 and all it can offer (when it gets here). His focus was the opportunity that AI-powered platforms can provide for SM assembly by autonomously collecting data to predict the effects of fine-tuning the complex process. Although Scutchfield mentioned it in passing, CFX is the protocol that can make this possible by combining inspection with printers and mounters.
The AI applications enable an APC model-based software to predict the conditions for optimum productivity while ensuring maximum yields by:
- "Detecting and correcting" during the assembly process saving costs rather than finding defects after final test
- Spotting trends in process behavior earlier in the process to avoid rejections during functional test
- Identifying pasting and placement issues before reflowing
Further, unique machines can be connected that might limit the process. Shrinking components require smaller apertures and finer solder, which complicates printing. Also, 70% of PCBA defects are attributed to the print process. APC can actively address the process with real-time data and SPI measurements to optimize print parameters (improvement in reduction of different mounter defect types. In testing, the AI software conducts an automatic Design of Experiment (DOE) by changing the printer parameter.
Scutchfield concluded with the advice that M2M and Industry 4.0 efforts can alter manufacturing to improve performance and first pass yields. APC plus feedback (FB) is revolutionizing process optimization and the foundation for the smart factory.
The second talk of the afternoon was by Subodh Kulkarni, Ph.D., of CyberOptics on, “3D Inspection and Measurement for Factory Automation Across Applications.” This presentation was a recap of their progress with implementing smart factory data analytics of 3D component inspection.
Kulkarni opened with a justification of the increasing need for process control in SMTA and SEMI driven by high-end components and semiconductors. The need to detect critical defects and measure critical parameters continue to increase at a 100% level. The need is for XYZ measurements that will allow AI analysis in real-time. Examples may be:
- Tall components next to small components
- Very tiny components (and getting smaller)
- Shiny and mirror-like surfaces
- Various packaging options
- Wafer-scale fabrications
One of the new innovations is multiple-reflection suppression sensor technology (MRS) that can:
- Detect and suppress multiple reflections in critical highly accurate inspection and measurements
- Use multiple sensors that can simultaneously capture data in parallel for a speed advantage
- Use sophisticated fusing algorithms to create precise 3D images with four 3D sensors
This requires over 100 images per field of view (FOV) collected in
MRS technology excels in challenging applications, such as:
- Shiny surfaces
- In areas of occlusion
- When a region can only be seen by a single camera
- For components and features near the inside corner of two vertical walls
- With sharper contrast than other technologies
- With highly needed metrology capability
Kulkarni concluded by noting that MRS is coupled with support for M2M communication using CFX. Advanced process control needs are met to detect critical defects or measure critical parameters for the smart factory.
The final talk was “Inspection 4.0” by Keith Bryant. This industry consultant ended the formal presentations with a summary of challenges for AXI, 3D AOI, and off-line X-ray to achieve closed-loop solutions. He opened with another overview of Industry 4.0.
Since this presentation was about inspection, Bryant started with in-line X-ray inspection (AXI), specifically, head-in-pillow (HIP) defects. Lead-free has a greater prevalent for this weak solder joint while having some connectivity for electrical integrity. Thus, in-line AXI tries to find HIP by looking for balls that are smaller or larger than their neighbors’ and trying to eliminate the false fail rates for these systems. Searching for HIP defects requires high-resolution oblique-view images. The capability of 3D AOI to detect HIP is limited by not being able to see underneath any device, and a conclusive decision cannot be made if the solder joints of the devices are still acceptable. Thus, the answer is an off-line, at-line X-ray system as a high-end sensor to compensate for the limitations of AXI or 3D AOI.
Benefits of using a smart factory closed-loop solution might include:
- The inspection and verification time is dramatically reduced
- 3D AOI is now a much more meaningful tool
- Full data integration gives process owners the tools needed for correct decisions
- The verification process becomes at least 6.5X more efficient
- The first-time pass yield of the line can increase from 90% to 99.5%.
Bryant concluded by saying, “Per current AXI and 3D AOI performance, it is beneficial to utilize AXI or 3D AOI equipment jointly with an at-line X-ray system for process improvement, faster throughput. and better yields, leading to lower production costs.”
The day concluded with a panel discussion moderated by Michael Ford on the day’s subjects of AR and smart factory inspection and test.
Although it was interesting to hear about the many benefits of Industry 4.0 and the smart factory, I wish someone would start their presentation by explaining how you justify investing in a smart factory, where to start, and how to transition. If you’re interested in finding the answers to these questions, download I-Connect007’s free Automation and Advanced Procedures in PCB Fabrication. Visit I-007eBooks.com to download this book and other educational titles.
The conference was co-organized by SMTA and Global SMT, and presentations will be available to SMTA members after September in the SMTA Knowledge Base.
Suggested Items
Driving Innovation: Direct Imaging vs. Conventional Exposure
07/01/2025 | Simon Khesin -- Column: Driving InnovationMy first camera used Kodak film. I even experimented with developing photos in the bathroom, though I usually dropped the film off at a Kodak center and received the prints two weeks later, only to discover that some images were out of focus or poorly framed. Today, every smartphone contains a high-quality camera capable of producing stunning images instantly.
Hands-On Demos Now Available for Apollo Seiko’s EF and AF Selective Soldering Lines
06/30/2025 | Apollo SeikoApollo Seiko, a leading innovator in soldering technology, is excited to spotlight its expanded lineup of EF and AF Series Selective Soldering Systems, now available for live demonstrations in its newly dedicated demo room.
Indium Corporation Expert to Present on Automotive and Industrial Solder Bonding Solutions at Global Electronics Association Workshop
06/26/2025 | IndiumIndium Corporation Principal Engineer, Advanced Materials, Andy Mackie, Ph.D., MSc, will deliver a technical presentation on innovative solder bonding solutions for automotive and industrial applications at the Global Electronics A
Fresh PCB Concepts: Assembly Challenges with Micro Components and Standard Solder Mask Practices
06/26/2025 | Team NCAB -- Column: Fresh PCB ConceptsMicro components have redefined what is possible in PCB design. With package sizes like 01005 and 0201 becoming more common in high-density layouts, designers are now expected to pack more performance into smaller spaces than ever before. While these advancements support miniaturization and functionality, they introduce new assembly challenges, particularly with traditional solder mask and legend application processes.
Knocking Down the Bone Pile: Tin Whisker Mitigation in Aerospace Applications, Part 3
06/25/2025 | Nash Bell -- Column: Knocking Down the Bone PileTin whiskers are slender, hair-like metallic growths that can develop on the surface of tin-plated electronic components. Typically measuring a few micrometers in diameter and growing several millimeters in length, they form through an electrochemical process influenced by environmental factors such as temperature variations, mechanical or compressive stress, and the aging of solder alloys.