Chemists Uncover a Mechanism Behind Doping Organic Semiconductors
September 16, 2019 | University of California - Santa BarbaraEstimated reading time: 3 minutes
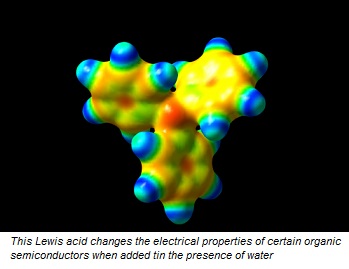
Semiconductors — and our mastery of them — have enabled us to develop the technology that underpins our modern society. These devices are responsible for a wide range of electronics, including circuit boards, computer chips and sensors.
The electrical conductance of semiconductors falls between those of insulators, like rubber, and conductors, like copper. By doping the materials with different impurities, scientists can control a semiconductor’s electrical properties. This is what makes them so useful in electronics.
Scientists and engineers have been exploring new types of semiconductors with attractive properties that could result in revolutionary innovations. One class of these new materials is organic semiconductors (OSCs), which are based on carbon rather than silicon. OSCs are lighter and more flexible than their conventional counterparts, properties that lend themselves to all sorts of potential applications, such as flexible electronics, for instance.
In 2014, UC Santa Barbara’s Professor Thuc-Quyen Nguyen and her lab first reported on doping of OSCs using Lewis acids to increase the conductance of some semiconducting polymers; however, no one knew why this increase happened until now.
Through a collaborative effort, Nguyen and her collages have parsed this mechanism, and their unexpected discovery promises to grant us greater control over these materials. The work was supported by the Department of Energy and the findings appear in the journal Nature Materials.
Researchers at UC Santa Barbara collaborated with an international team from the University of Kentucky, Humboldt University of Berlin and Donghua University in Shanghai. “The doping mechanism using Lewis acids is unique and complex; therefore, it requires a team effort,” Nguyen explained.
“That’s what this paper is all about,” said lead author Brett Yurash, a doctoral candidate in Nguyen’s lab, “figuring out why adding this chemical to the organic semiconductor increases its conductivity.”
“People thought it was just the Lewis acid acting on the organic semiconductor,” he explained. “But it turns out you don’t get that effect unless water is present.”
Apparently, water mediates a key part of this process. The Lewis acid grabs a hydrogen atom from the water and passes it over to the OSC. The extra positive charge makes the OSC molecule unstable, so an electron from a neighboring molecule migrates over to cancel out the charge. This leaves a positively charged “hole” that then contributes to the material’s conductivity.
“The fact that water was having any role at all was really unexpected,” said Yurash, the paper’s lead author.
Most of these reactions are performed in controlled environments. For instance, the experiments at UC Santa Barbara were conducted in dry conditions under a nitrogen atmosphere. There wasn’t supposed to be any humidity in the chamber at all. However, clearly some moisture had made it into the box with the other materials. “Just a tiny amount of water is all it took to have this doping effect,” Yurash said.
Scientists, engineers and technicians need to be able to controllably dope a semiconductor in order for it to be practical. “We’ve totally mastered silicon,” he said. “We can dope it the exact amount we want and it’s very stable.” In contrast, controllably doping OSCs has been a huge challenge.
Lewis acids are actually pretty stable dopants, and the team’s findings apply fairly broadly, beyond simply the few OSCs and acids they tested. Most of the OSC doping work has used molecular dopants Which don’t dissolve readily in many solvents “Lewis acids, on the other hand, are soluble in common organic solvents, cheap, and available in various structures,” Nguyen explained.
Understanding the mechanism at work should enable researchers to purposefully design even better dopants. “This is hopefully going to be the springboard from which more ideas launch,” Yurash said. Ultimately, the team hopes these insights help push organic semiconductors toward broader commercial realization.
Testimonial
"In a year when every marketing dollar mattered, I chose to keep I-Connect007 in our 2025 plan. Their commitment to high-quality, insightful content aligns with Koh Young’s values and helps readers navigate a changing industry. "
Brent Fischthal - Koh YoungSuggested Items
Trouble in Your Tank: Minimizing Small-via Defects for High-reliability PCBs
08/27/2025 | Michael Carano -- Column: Trouble in Your TankTo quote the comedian Stephen Wright, “If at first you don’t succeed, then skydiving is not for you.” That can be the battle cry when you find that only small-diameter vias are exhibiting voids. Why are small holes more prone to voids than larger vias when processed through electroless copper? There are several reasons.
The Government Circuit: Navigating New Trade Headwinds and New Partnerships
08/25/2025 | Chris Mitchell -- Column: The Government CircuitAs global trade winds continue to howl, the electronics manufacturing industry finds itself at a critical juncture. After months of warnings, the U.S. Government has implemented a broad array of tariff increases, with fresh duties hitting copper-based products, semiconductors, and imports from many nations. On the positive side, tentative trade agreements with Europe, China, Japan, and other nations are providing at least some clarity and counterbalance.
How Good Design Enables Sustainable PCBs
08/21/2025 | Gerry Partida, Summit InterconnectSustainability has become a key focus for PCB companies seeking to reduce waste, conserve energy, and optimize resources. While many discussions on sustainability center around materials or energy-efficient processes, PCB design is an often overlooked factor that lies at the heart of manufacturing. Good design practices, especially those based on established IPC standards, play a central role in enabling sustainable PCB production. By ensuring designs are manufacturable and reliable, engineers can significantly reduce the environmental impact of their products.
50% Copper Tariffs, 100% Chip Uncertainty, and a Truce
08/19/2025 | Andy Shaughnessy, I-Connect007If you’re like me, tariffs were not on your radar screen until a few months ago, but now political rhetoric has turned to presidential action. Tariffs are front-page news with major developments coming directly from the Oval Office. These are not typical times. President Donald Trump campaigned on tariff reform, and he’s now busy revamping America’s tariff policy.
Global PCB Connections: Understanding the General Fabrication Process—A Designer’s Hidden Advantage
08/14/2025 | Markus Voeltz -- Column: Global PCB ConnectionsDesigners don’t need to become fabricators, but understanding the basics of PCB fabrication can save you time, money, and frustration. The more you understand what’s happening on the shop floor, the better you’ll be able to prevent downstream issues. As you move into more advanced designs like HDI, flex circuits, stacked vias, and embedded components, this foundational knowledge becomes even more critical. Remember: the fabricator is your partner.