New Structural Design Could Lead to Self-Deploying Tents or Adaptive Robotic Fins
September 30, 2019 | MITEstimated reading time: 6 minutes
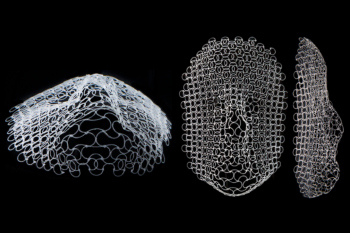
Researchers at MIT and elsewhere have designed 3-D printed mesh-like structures that morph from flat layers into predetermined shapes, in response to changes in ambient temperature. The new structures can transform into configurations that are more complex than what other shape-shifting materials and structures can achieve.
Image Caption: A lattice structure, originally printed flat, has morphed into the outline of a human face after changing in response to the surrounding temperature. Perspective view (left), top view (middle), and side view (right) of transformed lattice, approximately 160mm tall. Credit: Lori K. Sanders
As a demonstration, the researchers printed a flat mesh that, when exposed to a certain temperature difference, deforms into the shape of a human face. They also designed a mesh embedded with conductive liquid metal, that curves into a dome to form an active antenna, the resonance frequency of which changes as it deforms.
The team’s new design method can be used to determine the specific pattern of flat mesh structures to print, given the material’s properties, in order to make the structure transform into a desired shape.
The researchers say that down the road, their technique may be used to design deployable structures, such as tents or coverings that automatically unfurl and inflate in response to changes in temperature or other ambient conditions.
Such complex, shape-shifting structures could also be of use as stents or scaffolds for artificial tissue, or as deformable lenses in telescopes. Wim van Rees, assistant professor of mechanical engineering at MIT, also sees applications in soft robotics.
“I’d like to see this incorporated in, for example, a robotic jellyfish that changes shape to swim as we put it in water,” says van Rees. “If you could use this as an actuator, like an artificial muscle, the actuator could be any arbitrary shape that transforms into another arbitrary shape. Then you’re entering an entirely new design space in soft robotics.”
Van Rees and his colleagues are publishing their results this week in the Proceedings of the National Academy of Sciences. His co-authors are J. William Boley of Boston University; Ryan Truby, Arda Kotikian, Jennifer Lewis, and L. Mahadevan of Harvard University; Charles Lissandrello of Draper Laboratory; and Mark Horenstein of Boston University.
Gift wrap’s limit
Two years ago, van Rees came up with a theoretical design for how to transform a thin flat sheet into a complex shape such as a human face. Until then, researchers in the field of 4-D materials — materials designed to deform over time — had developed ways for certain materials to change, or morph, but only into relatively simple structures.
“My goal was to start with a complex 3-D shape that we want to achieve, like a human face, and then ask, ‘How do we program a material so it gets there?’” van Rees says. “That’s a problem of inverse design.”
He came up with a formula to compute the expansion and contraction that regions of a bilayer material sheet would have to achieve in order to reach a desired shape, and developed a code to simulate this in a theoretical material. He then put the formula to work, and visualized how the method could transform a flat, continuous disc into a complex human face.
But he and his collaborators quickly found that the method wouldn’t apply to most physical materials, at least if they were trying to work with continuous sheets. While van Rees used a continuous sheet for his simulations, it was of an idealized material, with no physical constraints on the amount of expansion and contraction it could achieve. Most materials, in contrast, have very limited growth capabilities. This limitation has profound consequences on a property known as double curvature, meaning a surface that can curve simultaneously in two perpendicular directions — an effect that is described in an almost 200-year-old theorem by Carl Friedrich Gauss called the Theorema Egregium, Latin for “Remarkable Theorem.”
If you’ve ever tried to gift wrap a soccer ball, you’ve experienced this concept in practice: To transform paper, which has no curvature at all, to the shape of a ball, which has positive double curvature, you have to crease and crumple the paper at the sides and bottom to completely wrap the ball. In other words, for the paper sheet to adapt to a shape with double curvature, it would have to stretch or contract, or both, in the necessary places to wrap a ball uniformly.
To impart double curvature to a shape-shifting sheet, the researchers switched the basis of the structure from a continuous sheet to a lattice, or mesh. The idea was twofold: first, a temperature-induced bending of the lattice’s ribs would result in much larger expansions and contractions of the mesh nodes, than could be achieved in a continuous sheet. Second, the voids in the lattice can easily accommodate large changes in surface area when the ribs are designed to grow at different rates across the sheet.
The researchers also designed each individual rib of the lattice to bend by a predetermined degree in order to create the shape of, say, a nose rather than an eye-socket.
Page 1 of 2
Suggested Items
Copper Price Surge Raises Alarms for Electronics
07/15/2025 | Global Electronics Association Advocacy and Government Relations TeamThe copper market is experiencing major turbulence in the wake of U.S. President Donald Trump’s announcement of a 50% tariff on imported copper effective Aug. 1. Recent news reports, including from the New York Times, sent U.S. copper futures soaring to record highs, climbing nearly 13% in a single day as manufacturers braced for supply shocks and surging costs.
Symposium Review: Qnity, DuPont, and Insulectro Forge Ahead with Advanced Materials
07/02/2025 | Barb Hockaday, I-Connect007In a dynamic and informative Innovation Symposium hosted live and on Zoom on June 25, 2025, representatives from Qnity (formerly DuPont Electronics), DuPont, and Insulectro discussed the evolving landscape of flexible circuit materials. From strategic corporate changes to cutting-edge polymer films, the session offered deep insight into design challenges, reliability, and next-gen solutions shaping the electronics industry.
Indium Corporation Expert to Present on Automotive and Industrial Solder Bonding Solutions at Global Electronics Association Workshop
06/26/2025 | IndiumIndium Corporation Principal Engineer, Advanced Materials, Andy Mackie, Ph.D., MSc, will deliver a technical presentation on innovative solder bonding solutions for automotive and industrial applications at the Global Electronics A
Gorilla Circuits Elevates PCB Precision with Schmoll’s Optiflex II Alignment System
06/23/2025 | Schmoll MaschinenGorilla Circuits, a leading PCB manufacturer based in Silicon Valley, has enhanced its production capabilities with the addition of Schmoll Maschinen’s Optiflex II Post-Etch Punch system—bringing a new level of precision to multilayer board fabrication.
Day 1: Cutting Edge Insights at the EIPC Summer Conference
06/17/2025 | Pete Starkey, I-Connect007The European Institute for the PCB Community (EIPC) Summer Conference took place this year in Edinburgh, Scotland, June 3-4. This is the second of three articles on the conference. The other two cover the keynote speeches and Day 2 of the technical conference. Below is a recap of the first day’s sessions.